A WRENCH TOO FAR
Page 92
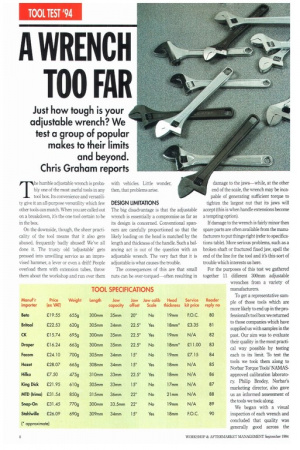
Page 93
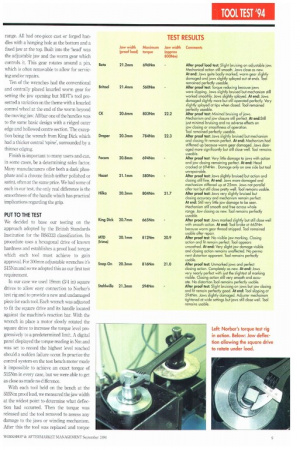
Page 94
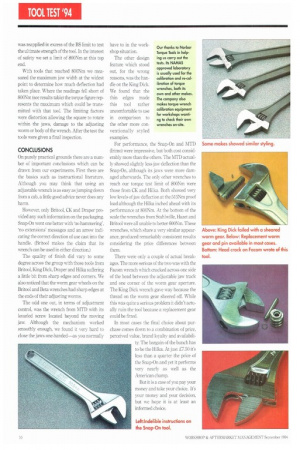
If you've noticed an error in this article please click here to report it so we can fix it.
Just how tough is your
adjustable wrench? We test a group of popular makes to their limits and beyond.
Chris Graham reports
The humble adjustable wrench is probably one of the most useful tools in any tool box. Its convenience and versatility give it an all-purpose versatility which few other tools can match. When you are called out on a breakdown, it's the one tool certain to be in the box.
On the downside, though, the sheer practicality of the tool means that it also gets abused, frequently badly abused! We've all done it. The trusty old 'adjustable' gets pressed into unwilling service as an improvised hammer, a lever or even a drift! People overload them with extension tubes, throw them about the workshop and run over them with vehicles. Little wonder, then, that problems arise.
DESIGN LIMITATIONS
The big disadvantage is that the adjustable wrench is essentially a compromise as far as its design is concerned. Conventional spanners are carefully proportioned so that the likely loading on the head is matched by the length and thickness of the handle. Such a balancing act is out of the question with an adjustable wrench, The very fact that it is adjustable is what causes the trouble.
The consequences of this are that small nuts can be over-torqued—often resulting in damage to the jaws—while, at the other end of the scale, the wrench may be incapable of generating sufficient torque to tighten the largest nut that its jaws will accept (this is when handle extensions become a tempting option).
If damage to the wrench is fairly minor then spare parts are often available from the manufacturers to put things right (refer to specifications table). More serious problems, such as a broken shaft or fractured fixed jaw, spell the end of the line for the tool and it's this sort of trouble which interests us here.
For the purposes of this test we gathered together 11 different 300mm adjustable wrenches from a variety of manufacturers.
To get a representative sample of those tools which are more likely to end up in the professional's tool box we returned to those companies which have supplied us with samples in the past. Our aim was to evaluate their quality in the most practical way possible by testing each to its limit. To test the tools we took them along to Norbar Torque Tools NAMASapproved calibration laboratory, Philip Brodey, Norbar's marketing director, also gave us an informed assessment of the tools we took along.
We began with a visual inspection of each wrench and concluded that quality was generally good across the range. All had one-piece cast or forged handles with a hanging hole at the bottom and a fixed jaw at the top. Built into the 'head' was the adjustable jaw and the worm gear which controls it. This gear rotates around a pin, which is often removable to allow for servicing and/or repairs.
Ten of the wrenches had the conventional and centrally placed knurled worm gear for setting the jaw opening but MDT's tool presented a variation on the theme with a knurled control wheel at the end of the worm beyond the moving jaw. All bar one of the handles was to the same basic design with a ridged outer edge and hollowed centre section. The exception being the wrench from King Dick which had a thicker central 'spine', surrounded by a thinner edging.
