OPERATION REFRIGERATION
Page 64
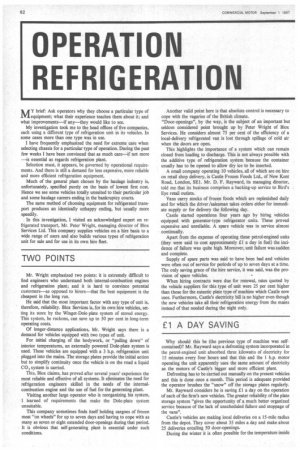
Page 66
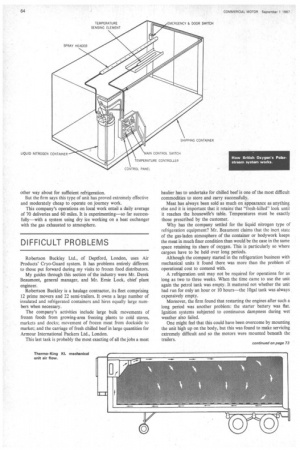
Page 75
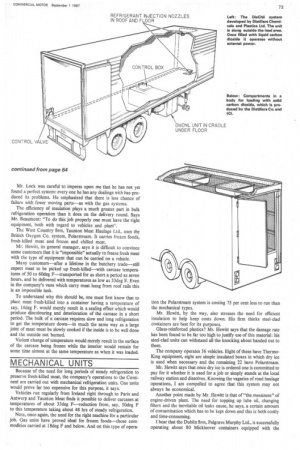
Page 76
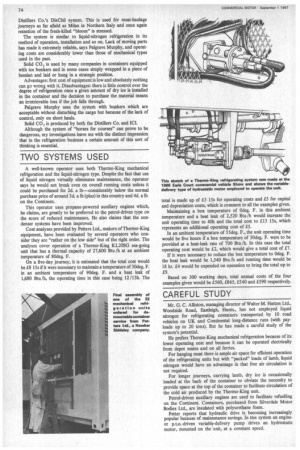
If you've noticed an error in this article please click here to report it so we can fix it.
mY brief: Ask operators why they choose a particular type of equipment; what their experience teaches them about it; and what improvements—if any—they would like to see.
My investigation took me to the head offices of five companies, each using a different type of refrigeration unit in its vehicles. In some cases more than one type was in use.
I have frequently emphasized the need for extreme care when selecting chassis for a particular type of operation. During the past few weeks I have been convinced that as much care—if not more —is essential as regards refrigeration plant.
Selection must, it appears, be governed by operational requirements. And there is still a demand for less expensive, more reliable and more efficient refrigeration equipment.
Much of the general plant chosen by the haulage industry is, unfortunately, specified purely on the basis of lowest first cost. Hence we see some vehicles totally unsuited to their particular job and some haulage careers ending in the bankruptcy courts.
The same method of choosing equipment for refrigerated transport produces an identically unhappy ending, but usually more speedily.
In this investigation, I visited an acknowledged expert on refrigerated transport, Mr. Peter Wright, managing director of Blox Services Ltd. This company supplies vehicles on a hire basis to a wide range of users and also builds various types of refrigeration unit for sale and for use in its own hire fleet.
TWO POINTS
Mr. Wright emphasized two points: it is extremely difficult to find engineers who understand both internal-combustion engines and refrigeration plant; and it is hard to convince potential customers—as opposed to hirers—that the best equipment is the cheapest in the long run.
He said that the most important factor with any type of unit is, therefore, reliability. Blox Services is, for its own hire vehicles, setting its store by the Winget-Dole-plate system of stored energy. This system, he reckons, can save up to 50 per cent in long-term operating costs.
Of longer-distance applications, Mr. Wright says there is a demand for vehicles equipped with two types of unit.
For initial charging of the bodywork, or "pulling down" of interior temperatures, an externally powered Dole-plate system is used. These vehicles are equipped with a 3 h.p. refrigeration unit plugged into the mains. The storage plates provide the initial action but to simplify continuity once the vehicle is on the road a liquid CO, system is carried.
This, Blox claims, has proved after several years' experience the most reliable and effective of all systems. It eliminates the need for refrigeration engineers skilled in the needs of the internalcombustion engine and the use of fuel for the generating plant.
Visiting another large operator who is reorganizing his system, I learned of requirements that make the Dole-plate system unsuitable.
This company sometimes finds itself holding cargoes of frozen meat "on wheels" for up to seven days and having to cope with as many as seven or eight extended door-openings during that period. It is obvious that self-generating plant is essential under such conditions. Another valid point here is that absolute control is necessary to cope with the vagaries of the British climate.
