GOOD AS NEW
Page 30
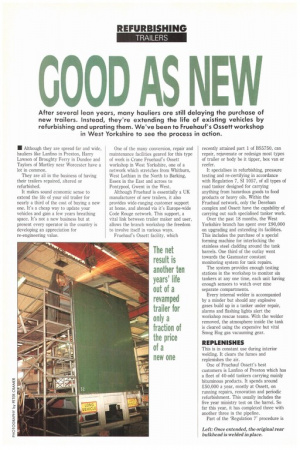
Page 31
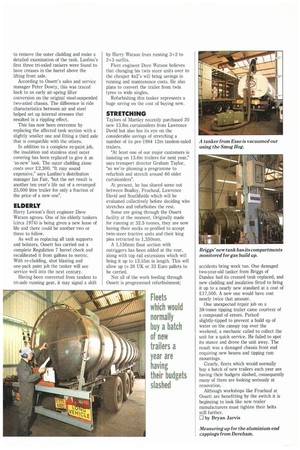
If you've noticed an error in this article please click here to report it so we can fix it.
After several lean years, many hauliers are still delaying the purchase of new trailers. Instead, they're extending the life of existing vehicles by refurbishing and uprating them. We've been to Fruehauf's Ossett workshop in West Yorkshire to see the process in action.
• Although they are spread far and wide, hauliers like Lanfino in Preston, Harry Lawson of Broughty Ferry in Dundee and Taylors of Martley near Worcester have a lot in common.
They are all in the business of having their trailers repaired, altered or refurbished.
It makes sound economic sense to extend the life of your old trailer for nearly a third of the cost of buying a new one. It's a cheap way to update your vehicles and gain a few years breathing space. It's not a new business but at present every operator in the country is developing an appreciation for re-engineering value. One of the many conversion, repair and maintenance facilities geared for this type of work is Crane Fruehauf's Ossett workshop in West Yorkshire, one of a network which stretches from Whitburn, West Lothian in the North to Barking, Essex in the East and across to Pontypool, Gwent in the West.
Although Fruehauf is essentially a UK manufacturer of new trailers, it also provides wide-ranging customer support at home, and abroad via it's Europe-wide Code Rouge network. This support, a vital link between trailer maker and user, allows the branch workshop the freedom to involve itself in various ways.
Fruehauf's Ossett facility, which recently attained part 1 of BS5750, can repair, rejuvenate or redesign most types of trailer or body be it tipper, box van or reefer.
It specialises in refurbishing, pressure testing and re-certifying in accordance with Regulation 7, SI 1057, of all types of road tanker designed for carrying anything from hazardous goods to food products or heavy oils. Within the Fruehauf network, only the Dereham complex and Ossett have the capability of carrying out such specialised tanker work.
Over the past 18 months, the West Yorkshire branch has spent over £90,000 on upgrading and extending its facilities. This includes the purchase of a special forming machine for interlocking the stainless steel cladding around the tank barrels. One third of the outlay went towards the Gasmaster constant monitoring system for tank repairs.
The system provides enough testing stations in the workshop to monitor six tankers at any one time, each unit having enough sensors to watch over nine separate compartments.
Every internal welder is accompanied by a minder but should any explosive gases build up in a tanker under repair, alarms and flashing lights alert the workshop rescue teams. With the welder removed, the atmosphere inside the tank is cleared using the expensive but vital Smog Hog gas vacuuming gear.
REPLENISHES
This is in constant use during interior welding. It clears the fumes and replenishes the air.
One of Fruehauf Ossett's best customers is Lanfino of Preston which has a fleet of 40-odd tankers carrying mainly bituminous products. It spends around £50,000 a year, mostly at Ossett, on running repairs, renovation and periodic refurbishment. This usually includes the five year ministry test on the barrel. So far this year, it has completed three with another three in the pipeline.
Part of the 'Regulation 7' procedure is to remove the outer cladding and make a detailed examination of the tank. Lanfino's first three tri-axled tankers were found to have creases in the barrel above the lifting front axle.
According to Ossett's sales and service manager Peter Dowty, this was traced back to an early air-spring lifter conversion on the original steel-suspended two-axled chassis. The difference in ride characteristics between air and steel helped set up internal stresses that resulted in a rippling effect.
This has now been overcome by replacing the affected tank section with a slightly smaller one and fitting a third axle that is compatible with the others.
In addition to a complete re-paint job, the insulation and stainless steel outer covering has been replaced to give it an 'as-new look. The outer cladding alone costs over £2,300. "It may sound expensive," says Lanfino's distribution manager Ian Fair, "but the net result is another ten year's life out of a revamped 25,000 litre trailer for only a fraction of the price of a new one".
ELDERLY
Harry Lawson's fleet engineer Dave Watson agrees. One of his elderly tankers (circa 1974) is being given a new lease of life and there could be another two or three to follow.
As well as replacing all tank supports and bolsters, Ossett has carried out a complete Regulation 7 barrel check and recalibrated it from gallons to metric. With re-cladding, shot blasting and one-pack paint job the tanker will see service well into the next century.
Having been converted from tandem to tri-axle running gear, it may signal a shift by Harry Watson from running 3+2 to 2+3 outfits.
Fleet engineer Dave Watson believes that changing his twin steer units over to the cheaper 4x2's will bring savings in running and maintenance costs. He also plans to convert the trailer from twin tyres to wide singles.
Refurbishing this tanker represents a huge saving on the cost of buying new.
STRETCHING
Taylors of Martley recently purchased 20 new 13.6m curtainsiders from Lawrence David but also has its eye on the considerable savings of stretching a number of its pre-1984 12m tandem-mded trailers.
"At least one of our major customers is insisting on 13.6m trailers for next year," says transport director Graham Taylor, "so we're planning a programme to refurbish and stretch around 60 older curtainsiders".
At present, he has shared some out between Boalloy, Fruehauf, Lawrence David and Southfields which will be evaluated collectively before deciding who stretches and refurbishes the rest.
Some are going through the Ossett facility at the moment. Originally made for running at 32.5 tonnes, they are now having their necks re-profiled to accept twin-steer tractive units and their king pins retracted to 1,350mm.
A 1,150mm floor section with outriggers has been added at the rear, along with top rail extensions which will bring it up to 13.55m in length. This will allow up to 26 UK or 33 Euro pallets to be carried.
Not all of the work feeding through Ossett is programmed refurbishment; accidents bring work too. One damaged two-year-old tanker from Briggs of Dundee had its creased tank replaced, and new cladding and insulation fitted to bring it up to a nearly new standard at a cost of £17,500. A new one would have cost nearly twice that amount.
One unexpected repair job on a 38-tonne tipping trailer came courtesy of a compound of errors. Parked slightly-tipped to prevent a build up of water on the canopy top over the weekend, a mechanic called to collect the unit for a quick service. He failed to spot its stance and drove the unit away. The result was a damaged chassis front end requiring new beams and tipping ram mountings.
Clearly, fleets which would normally buy a batch of new trailers each year are having their budgets slashed, consequently many of them are looking seriously at renovation.
Although workshops like Fruehauf at Ossett are benefitting by the switch it is beginning to look like new trailer manufacturers must tighten their belts still further.
El by Bryan Jarvis Measuring up for the aluminium end cappings from Dereham.