Finish is important to many users and can, in some cases, be a determining sales factor. Many manufacturers offer both a dark phosphate and a chrome finish (either polished or satin), often at the same price. We had some of each in our test, the only real difference is the smoothness of the handle which has practical implications regarding the grip.
PUT TO THE TEST We decided to base our testing on the approach adopted by the British Standards Institution for the BS6333 classification. Its procedure uses a hexagonal drive of known hardness and establishes a proof load torque which each tool must achieve to gain approval. For 300mm adjustable wrenches it's 515Nm and so we adopted this as our first test requirement.
In our case we used 19mm (3/4 in) square drives to allow easy connection to Norbar's test rig and to provide a new and undamaged piece for each tool. Each wrench was adjusted to fit the square drive and its handle located against the machine's reaction bar. With the wrench in place a motor slowly rotated the square drive to increase the torque level progressively to a predetermined limit. A digital panel displayed the torque reading in Nm and was set to record the highest level reached should a sudden failure occur. In practice the control system on the test bench motor made it impossible to achieve an exact torque of 515Nm in every case, but we were able to get as close as made no difference.
With each tool held on the bench at the 515Nm proof load, we measured the jaw width at the widest point to determine what deflection had occurred. Then the torque was released and the tool removed to assess any damage to the jaws or winding mechanism. After this the tool was replaced and torque was reapplied in excess of the BS limit to test the ultimate strength of the tool. In the interest of safety we set a limit of 800Nm at this top end.
With tools that reached 800Nm we measured the maximum jaw width at the widest point to determine how much deflection had taken place. Where the readings fell short of 800Nm (see results table) the torque figure represents the maximum which could be transmitted with that tool. The limiting factors were distortion allowing the square to rotate within the jaws, damage to the adjusting worm or body of the wrench. After the test the tools were given a final inspection.
CONCLUSIONS
On purely practical grounds there are a number of important conclusions which can be drawn from our experiments. First there are the basics such as instructional literature. Although you may think that using an adjustable wrench is as easy as jumping down from a cab, a little good advice never does any harm.
However. only Britool, CK and Draper provided any such information on the packaging. Snap-On went one better with `no hammering', no extensions' messages and an arrow indicating the correct direction of use cast into the handle. (Britool makes the claim that its wrench can be used in either direction.) The quality of finish did vary to some degree across the group with those tools from Britool, King Dick, Draper and Hilka suffering a little bit from sharp edges and corners. We also noticed that the worm gear wheels on the Britool and Beta wrenches had sharp edges at the ends of their adjusting worms.
The odd one out, in terms of adjustment control, was the wrench from MTD with its knurled screw located beyond the moving jaw Although the mechanism worked smoothly enough, we found it very hard to close the jaws one-handed—as you normally have to in the workshop situation, The other design feature which stood out, for the wrong reasons, was the handle on the King Dick. We found that the thin edges made this tool rather uncomfortable to use in comparison to the other more conventionally styled examples.
For performance, the Snap-On and MTD (Irimo) were impressive, but both cost considerably more than the others. The MTD actually showed slightly less jaw deflection than the Snap-On, although its jaws were more damaged afterwards. The only other wrenches to reach our torque test limit of 800Nm were those from CK and Hiika. Both showed very low levels of jaw deflection at the 515Nm proof load although the Mika inched ahead with its performance at 800Nm. At the bottom of the scale the wrenches from Stahlwille, Hazet and Britool were all unable to better 600Nm. These wrenches, which share a very similar appearance, produced remarkably consistent results considering the price differences between them.
There were only a couple of actual breakages. The more serious of the two was with the Facom wrench which cracked across one side of the head between the adjustable jaw track and one corner of the worm gear aperture. The King Dick wrench gave way because the thread on the worm gear sheered off. While this was quite a serious problem it didn't actually ruin the tool because a replacement gear could be fitted.
In most cases the final choice about purchase comes down to a combination of price, perceived value, brand loyalty and availability. The bargain of the bunch has to be the Hilka. At just £7.50 it's less than a quarter the price of the Snap-On and yet it performs very nearly as well as the American champ.
But it is a case of you pay your money and take your choice. It's your money and your decision, but we hope it is at least an informed choice.