"Door-openings", by the way, is the subject of an important but seldom considered point brought up by Peter Wright of Blox Services. He considers almost 75 per cent of the efficiency of a local-delivery refrigerated van is lost through spillage of cold air when the doors are open.
This highlights the importance of a system which can remain closed from loading to discharge. This is not always possible with the additive type of refrigeration system because the container usually has to be opened to allow dry ice to be inserted.
A small company operating 10 vehicles, all of which are on hire on retail shop delivery, is Castle Frozen Foods Ltd., of New Kent Road, London, SEl. Mr. D. F. Rayward, its managing director, told roe that its business comprises a backing-up service to Bird's Eye retail outlets.
Vans carry stocks of frozen foods which are replenished daily and for which the driver/salesman takes orders either for immediate supply or for delivery the following day.
Castle started operations four years ago by hiring vehicles equipped with generator-type refrigerator units. These proved expensive and unreliable. A spare vehicle was in service almost continually.
Apart from the expense of operating these petrol-engined units (they were said to cost approximately £1 a day in fuel) the incidence of failure was quite high. Moreover, unit failure was sudden and complete.
Supply of spare parts was said to have been bad and vehicles were often out of service for periods of up to seven days at a time. The only saving grace of the hire service, it was said, was the provision of spare vehicles.
When hiring contracts were due for renewal, rates quoted by the vehicle suppliers for this type of unit were 25 per cent higher than those for the eutectic plate type of machine which Castle now uses. Furthermore, Castle's electricity bill is no higher even though the new vehicles take all their refrigeration energy from the mains instead of that needed during the night only.
£1 A DAY SAVING
Why should this be (the previous type of machine was selfcontained)? Mr. Rayward says a defrosting system incorporated in the petrol-engined unit absorbed three kilowatts of electricity for 15 minutes every four hours and that this and the 1 h.p. motor operating the unit apparently uses the same amount of electricity as the motors of Castle's bigger and more efficient plant.
Defrosting has to be carried out manually on the present vehicles and this is done once a month. This period is adequate provided the operator brushes the "snow" off the storage plates regularly.
Mr. Rayward considers he is saving £1 a day on the operation of each of the firm's new vehicles. The greater reliability of the plate storage system "gives the opportunity of a much better organized service because of the lack of unscheduled failure and stoppage of the vans".
Castle's vehicles are making local deliveries on a 15-mile radius from the depot. They cover about 35 miles a day and make about 25 deliveries entailing 50 door-openings.
During the winter it is often possible for the temperature inside other way about for sufficient refrigeration.
But the firm says this type of unit has proved extremely effective and moderately cheap to operate on journey work.
This company's operations on local work entail a daily average of 70 deliveries and 60 miles. It is experimenting—so far successfully—with a system using dry ice working on a heat exchanger with the gas exhausted to atmosphere.
DIFFICULT PROBLEMS
Robertson Buckley Ltd., of Deptford, London, uses Air Products' Cryo-Guard system. It has problems entirely different to those put forward during my visits to frozen food distributors.
My guides through this section of the industry were Mr. Derek Beaumont, general manager, and Mr. Ernie Lock, chief plant engineer.
Robertson Buckley is a haulage contractor, its fleet comprising 12 prime movers and 22 semi-trailers. It owns a large number of insulated and refrigerated containers and hires equally large numbers when necessary.
The company's activities include large bulk movements of frozen foods from growing-area freezing plants to cold stores, markets and docks; movement of frozen meat from dockside to market; and the carriage of fresh chilled beef in large quantities for Armour International Packers Ltd., London.
This last task is probably the most exacting of all the jobs a meat haulier has to undertake for chilled beef is one of the most difficult commodities to store and carry successfully.
Meat has always been sold as much on appearance as anything else and it is important that it retains that "fresh-killed" look until it reaches the housewife's table. Temperatures must be exactly those prescribed by the customer.
Why has the company settled for the liquid nitrogen type of refrigeration equipment? Mr. Beaumont claims that the inert state of the gas-laden atmosphere of the container or bodywork keeps the meat in much finer condition than would be the case in the same space retaining its share of oxygen. This is particularly so where cargoes have to be held over long periods.
Although the company started in the refrigeration business with mechanical units it found there was more than the problem of operational cost to contend with.
A refrigeration, unit may not be required for operations for as long as two to three weeks. When the time came to use the unit again the petrol tank was empty. It mattered not whether the unit had run for only an hour or 10 hours—the lOgal tank was always expensively empty.
Moreover, the firm found that restarting the engines after such a long period was another problem: the starter battery was flat. Ignition systems subjected to continuous dampness during wet weather also failed.
One might feel that this could have been overcome by mounting the unit high up on the body, but this was found to make servicing extremely difficult and so the motors were mounted beneath the trailers. Mr. Lock was careful to impress upon me that he has not yet found a perfect system: every one he has any dealings with has produced its problems. He emphasized that there is less chance of failure with fewer moving parts—as with the gas systems.
