NEW WAYS TO [SIGN
Page 114
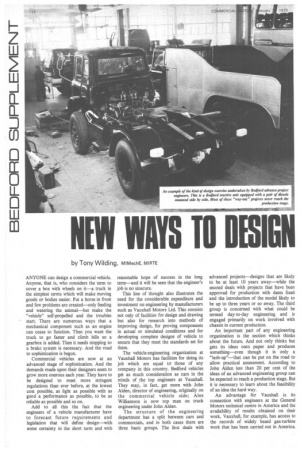
Page 115
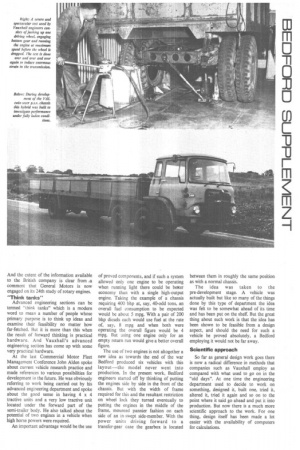
Page 116
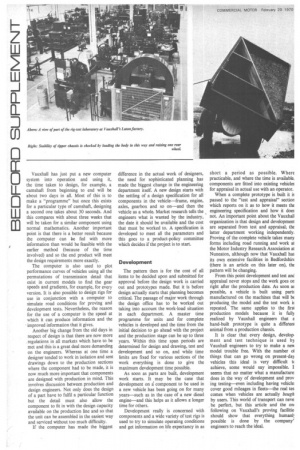
If you've noticed an error in this article please click here to report it so we can fix it.
by Tony Wilding, mlMechE, MIRTE
ANYONE can design a commercial vehicle. Anyone, that is, who considers the term to cover a box with wheels on it—a truck in the simplest terms which will make moving goods or bodies easier. Put a horse in front and few problems are created—only feeding and watering the animal—but make the "vehicle" self-propelled and the troubles start. There are numerous ways that a mechanical component such as an engine can cease to function. Then you want the truck to go faster and climb hills so a gearbox is added. Then it needs stopping so a brake system is necessary. And the road to sophistication is begun.
Commercial vehicles are now at an advanced stage of sophistication. And the demands made upon their designers seem to grow more onerous each year. They have to be designed to meet more stringent regulations than ever before, at the lowest cost possible, as light as possible with as good a performance as possible, to be as reliable as possible and so on.
Add to all this the fact that the engineers of a vehicle manufacturer have to forecast future requirements and legislation that will define design—with some certainty in the short term and with reasonable hope of success in the long term—and it will be seen that the engineer's job is no sinecure.
This line of thought also illustrates the need for the considerable expenditure and investment on engineering by manufacturers such as Vauxhall Motors Ltd. This consists not only of facilities for design and drawing but also for research into methods of improving design, for proving components in actual or simulated conditions and for developing complete designs of vehicle to ensure that they meet the standards set for them.
The vehicle-engineering organization at Vauxhall Motors has facilities for doing its job which are equal to those of any company in this country. Bedford vehicles get as much consideration as cars in the minds of the top engineers at Vauxhall. They may, in fact, get more with John Alden, director of engineering, originally on the commercial vehicle side; Alex Williamson is now top man on truck engineering under John Alden.
The structure of the engineering department has a split between cars and commercials, and in both cases there are three basic groups. The first deals with advanced projects—designs that are likely to be at least 10 years away—while the second deals with projects that have been approved for production with dates fixed and the introduction of the model likely to be up to three years or so away. The third group is concerned with what could be termed day-to-day engineering and is engaged primarily on work involved with chassis in current production.
An important part of any engineering organization is the section which thinks about the future. And not only thinks but gets its ideas onto paper and produces something—even though it is only a "lash-up"—that can be put on the road to allow practical assessment. According to John Alden less than 20 per cent of the ideas of an advanced engineering group can be expected to reach a production stage. But it is necessary to learn about the feasibility of an idea the hard way.
An advantage for Vauxhall is its connection with engineers at the General Motors technical centre in America and the availability of results obtained on their work. Vauxhall, for example, has access to the records of widely based gas-turbine -Work that has been carried out in America.
And the extent of the information available to the British company is clear from comment that General Motors is now engaged on its 24th study of rotary engines.
"Think tanks"
Advanced engineering sections can be termed -think tanks" which is a modern word to mean a number of people whose primary purpose is to think up ideas and examine their feasibility no matter how far-fetched. But it is more than this when the result of forward thinking is practical hardware. And Vauxhall's advanced engineering section has come up with some very practical hardware.
At the last Commercial Motor Fleet Management Conference John Alden spoke about current vehicle research practice and made references to various possibilities for development in the future. He was obviously referring to work being carried out by his advanced engineering department and spoke about the good sense in having 4 x 4 tractive units and a very low tractive unit located under the forward part of the semi-trailer body. He also talked about the potential of two engines in a vehicle when high horse powers were required.
An important advantage would be the use of proved components, and if such a system allowed only one engine to be operating when running light there could be better economy than with a single high-output engine. Taking the example of a chassis requiring 400 bhp at, say, 40-odd tons, an overall fuel consumption to be expected would be about 5 mpg. With a pair of 200 bhp diesels each would use fuel at the rate of, say, 8 mpg and when both were operating the overall figure would be 4 mpg. But using one engine only for an empty return run would give a better overall figure.
