TALKING TO T TIPPERMEN
Page 124
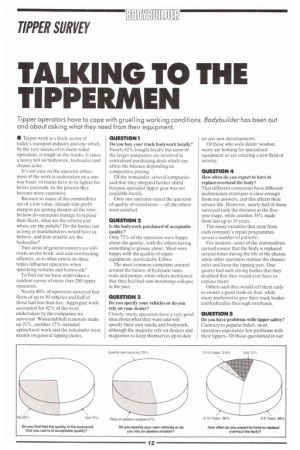
Page 125

If you've noticed an error in this article please click here to report it so we can fix it.
Tipper operators have to cope with gruelling working conditions. Bodybuilder has been out and about asking what they need from their equipment.
• Tipper work is a lively sector of today's transport industry and one which, by the very nature of its many-sided operation, is tough on the trucks. It takes a heavy toll on bodywork, hydraulics and chassis alike.
It's not easy on the operator either; most of the work is undertaken on a oneway basis, so trucks have to be lighter for better payloads. In the process they become more expensive.
Because so many of the commodities are of a low value, already slim profit margins are getting thinner all the time. So how do operators manage to replace their fleets, what are the criteria and where are the pitfalls? Do the bodies last as long as manufacturers would have us believe, and how reliable are the hydraulics?
Two areas of general concern are rollovers on site work, and axle overloading offences, so to what extent do these topics influence operators when specifying vehicles and bodywork?
To find out we have undertaken a random survey of more than 200 tipper operators.
Nearly 80% of operators surveyed had fleets of up to 10 vehicles and half of those had less than five. Aggregate work accounted for 42% of the work undertaken by the companies we surveyed. Waste/rubbish removals made up 21%, another 17% included agricultural work and the remainder were mainly on general tipping duties. QUESTION 1 Do you buy your truck bodywork locally? Nearly 62% bought locally but some of the larger companies are involved in centralised purchasing deals which can affect the balance depending on competitive pricing.
Of the remainder, several companies said that they shopped further afield because specialist tipper gear was not available locally.
Only one operator raised the question of quality of installation — all the others were satisfied.
QUESTION 2 Is the bodywork purchased of acceptable quality?
Only 75% of the operators were happy about the quality, with the others having something to grouse about. Most were happy with the quality of tipper equipment, particularly Edbro, The most common complaint centred around the failure of hydraulic rams, seals and pumps, while others mentioned that they had had ram mountings collapse in the past.
QUESTION 3 Do you specify your vehicles or do you rely on your dealer?
Clearly, many operators have a very good idea about what they want and will specify their own trucks and bodywork, although the majority rely on dealers and magazines to keep themselves up to date on any new developments.
Of those who seek dealer wisdom, many are looking for specialised equipment or are entering a new field of activity.
QUESTION 4 How often do you expect to have to replace/overhaul the body?
That different companies have different maintenance strategies is clear enough from our answers, and this affects their service life. However, nearly half of those surveyed took the decision at the fiveyear stage, while another 36% made them last up to 10 years.
The many variables that stem from each company's repair programmes reveal a number of patterns.
For instance, some of the commodities carried ensure that the body is replaced several times during the life of the chassis while other operators replace the chassis/ axles and keep the tipping part. One quarry had such strong bodies that they doubted that they would ever have to replace them!
Others said they would sell them early to ensure a good trade-in deal, while many preferred to give their truck bodies and hydraulics thorough overhauls.
QUESTION 5 Do you have problems with tipper safety? Contrary to popular belief, most operators experience few problems with their tippers. Of those questioned in our
survey, 92% had avoided the grim spectre of tip-overs although most were well aware of the dangers.
Two managers within council waste departments referred to trouble with loose ground on sites and both had had vehicles slipping and turning over while tipping.
Both felt the solution was extreme care by the driver while on wet or loose ground. but agreed that more stable tipping platforms would be the ideal.
The other main hazard stemmed from the failure of hydraulics systems while tipping. There were several instances of hydraulic rams blowing out, seals failing and ram mountings collapsing, but each of the operators involved said the solution was regular maintenance and safety checks.
Only one operator, moving very heavy aggregate loads, worried about the ability of a front axle to cope in rough conditions.
QUESTION 6 What make of tipping gear do you use, and is it reliable?
The majority of operators surveyed were using Edbro tipping gear and apart from the occasional electronic failure or leakage from the seals they were quite happy with the equipment, saying it was worth the extra cost.
Of the small number of other makes of hydraulics used, there were several instances of reliability problems but the sample sizes are too small to draw conclusions from this.
QUESTION 7
What type of suspension do you favour? Almost 72% of those questioned favoured mechanical suspension. While many preferred steel springs, others used them for economic reasons.
Many would love to have air springs but think it too expensive for the value of the cargo being carried.
They were all aware of the main advantages of fitting pneumatics; smoothness of ride, a big reduction in noise (compared with steel), and its ability to cushion delicate loads from damage.
Several operators expressed concern about going to air because of the extra complexity and maintenance.
QUESTION 8 Is overloading a problem?
The majority of operators questioned (87%) have had no problems with overloading, and most of the instances referred to related to disagreements between truck operators and loaders, particularly where aggregates, waste and crops were concerned.
Drivers often have to rely on the judgement of the loaders and this has led to problems in the past (see Commercial Motor's survey on legislation.
One of the major problems, we were told, was water content. A tipper might pick up a load of dry sugar beet, for example, then transport it (without cover, presumably) across the country, with rain showers adding a tonne or more in the process.
The penalty for breaking the overloading laws makes art investment in a tailored tarp good value and good sense.
QUESTION 9 How do you weigh your trucks?
From the responses to this question, very few companies use any form of on-board weighing equipment. The vast majority (86%) depend on public weighbridges.
Only 10% used on-board weighers while less than 2% made use of pressure pads at their depots or elsewhere. Several operators, particularly those in agricultural or aggregate movements, said they rarely weighed their vehicles because they drove such short distances.