A Tight Hand on
Page 48
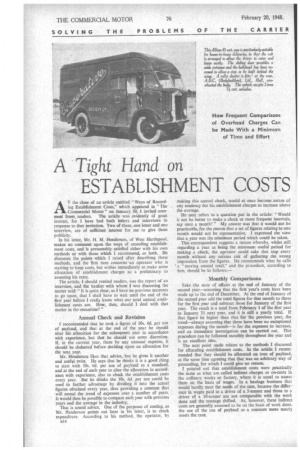
Page 51
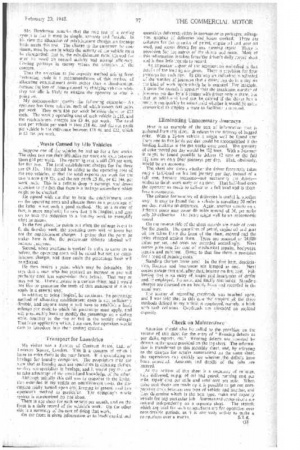
If you've noticed an error in this article please click here to report it so we can fix it.
ESTABLISHMENT COSTS
AT the close of an article entitled Ways of Recording Establishment Costs," which appeared in" The Commercial Motor" on January 30, I invited comment from, readers. The article was evidently of great interest, for I have had both letters and interviews in .response to that invitation. Two of these, one letter and one interview, are of sufficient interest for me to give them publicity.
In his letter, Me H. M. Henderson, of West Hartlepool, makes no comment upon the ways of recording establishment costs, and is presumably satisfied either with his own methods or with those which I recommend, or both. He discusses the points which I raised alter describing those methods, and the first item concerns,an operator who is starting to keep costs, but wishes immediately to make some allocation of establishment charges as a preliminary to assessing his rates. The article, I should remind readers, Was the report -of an interview, and the haulier with whom I was discussing the matter said: It is quite clear, as I have no previous accounts to go upon, that I shalt have to wait until the end of the first year before I really know what our total annual establishment costs are. How, then, should I deal with that matter in the meantime?"
Annual Check and Revision
I recommended that he took a figure of Ws. 6d. per ton of payload, and that at the end of the year he should alter his allocation for the subsequent year in accordance with experience, but that he should use some discretion. If, in the current year, there be any unusual expense, it should be deducted before deciding upon an allocation for the next year.
Mr. Henderson likes that advice, but he gives it another and useful twist. He says that be thinks it is a good thing to start with 10s. 6d. per ton of payload as a standard, and at the end of each year to alter the allocation in accordance with experience, also to cheek the establishment costs every year. But he thinks the 10s. 6d. per ton could be used to further advantage by dividing it into the actual figures obtained every year, thus providing a constant that will reveal the trend of expenses over a number of years. It would then be posak to compare each year with previous years and the average in the industry.
That is sound advice. One of the purposes of costing, as Mr. Henderson points out later in his letter, is to check expenditure. According to his method, the operator, by making this annual check, would at once become aware of any tendency for his establishment charges to increase above the average.
He next refers to a question put in the article: "Would it not be better to make a check at more frequent intervals, say once a month?" My answer was that it would not be practicable., for the reason that a set of figitres relating to one month would not be representative. I expressed the view that a year was the minimum period which could be taken.
This correspondent suggests a means whereby, whilst still regarding a year as being the minimum useful period for making a check, the operator could take that step every month without any serious risk of gathering the wrong impression from the figures. He recommends what he calls 'a "moving annual total," and the procedure, according to him, should be as follows:—
. Monthly Comparisons Take the state of affairs at the end of January of the second year—assuming that the first year's costs have been made up to the end of December. At the end of January of the second year add the total figures for that month to those for the first year and subtract those for January of the first year. The result is a total from February I of the first year to January 31 next year, and it is still a yearly total. If that figure be higher than that for the previous year, the trend—always assuming that there have been no exceptional expenses during the month—is for the expenses to increase, and an immediate investigation can be carried out. This procedure can be followed monthly throughout the year and is an excellent idea.
The next point made relates to the methods t discussed for allocating establishment costs. In the article I recommended that they should be allocated on tons of payload, at the same time agreeing that that was an arbitrary way of proceeding, for which I could give no reason: I pointed out that establishment -costs were practically the same as what are called indirect charges or on-costs in the ordinary works or factory, where it is usual to assess them on the basis of wages. In a haulage business that would hardly meet the needs of the case, because the difference in wages paid to a driver of a 5-tenner and those to a driver of a 10-tonner are not comparable with the work done and the tonnage shifted. As, however, these indirect costs are generally assumed to be on the basis of work done, the use of the ton of payload as a constant mere nearly meets the case.
Mr. Henderson remarks that the true test of a costing system is that it must be simple, accurate and 'flexible." In his view the allocation of establishment charges .on tonnage basis meets this test. The charge to the customer, he continues, must be one in which the activity of the vehicle must be disregarded; that is, the establishment rates allowed for must be based on normal activity and normal• efficiency. Costing portrays in money values the activities of the concern.
Thus the objection to the capacity method arising from fluctuating trade is a recommendation of 'this method of allocating establishment costs rather than a disadvantage, . because the loss of mone*caused by charging vehicles while they are idle is likely to awaken •theoperator to 'what is going on.
My correspondent quotes the following example:—An operator has three vehicles, each of which covers 600 miles per week. They earn £66 per week between them, or £22 each. The weekly operating cost of each vehicle is £15, and the establishment charges are £3 4s. per week. The total cost per vehicle. per week is thus £18 4s., and the net profit per vehicle is the difference between £18 4s. and £22, which is £3 16s. per week.
