injection Equipment and "Diesel Knock"
Page 23
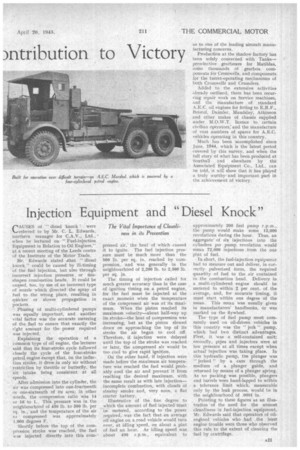
If you've noticed an error in this article please click here to report it so we can fix it.
The Vital Importance of Cleanliness in its Prevention CAUSES of " diesel knock were referred to by Mr. C. L. Edwards, . northern manager for .Ltd., when he lectured on " Fuel-injection
Equipment in Relation to Oil Engines," at a recent meeting of the Leeds centre of the Institute of the Motor Trade.
Mr. Edwards stated .that " diesel knock " could be caused by ill-timing • of the fuel injection, but also through. incorrect injection pressures , or Mis shapen combustion heads. It could be calved, too, by use of an incorrect type of nozzle which directed the spray of fuel to the wrong place, resulting in quicker or slower propagation in pockets.
Phasing of multi-cylindered pumps was equally important, and another vital factor was the accurate metering of the fuel to ensure that exactly the right amount for the power required • was injected.
Explaining the operation of a common type of oil engine, the lecturer said that its four-stroke cycle. followed 'closely the cycle of the four-stroke petrol engine except that, on the induction stroke, it drew in only air without' restriction by throttle or butterfly,. the air intake, being consistent at . all speeds. . After admission into the cylinder, the air was compressed into one-fourteenth
or one-sixteenth Of its area; in .other words, the compression ratio was 14 or 16' to I_ This_pressure was in the
neighbourhood of 450 lb. to 500 lb. per sq. in., and the temperature of the air so compressed was approximately 1.000 degrees F. • 'Shortly. before the top of the corn • pression stroke was reached, the fuel was injected directly into this corn-' pressed air; the heat of which -caused it to ignite. The fuel injection pressure Must be much more than the 500 lb. per sq, in. reached by compression, and was generally in the neighbourhood of 2,200 lb. to 2,500 lb. per sq. In.
The timing of injection called for much greater accuracy than in the case of ignition timing on a petrol engine, for the fuel must be injected at the exact ,rnomeirt when the temperature of the compressed air was at its maximum. When the piston reached its maximum, velocity—about half-way up its stroke—the heat of compressionwas increasing, but as the piston slowed down on approaching the top of its stroke the air began to cool off. Therefore, if injection were delayed until the top of the stroke was reached or later, the compressed air would be too cool to give rapid ignition.
On the other hand, if injection were made before the maximum air temperature was reached the fuel would probably cool the air.and prevent it from reaching. the desired maximum, with the same result as With late injection— incomplete combustion, with clouds of .steamy smoke and, very soon, a flat starter battery.
illustrative of the fine degree to . which the amount of fuel injected must be metered, according to the power required, was the fact that an average oil engine on a road vehicle would turn over, at idling speed, on about a, pint of fuel an. hour. As idling speed was about 400 r.p.m., equivalent to approximately 200 fuel pump the pump would make some 12,000 revolutions during the hour. Thus, an aggregate" of six injections into the cylinders per pump revolution would mean 72,000 injections from the one pint of fuel.
in short, the fuel-injection equipment had to measure out and deliver, in correctly pulverized form, the required quantity of fuel to the air contained in the combustion head. Delivery in rnulti-cylindered engine should be metered to within 2 per cent. of the average, and, for accurate timing, it must start within one degree of the mean. This mean was usually given in manufacturers' handbooks, Or was marked on the flywheel.
The type of fuel pump most corn. moniy used on oil-driven vehicles in this country was the "jerk " pump, which had two distinct advantages. First, it was a self-contained unit; :secondly, pipes and injectors were at low 'pressure at all times except when actual injection was taking place. In this hydraulic pump, the plunger was
" jerked by a cam through the medium of a plunger guide, and returned by means of a plunger spring. As no packing. was possible, plungers and barrels were hand-lapped to within a tolerance limit which, measurable only by the leak process, would be in the neighbourhood Of .0001 in.
Pointing to these figures as an illustration of the need for the utmost cleanliness' in fuel-injection equipment, Mr. Edwards said that operators of oilengined vehicles who ,had ,the least engine trouble were those who observed this rule to the extent of cleaning the fuel by. centrifuge.