A NEW METHOD OF RADIATOR CONSTRUCTION.
Page 12
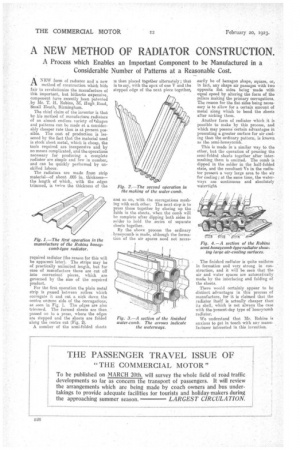
If you've noticed an error in this article please click here to report it so we can fix it.
A Process which Enables an Important Component to be Manufactured in a Considerable Number of Patterns at a Reasonable Cost.
ANEW form of radiator and a new method of construction which bids fair to revolutionize the manufacture of this important, but hitherto expensive, component have recently been patented .by Mr. T. H. Robins, 38-, Ilugh.Road, Small Heath, Birmingham.
The chief claim of the inventor is that by his method of manufacture radiators of an almost endless variety of 'shapes and patterns can be made at a considerably cheaper rate than is at present, possible. The cost of production is lessened by the fact that the material used is stock sheet metal, which is cheap, the tools required are inexpensive and by no means complicated, and the operations necessary for producing a complete radiator are simple and few in number, and can be quickly performed by unskilled labour.
The radiators are made from strip material—of about .005 in. thickness— the length of which,, with the edges trimmed, is twiee the thickness of the required radiator (the reason for this will be apparent later). The strips may be of practically unlimited length, but for case of manufacture these are cut off into convenient pieces, which are governed by the size of the required product.
For the first operation the plain metal strip is passed between rollers which corrugate it and cut a nick down the centre on tone side of the *corrugations, as seen in Fig. 1. The edges; are also trimmed. The formed sheets are then passed on to a press, where the edges are stepped and the sheets are folded along the centre cut (Fig. 2).
A number of the semi-folded sheets is then placed together alternately; that is to say, with the apex of one V and the stepped edge of the next piece together,
and so on, with the corrugations meshing with each other. The next step is to press these together by closing up the folds in the sheets, when the comb will be complete after dipping both sides in solder to hold the aeries of separate sheets together.
By the above process the ordinary honeycomb is made, although the formation of the air spaces need not neces sexily be of hexagon shape, square, or, in fact, any shape air passages with two opposite Hat sides being made with equal speed by altering the form of the rollers making the primary corrugations. The reason for the fiat sides being necessary is to allow for a certain amount of metal along which to bend the sheets after nicking them.
Another form of radiator which it is possible to make by this process, and which may possess certain advantages in presenting a greater surface for air cooling than the ordinary pattern, is known as the semi-honeycomb.
This is made in *a similar way to the other, but the operation of pressing the semi-folded sheets together after intermeshing them is omitted. The comb is dipped in the solder in the half-folded state, and the resultant•Vs in the radiator present a very large area to the air for cooling; at the same time, the waterways are continuous and absolutely watertight, The finished radiator is quite uniform in formation and very strong in construction, and it will be seen that the air and water spaces are automatically made by the interlacing and folding of the sheets.
There would certainly appear to be distinct advantages in this process of manufacture, for it is claimed that the radiator itself is actually cheaper than its shell, which is not always the case with the Present-day type of honeycomb radiator.
We understand that Mr. Robins is anxious to get in touch with any manufacturer interested in this invention.