Applying Hard-facing Alloy to Wearing Surfaces
Page 48
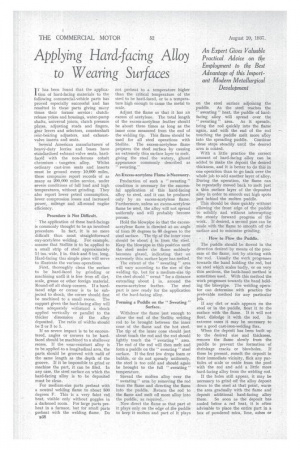
Page 49
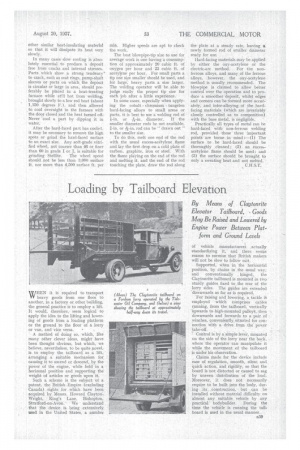
If you've noticed an error in this article please click here to report it so we can fix it.
An Expert Gives Valuable Practical Advice on the Employment to the Best Advantage of this Important Modern Metallurgical Development
1.1. has been found that the applica tion of hard-facing materials to the following commercial-vehicle parts has proved especially successful and has resulted in these parts giving many times their former service : dutchrelease yokes and housings, water-pump shafts, universal joints, clutch pressure plates, adjusting studs and fingers, gear levers and selectors, countersha It sear-bearing adjusters, and exhaustvalve inserts and seats.
Several American manufacturers of heavY-duty lorries and buses have standardized exhaust-valve seats, hardfaced with the non-ferrous cobalt chromium tungsten alloy. Whilst ordinary cast-iron seats and inserts must be ground every 10,000 miles, these companies report records of as many as 200,000 miles service, under severe conditions of full load and high temperatures, without grinding. They also report lower petrol consumption, lower compression losses and increased power, mileage and all-round engate efficiency.
Procedure is Not Difficult.
The application of these hard-facings is commonly thought to be an involved procedure. In fact, it is no more difficult than most straightforward oxy-acetylene welding. For example, . assume that Stellite is to be applied to a small strip of steel approximately 11 ins, wide, in. thick and 8 ins. long. Hard-facing this simple piece will serve to illustrate the various operations.
First, thoroughly clean the surface to be hard-faced by grinding or machining until it is free from all dirt, scale, grease or other foreign material. Round-off all sharp corners. If a hardfaced edge or corner is to be subjected to shock, the corner should first he machined to a small recess. The support given the bard-facing alloy will then adequately withstand a shock applied vertically or parallel to the thicker dimension of the alloy deposited. The ratio of widths should be 2 or 3 to I.
If no severe impact is to he encountered, angles or corners to be hardfaced should be machined to a shallower recess. TI the wear-resistant alloy is to be applied-to a longitudinal area, the parts should be grooved with radii of the same length as the depth of the groove. If it be impossible to grind or machine the part, it can he hied. In any case, the steel surface on which the hard-facing alloy is to be deposited must be clean.
For medium-size parts preheat with a neutral welding flame to about 800 degrees F. This is a very faint red heat, visible only without goggles in a darkened room. For large parts preheat in a furnace, but for small parts preheat with the welding flame. Do B38 not preheat to a temperature higher than the critical temperature of the steel to be hard-faced, or to a temperature high enough to cause the metal to scale.
Adjust the flame so that it has an excess of acetylene. The total length of the excess-acetylene feather should be about three times as long as the inner cone measured from the end of the Welding tip. This flame should be used for all steel operations with Stelae. The excess-acetylene flame prepares the steel surface by causing an extremely thin surface layer to melt, giving the steel the watery, glazed appearance commonly described as "sweating."
An Excess-acetyIene Flame is Necessary.
Production of such a " sweating " condition is necessary for the successful application of this hard-facing alloy to steel, and it can be produced only by an excess-acetylene flame. Furthermore, unless an excess-acetylene flame be used, the alloy will not spread uniformly and will probably become porous.
Hold the blowpipe o that the excessacetylene flame is directed at an angle of from 30 degrees to 60 degrees to the steel surface. The tip of the inner cone should be about in from the steel. Keep the blowpipe in this position until the steel under the flame suddenly becomes glazed, indicating that an extremely thin surface layer has melted.
The extent of the " sweating " area will vary according to the size of the welding tip, but for a medium-size tip the steel should " sweat" for a distance extending about in. around the excess-acetylene feather. The steel part is now ready for the application of the hard-facing alloy.
Forming a Puddle on the " Sweating " Surface.
