Three-pronged attack
Page 39
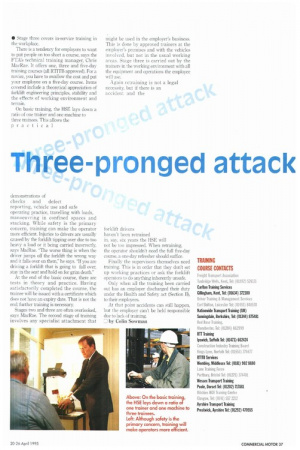
Page 38
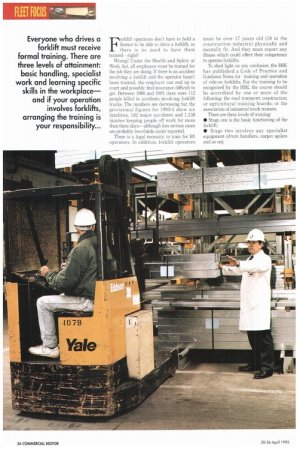
If you've noticed an error in this article please click here to report it so we can fix it.
Everyone who drives a forklift must receive formal training. There are three levels of attainment: basic handling, specialist work and learning specific skills in the workplace— and if your operation involves forklifts, arranging the training is your responsibility...
Forklift operators don't have to hold a licence to be able to drive a forklift, so there is no need to have them trained—right?
Wrong! Under the Health and Safety at Work Act, all employees must be trained for the job they are doing. If there is an accident involving a forklift and the operator hasn't been trained, the employer can end up in court and possibly find insurance difficult to get. Between 1986 and 1991 there were 112 people killed in accidents involving forklift trucks. The numbers are decreasing but the provisional figures for 1993/4 show six fatalities, 182 major accidents and 1,138 injuries keeping people off work for more than three days—although less serious cases are probably two-thirds under reported.
There is a legal necessity to train for lift operators. In addition, forklift operators must be over 17 years old (18 in the construction industry) physically and mentally fit. And they must report any illness which could affect their competence to operate forklifts.
To shed light on any confusion, the HSE has published a Code of Practice and Guidance Notes for training and operation of ride-on forklifts. For the training to be recognised by the HSE, the course should be accredited by one or more of the following: the road transport; construction; or agricultural training boards; or the association of industrial truck trainers.
There are three levels of training: • Stage one is the basic functioning of the forklift; • Stage two involves any specialist equipment (drum handlers, carpet spikes and so on); • Stage three covers in-service training in the workplace.
There is a tendency for employers to want to put people on too short a course, says the ETA's technical training manager, Chris MacRae. It offers one, three and five-day training courses (all RTITB approved). For a novice, you have to swallow the cost and put your employee on a five-day course. Items covered include a theoretical appreciation of forklift engineering principles, stability and the effects of working environment and terrain.
On basic training, the HSE lays down a ratio of one trainer and one machine to three trainees. This allows the practical demonstrations of checks and defect reporting, vehicle use and safe operating practice, travelling with loads, manoeuvring in confined spaces and stacking. While safety is the primary concern, training can make the operator more efficient. Injuries to drivers are usually caused by the forklift tipping over due to too heavy a load or it being carried incorrectly, says MacRae. "The worse thing is when the driver jumps off the forklift the wrong way and it falls over on them," he says. "If you are driving a forklift that is going to fall over, stay in the seat and bold on for grim death."
At the end of the basic course, there are tests in theory and practice. Having satisfactorily completed the course, the trainee will be issued with a certificate which does not have an expiry date. That is not the end; further training is necessary Stages two and three are often overlooked, says MacRae. The second stage of training involves any specialist attachment that might be used in the employer's business. This is done by approved trainers at the employer's premises and with the vehicles involved, but not in the usual working areas. Stage three is carried out by the trainers in the working environment with all the equipment and operations the employee will use.
Again retraining is not a legal necessity, but if there is an accident, and the forklift drivers haven't been retrained in, say. six years the HSI.: will not be too impressed. When retraining. the operator shouldn't need the full five-day course, a one-day refresher should suffice.
Finally the supervisors themselves need training. This is in order that they don't set up working practices or ask the forklift operators to do anything inherently unsafe.
Only when all the training been carried out has an employer discharged their duty under the Health and Safety act (Section II), to their employees.
At that point accidents can still happen, but the employer can't be held responsible due to lack of training.
11 by Colin Sowman