Waste Caused by Idle Vehicles
Suppose one of .the vehicles, be laid up for a few weeks. The other two run their 600 miles per week and earn between them £44 per week. The operating cost is still £30 per week for the two. The total establishment charges 'for the, three are £9 12s. This should be added to the operating cost of the two vehicles, so that the total expense per week for the two is now £39 12s. and the net profit £5 .8s., or £2 14s. per week each. This .is a definite drop in earnings, and draws attention to the fact that there is a leakage somewhere which ought to be checked.
-He agreed with ..me. that to base the establishment costs on the operating costs and allocate them as a percentage of the latter is not such a good. method. He, as a matter of fact, is more emphatic; he says that it is illogical, and goes on to take the reduction to a five-day week to exemplify what he means,
In the first place, he points out when the mileage is cut to • fit the five-day week, the operating costs will be lower but not the establishment charges. I gather that the point he makes here is that the percentage hitherto adopted will become incorrect. • Second, when overtime is worked in order, to carry on as before, the operating costs will be raised but not the establishment charges, and there again the percentage basis will be affected. .
He then makes a point which may be debatable. He says that a man who has received an increase in pay, will probably need less supervision than before. That may or may not be. Human nature is a curious thing, and I would not like to guarantee the truth of that statement if it is to apply in a general way.
In addition to being illogical,, he continues, the percentage method of allocating establishment costs is not sufficiently flexible, and anyone using it will have to establish a basic mileage per week to which his Percentage Must apply, and will presumably, have to Modify the percentage an a sliding scale, contrary to the rise or fall in the weekly mileage. That is an application which, I am sure, few operators would care to introduce into their costing systems.
Transport for Laundries My visitor was a director of Contract Autos, Ltd., of Leicester Square, .London. This is a concern of which I hope to write More in the near future. It is specializing'on haulage for laundry companies. The proprietors take the view that as laundry. men are specialists in cleaning clothes, so they are specialists in haulage, and it would pay the one to take advantage of the specialized knowledge of the other.
Although initially this call was in response to the invitation extended in my article on establishment 'costs, the discussion really turned upon cost keeping in general and this operators method in particular. , The company's whole system is summarized on One sheet. • There is one sheet for each vehicle per month, and on the front is a daily record of the vehicle's work. On the other side is a summary of the cost of doing that work.
On the front is given information as to loads carried and quantities delivered, either in tonnage or in packages, mileage run, number of deliveries and hours worked. There are columns for the quantity of petrol, engine oil and gear oil used, and stores drawn for any running repair There is provision for the names of the driver and mate. Most of . this information is taken from the' driver's daily record sheet and is thus little trouble to record.
An important aspect of the information embodied is that details of the loading are given. There is provision for,four journeys for each day. In this way an indication is afforded of the number of journeys that a driver can do in a day on the kind of work upon which he is engaged For example, if from the records it appears that the maximum number of journeys per day by ,a 6-tonner with driver only is three, but that an additional load can be carried if the driver_ has a mate, it can quickly be ascertained whether it would be more economical to employ a mate to facilitate turnrouncl.
Eliminating Unnecessary Journeys
Here' is an example of the sort of information that is gathered from this sheet. It relates to the delivery of bagged coke. With a 2i-ton vehicle it might well be found that from one to five loads per day could be accomplished if the loading facilities at the gas works were good. The quantity of coke moved per day would be l2i tons. With a 3-tonner it might be found possible to deliver 12 tons or the full 1.21 tons on only four journeys per day. That; obviously, would be an economy.
The sheet also shows whether the driver frequently takes only a half-load on his last journey per day, instead of a full one, because someone—not necessarily the driver— wishes to finish work early or on time. That half-load costs the operator as much to deliver as a full load and is therefore uneconomic.
The column for-number of deliveries is useful in another way. It may be found that a vehicle is travelling 30 miles per day, making 60 deliveries. Again, another vehicle on a different route may cover 40 mites instead of 30, yet make only 30 deliveries. The latter might well be an uneconomic round.
On the reverse side of the sheet records are made of costs for the month. The quantities of petrol, engine oil and gear oil are taken from the front of the sheet, entered and the price charged against them. _ Tyres are assessed at 24,000
miles per, set, and costs are recorded accordingly. Next comes provision for cost of mechanical repairs, bodywork repairs and .painting. Down to that line there. is provision for a total of running costs.
Standing charges come next In the first iteni, depre..ciation, licences and insurances are lumped as one. Next comes garage rent and, after that, interest on first cost. Following that is an entry of Wages' and .insurances of driver and if etriPloyed, the mate, and finally overheads. Standing charges are assessed on an hourly:basis and recorded in the usual way
• The matter of recording overheads was touched upon, and I was fold that in this case the simplest of the three methods defined in my article is employed,namely, a book With cash columns. Overheads are allocated on payload capacity.
Check on Maintenance
Attention should also be called to the provision on the reverse of this sheet for the entry of "Running defects as per daily, reports, etc." Running defects are reported by drivers in the space provided on the log sheet The information is transferred to this monthly sheet, and, by referring to the charges for repairs summarized on the same sheet, the supervisors can quickly see whether . the defects have been _remedied. Amounts and details of the jobs are entered.
At the bottom of this sheet is a summary of mileage, tons delivered; m.p.g. of oil and petrol, running cost per mile, repair cost per mile and total. cost per mile. When these coat Sheets are made up it is possible to get out comparative costs between one type orvehicle and another, and thus determine which is the best type, make and capacity vehicle for any particular job. Summarized comparisons are entered independently on a separate sheet. The records which are used for such comparisons are for operation over consideralile periods, as it is obviously unfair to make a
comparison over a month. S.T.R.