Shaped-for
Page 11
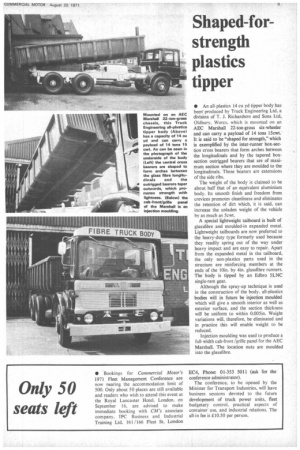
If you've noticed an error in this article please click here to report it so we can fix it.
strength plastics tipper
• An all-plastics 14 cu yd tipper body has been produced by Truck Engineering Ltd. a division of T. J. Richardson and Sons Ltd, Oldbury. Worcs. which is mounted on an AEC Marshall 22-ton-gross six-wheeler and can carry a payload of 14 tons 15cwt. It is said to be "shaped for strength," which is exemplified by the inter-runner box-section cross bearers that form arches between the longitudinals and by the tapered boxsection outrigged bearers that are of maximum section where they are moulded to the longitudinals. These bearers are extensions of the side ribs.
The weight of the body is claimed to be about half that of an equivalent aluminium body. Its smooth finish and freedom from crevices promotes cleanliness and eliminates the retention of dirt which, it is said, can increase the unladen weight of the vehicle by as much as 5cwt.
A special lightweight tailboard is built of glassfibre and moulded-in expanded metal. Lightweight tailboards are now preferred to the heavy-duty type formerly used because they readily spring out of the way under heavy impact and are easy to repair. Apart from the expanded metal in the tailboard, the only non-plastics parts used in the structure are reinforcing members at the ends of the 10in. by 4in. glassfibre runners. The body is tipped by an Edbro 5LNC single-ram gear.
Although the spray-up technique is used in the construction of' the body, all-plastics bodies will in future be injection moulded which will give a smooth interior as well as exterior surface, and the section thickness will be uniform to within 0.005in. Weight variations will, therefore, be eliminated and in practice this will enable weight to be reduced.
Injection moulding was used to produce a full-width cab-front /grille panel for the AEC Marshall. The location nuts are moulded into the glassfibre.