Withdraw the flame just enough to allow the end of the Stellite welding rod to be brought between the inner cone of the flame and the hot steel. The tip of the inner cone should just about touch the rod and the rod should lightly touch the " sweating " area. The end of the rod will then melt and form a puddle on the " sweating" steel surface. If the first few drops foam or bubble, or do not spready uniformly, the steel is too cold and should again be brought to the full " sweating " temperature.
Spread the molten alloy over the "
sweating" area by removing the rod from the flame and directing the flame into the puddle. Return the rod to the flame and melt off more alloy into the puddle, as required,
Now direct the flame so that part ot it plays only on the edge of the puddle to keep it molten and part of it plays on the steel surface adjoining the puddle. As the steel reaches the " sweating " heat, the puddle of hardfacing alloy will spread over the " sweating " area. As it spreads. bring the rod quickly into the flame again, and with the end of the rod touching the puddle melt more alloy into the spreading puddle. Continue these steps steadily until the desired area is coated.
With a little practice the correct amount of hard-facing alloy can be added to make the deposit the deSired thickness, and it is better to do this in one operation than to go back over the whole job to add another layer of alloy. During the operation, the flame can be repeatedly moved back to melt just a thin surface layer of the deposited alloy in order to smooth out high spots just behind the molten puddle.
This should be done quickly without allowing the front edge of the puddle to solidify and without interrupting the .steady forward progress of the work. If desired, a second pass can be made with the flame to smooth off the surface and to minimize grinding,
How to Flow the Puddle.
The puddle should be flowed in the direction desired by means of the pressure of the flame, not by stirring with the rod. Usually the work progresses towards the hand holding the rod, but on steel which scales badly, or on very thin sections, the back-hand method is sometimes used. With this method the work progresses towards the hand bolding the blowpipe. The welding operator can determine with practice the preferable method for any particular job.
If any dirt or scale appears on the steel or in the puddle, float it to the surface with the flame. If it will not float, dislodge it with the rod. In extreme cases it may be necessary to use a good east-iron-welding flux.
When the deposit has been built up to the desired size and thickness. remove the flame slowly from the puddle to prevent the formation of shrinkage cracks or blowholes. If these be present, remelt the deposit in their immediate vicinity, flick any particles of scale or oxide from the pool with the rod and add a little more hard-facing alloy from the welding rod.
If the holes still appear, it may be necessary to grind off the alloy deposit down to the steel at that point, warm the area gradually with the flame and deposit additional hard-facing alloy there. So soon as the deposit has cooled below a red heat, it is often advisable to place the entire part in a box of powdered mica, lime, ashes or other similar heat-insulating material so that it will dissipate its heat very
In many cases slow cooling is absolutely essential to produce a deposit free from cracks and internal stresses. Parts which show a strong tendency' to crack, such as seat rings, pump-shaft sleeves or parts on which the deposit is circular Or large in area, should preferably be placed in a heat-treating furnace while still hot from welding, brought slowly to a low red heat (about 1,150 degrees F.), and then allowed to cool overnight in the furnace with the door closed and the heat turned off.Never -cool a part by dipping it in water.
After the hard-faced part has cooled, it may be necessary to remove the high spots or grind the hard-faced surface to an exact size. Any soft-grade vitrified wheel, not coarser than 46 or finer than 69 in grade I or J, is suitable for grinding Stellite. The wheel speed should not be less than 3,000 surface ft. nor more than 4,500 surface ft. per min. Higher speeds are apt to check the work.
The best blowpipe-tip size to use for average work is one having a consumption of approximately 20 cubic ft. of oxygen per hour and 23 cubic ft. of acetylpie per hour. For smart parts a tip one size smaller should be used, and for large, heavy parts a size larger. The welding operator will be able to judge easily the proper tip size for each Job after a little experience.
In some cases, especially when applying the cobalt chromium tungsten hard-facing alloys to small areas or parts, it is best to use a welding rod of i-in. or diameter. If the smaller diameter rods be not available, t-in. or rod can be" drawn out " to the smaller size.
To do this, melt one end of the rod with the usual excess-acetylene flame and lay the first drop on a cold plate of carbon, graphite, iron or steel. With the flame playing on the end of the rod and melting it, and the end of the rod touching the plate, draw the rod along
the plate at a steady rate, leaving a newly formed rod of smaller diameter ready for use.
Hard-facing materials may be applied by either the nay-acetylene or the electric-arc method. For the nonferrous alloys, and many of the ferrous alloys, however, the oxy-acetylene method is usually recommended. The blowpipe is claimed to allow better control over the operation and to produce a smoother deposit, whilst edges and corners can be 'formed more accurately, and inter-alloying of the hardfacing materials (which are invariably closely controlled as to composition) with the base Metal, is negligible. • Practically all types of metal can be hard-faced with non-ferrous welding rod, provided these three important points are borne in mind :----(1) The surface to be hard-faced should be thoroughly cleaned ; (2) an exc-essacetylene flame should be used : and (3) the surface should be brought to only a sweating heat and not melted.