The use of two engines is not altogether a new idea as towards the end of the war Bedford produced six vehicles with this layout--the model never went into production. In the present work, Bedford engineers started off by thinking of putting the engines side by side in the front of the chassis. But with the width of frame required for this and the resultant restriction on wheel lock they turned eventually to putting the engines in the middle of the frame, mounted pannier fashion on each side of an in swept side-member. With the power units driving forward to a transfer-gear case the gearbox is located
between them in roughly the same position as with a normal chassis.
The idea was taken to the pre-development stage. A vehicle was actually built but like so many of the things done by this type of department the idea was felt to be somewhat ahead of its time and has been put on the shelf. But the great thing about such work is that the idea has been shown to be feasible from a design aspect, and should the need for such a vehicle be proved absolutely, a Bedford employing it would not be far away.
Scientific approach So far as general design work goes there is now a radical difference in methods that companies such as Vauxhall employ as compared with what used to go on in the "old days". At one time the engineering department used to decide to work on something, designed it, built one, tried it, altered it, tried it again and so on to the point where it said go ahead and put it into production. But now there is a much more scientific approach to the work. For one thing, design itself has been made a lot easier with the availability of computers for calculations. Vauxhall has just put a new computer system into operation and using it, the time taken to design, for example, a camshaft from beginning to end will be about two days in all. Most of this is to make a "programme" but once this exists for a particular type of camshaft, designing a second one takes about 30 seconds. And this compares with about three weeks that will be taken for a similar component using normal mathematics. Another important point is that there is a better result because the computer can be fed with more information than would be feasible with the earlier method (because of the time involved) and so the end product will meet the design requirements more exactly.
The computer is also used to plot performance curves of vehicles using all the permutations of transmission detail that exist in current models to find the gear speeds and gradients, for example, for every version. It is also possible to design rigs for use in conjunction with a computer to simulate road conditions for proving and development tests. Nevertheless, the reason for the use of a computer is the speed at which it can produce information and the • improved information that it gives.
Another big change from the old days in respect of design is that there are now more . regulations in all markets which have to be met and this is a great deal more demanding on the engineers. Whereas at one time a designer tended to work in isolation and sent drawings down to the production sections where the component had to be made, it is now much more important that components are designed with production in mind. This involves discussion between production and design engineers. Not only does the design of a part have to fulfil a particular function but the detail must also allow the component to fit in with the design capacity available on the production line and so that the unit can be assembled in the easiest way and serviced without too much difficulty.
If the computer has made the biggest difference in the actual work of designers, the need for sophisticated planning has made the biggest change in the engineering department itself. A new design starts with the settling of a design specification for all components in the vehicle—frame, engine, axles, gearbox and so on—and then the vehicle as a whole. Market research tells the engineers what is wanted by the industry, the date it should be available and the cost that must be worked to. A specification is developed to meet all the parameters and this goes to a product-policy committee which decides if the project is to start.
Development
The pattern then is for the cost of all items to be decided upon and submitted for approval before the design work is carried out and prototypes made. But it is before design actually starts that planning becomes critical. The passage of major work through the design office has to be worked out taking into account the work-load situation in each department. A master time programme for units and for complete vehicles is developed and the time from the initial decision to go ahead with the project and the production stage can be up to three years. Within this time span periods are determined for design and drawing, test and development and so on, and while time limits are fixed for various sections of the work everything is done to give the maximum development time possible.
As soon as parts are built, development work starts. It may be the case that development on i. component to be used in a new vehicle has been going on for many years—such as in the case of a new diesel engine—and this helps as it allows a longer time for others.
Development really is concerned with components and a wide variety of test rigs is used to try to simulate operating conditions and get information on life expectancy in as short a period as possible. Where practicable, and where the time is available. components are fitted into existing vehicles for appraisal in actual use with an operator.
When a complete prototype is built it is passed to the "test and appraisal" section which reports on it as to how it meets the engineering specification and how it does. not. An important point about the Vauxhall organization is that design and development are separated from test and appraisal, the latter department working independently. Proving of the complete vehicle takes many forms including road running and work al the Motor Industry Research Association at Nuneaton, although now that Vauxhall has its own extensive facilities in Bedfordshire (there is an article on this later on), the pattern will be changing.
From this point development and test anc appraisal never stops and the work goes or right after the production date. As soon as possible, a vehicle is built using parts manufactured on the machines that will lx producing, the model and the test work is repeated. The same applies to the first production models because it is fully realized by Vauxhall engineers that z hand-built prototype is quite a different animal from a production chassis.
It is clear that every design, development and test technique is used by Vauxhall •engineers to try to make a new model trouble free. With the number ol things that can go wrong on present-day vehicles this ideal is very difficult te achieve, some would say impossible. I seems that no matter what a manufacture does in the way of development and prov ing testing—even including having vehicle cover good mileages in fleets—the real tes comes when vehicles are actually bough by users. This world of transport can neve be perfect, but this article and the on following on Vauxhall's proving facilitie should show that everything humanl: possible is done by the company' engineers to reach the ideal.