New technology for plastics cab
Page 39
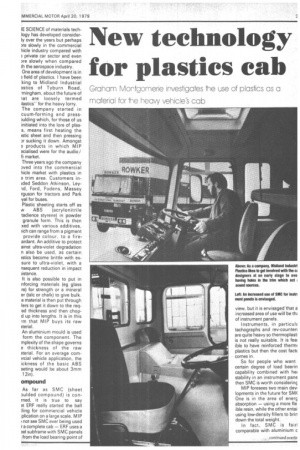
Page 40
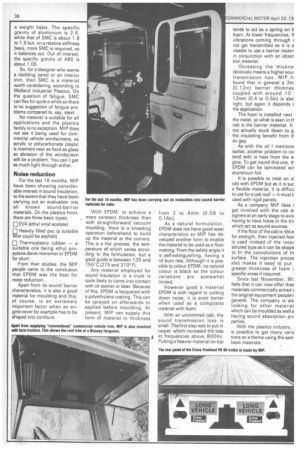
If you've noticed an error in this article please click here to report it so we can fix it.
Graham Mortgomerie investigates the use of plastics as a material for e heavy vehicle's cab
IE SCIENCE of materials techlogy has developed considerly over the years but perhaps )re slowly in the commercial hide industry compared with ) private car sector and even )re slowly when compared th the aerospace industry.
One area of development is in ) field of plastics. I have been king to Midland Industrial 3stics of Tyburn Road, mingham, about the future of lat are loosely termed lastics" for the heavy lorry. The company started in cuum-forming and press)ulding which, for those of us initiated into the lore of plass, means first heating the istic sheet and then pressing )r sucking it down. Amongst a products in which MIP ecialised were for the audio/ fi market.
Three years ago the company )ved into the commercial hide market with plastics in a trim area. Customers inKied Seddon Atkinson, Leyid, Ford, Fodens, Massey rguson for tractors and Park yal for buses.
Plastic sheeting starts off as
N ABS (acrylonitrile tadience styrene) in powder granule form, This is then xed with various additives, lich can range from a pigment provide colour, to a fireardant. An additive to protect ainst ultra-violet degradation n also be used, as certain istics become brittle with exsure to ultra-violet, with a nsequent reduction in impact ;istance.
It is also possible to put in nforcing materials (eg glass re) for strength or a mineral er (talc or chalk) to give bulk. e material is then put through lers to get it down to the reqed thickness and then chopd up into lengths. It is in this -m that MIP buys its raw iterial.
An aluminium mould is used form the component. The mplexity of the shape governs thickness of the raw Iterial. For an average com)rcial vehicle application, the ickness of the basic ABS aeting would be about 3mm 12in).
ompound As far as SMC (sheet Dulded compound) is conrned, it is true to say 3t ERF really started the ball ling for commercial vehicle plication on a large scale. MIP not see SMC ever being used r a complete cab — ERF uses a ael subframe with SMC panels from the load bearing point of
view, but it is envisaged that a increased area of use will be thi of instrument panels.
Instruments, in partiouli. tachographs and rev-counter are quite heavy so thermoplast is not really suitable. It is lea ible to have reinforced therm( plastics but then the cost fact( comes in.
So for people who want certain degree of load bearin capability combined with he stability in an instrument pane then SMC is worth considerinc
MIP foresees two main devi lopments in the future for SMt One is in the area of enerc absorption — using a more fle ible resin, while the other entai using low-density fillers to brir down the total weight.
In fact, SMC is fair] comparable with aluminium c a weight basis. The specific gravity of aluminium is 2.6, while that of SMC is about 1.8 to 1.9 but, on a relative stiffness basis, more SMC is required, so it balances out. Out of interest, the specific gravity of ABS is about 1.05.
So, for a designer who wants a cladding panel or an interior trim, then SMC is a material worth considering, according to Midland Industrial Plastics. On the question of fatigue, SMC can flex for quite a while so there is no suggestion of fatigue problems compared to, say, steel.
No material is suitable for all applications and the plastics family is no exception. MIP does not see it being used for commercial vehicle windscreens, as acrylic or polycarbonate plastic is nowhere near as hard as glass so abrasion of the windscreen will be a problem. You can't get as much light through either.
Noise reduction
For the last 18 months, MIP have been showing considerable interest in sound insulation, to the extent that they have been carrying out an evaluation into all known sound-barrier materials. On the plastics front, there are three basic types:
El EVA (ethyl vinyl acetate) n Heavily filled pvc (a suitable Ner could be asphalt) Ei Thermoplastic rubber — a suitable one being ethyl propylene diene monomer or EPDM for short.
From their studies, the MIP people came to the conclusion that EPDM was the best for noise reduction.
Apart from its sound barrier characteristics, it is also a good material for moulding and this, of course, is an extremely important factor when an engine cover for example has to be shaped into contours. With EPDM, to achieve a more constant thickness than with straightforward vacuum moulding, there is a kneading operation beforehand to build up the material at the corners. This is a hot process, the temperature of which varies according to the formulation, but a good guide is between 135 and 155°C(275 and 310'F).
Any material employed for sound insulation in a truck is quite likely to come into contact with oil sooner or later. Because of this, EPDM is lacquered with a polyethylene coating. This can be sprayed on afterwards or applied before moulding. At present, MIP can supply this form of material in thickness from 2 to 4mm (0.08 to 0.16in).
As a natural formulation, EPDM does not have good wear characteristics so MIP has developed another form to enable the material to be used as a floor matting. From the safety angle it is self-extinguishing, having a nil burn rate. Although it is possible to colour EPDM, its natural colour is black so the colour variations are somewhat limited.
However good a material EPDM is with regard to cutting down noise, it is even better when used as a composite material with foam.
With an untrimmed cab, the sound transmission loss is small. The first step was to put in carpet, which increased the loss at frequencies above 800Hz. Putting a heavier material on top
tends to act as a spring on tl foam. At lower frequencies, tt vibrations coming through not get transmitted so it is a visable to use a barrier materi in conjunction with an absor tion,material.
Increasing the thickne: obviously means a higher sour transmission loss. MIP h; found that in general a 3m (0.12in) barrier thicknes coupled with around 1 0 12mm (0.4 to 0.5in) is abo right, but again it depends the application.
The foam is installed next the metal, so what is seen in cab is the barrier material. It not actually stuck down to g the insulating benefit from flair gap.
As with the oil I mentione earlier, another problem to col tend with is heat from the ei gine. To get round this one, if EPDM can be laminated wii aluminium foil.
It is possible to treat an ol cab with EPDM but as it is suc a flexible material, it is difficu to use for a cab roof — it must h used with rigid panels.
As a company MIP likes 1 get involved with the cab di signers at an early stage to avoi having to have holes in the trir which act as sound sources.
If the floor of the cab is rilke for strength, then injected bar is used instead of the recor stituted type as it can be shape to fit the convolutions of th surface. The injection proces also makes it easy to put greater thickness of foam i specific areas if required.
Since last November, MI feels that it can now offer thes materials commercially aimed a the original equipment people.i general. The company is als looking for other material which can be moulded as well a having sound absorption prc perties.
With the plastics industry, I is possible to get many varia tions on a theme using the sam basic materials.