The efficiency of insulation plays a much greater part in bulk refrigeration operation than it does on the delivery round. Says Mr. Beaumont: "To do this job properly one must have the right equipment, both with regard to vehicles and plant".
The West Country firm, Taunton Meat Haulage Ltd., uses the British Oxygen Co. system, Polarstream. It carries frozen foods, fresh-killed meat and frozen and chilled meat.
Mr. Hewitt, its general manager, says it is difficult to convince some customers that it is "impossible" actually to freeze fresh meat with the type of equipment that can be carried on a vehicle.
Many customers—after a lifetime in the butchery trade—still expect meat to be picked up fresh-killed—with carcase temperatures of 50 to 60deg F—transported for as short a period as seven hours, and be delivered with temperatures as low as 33deg F. Even in the company's vans which carry meat hung from roof rails this is an impossible task.
To understand why this should be, one must first know that to place meat fresh-killed into a container having a temperature of say, 14deg F. would merely result in a sealing effect which would produce discolouring and deterioration of the carcase in a short period. The bulk of a carcase requires slow and long refrigeration to get the temperature down—in much the same way as a large joint of meat must be slowly cooked if the inside is to be well done and the outside not burned.
Violent change of temperature would merely result in the surface of the carcase being frozen while the interior would remain for some time almost at the same temperature as when it was loaded.
MECHANICAL UNITS
Because of the need for long periods of steady refrigeration to preserve fresh-killed meat, the company's operations to the Continent are carried out with mechanical refrigeration units. Gas units would prove far too expensive for this purpose, it says.
Vehicles run regularly from Ireland right through to Paris and Antwerp and Taunton Meat finds it possible to deliver carcases at temperatures of about 33deg F—reduction from, say, 50deg F to this temperature taking about 48 hrs of steady refrigeration.
Note, once again, the need for the right machine for a particular job. Gas units have proved ideal for frozen foods—those commodities carried at 18deg F and below. And on this type of opera
tion the Polarstream system is costing 75 per cent less to run than the mechanical types.
Mr. Hewitt, by the way, also stresses the need for efficient insulation to help keep costs down. His firm thinks steel-clad containers are best for its purposes.
Glass-reinforced plastics? Mr. Hewitt says that the damage rate has been found to be far too high to justify use of this material: his steel-clad units can withstand all the knocking about handed out to them.
The company operates 36 vehicles. Eight of these have ThermoKing equipment, eight are simple insulated boxes in which dry ice is used when necessary and the remaining 22 have Polarstream.
Mr. Hewitt says that once dry ice is ordered one is committed to pay for it whether it is used for a job or simply stands at the local railway station and dissolves. Knowing the vagaries of road haulage operations, I am compelled to agree that this system may not always be economical.
Another point made by Mr. Hewitt is that of "the messiness" of engine-driven plant. The need for topping up lube oil, changing filters and the inevitable oil leaks cause, he says, a certain amount of contamination which has to be kept down and this is both costly and time-consuming.
I hear that the Dublin firm, Palgrave Murphy Ltd., is successfully operating about 80 Mickleover containers equipped with the
Distillers Co.'s DisChil system. This is used for meat-haulage journeys as far afield as Milan in Northern Italy and once again retention of the fresh-killed "bloom" is stressed.
The system is similar to liquid-nitrogen refrigeration in its method of operation, installation and so on. Lack of moving parts has made it extremely reliable, says Palgrave Murphy, and operating costs are considerably lower than those of mechanical types used in the past.
Solid CO, is used by many companies in containers equipped with ice bunkers and in some cases simply wrapped in a piece of hessian and laid or hung in a strategic position.
Advantages: first cost of equipment is low and absolutely nothing can go wrong with it. Disadvantages: there is little control over the degree of refrigeration once a given amount of dry ice is installed in the container and the decision to purchase the material means an irretrievable loss if the job falls through.
Palgrave Murphy uses the system with bunkers which are acceptable without disturbing the cargo but because of the lack of control, only on short hauls.
Solid CO, is produced by both the Distillers Co. and ICI.
Although the system of "horses for courses" can prove to be dangerous, my investigations leave me with the distinct impression that in the refrigeration business a certain amount of this sort of thinking is essential.
TWO SYSTEMS USED
A well-known operator uses both Thermo-King mechanical refrigeration and the liquid-nitrogen type. Despite the fact that use of liquid nitrogen virtually eliminates maintenance, the operator says he would not break even on overall running costs unless it
could be purchased for 2d. a lb considerably below the normal purchase price of around 3d. a lb (plus) in this country and 4d. a lb on the Continent.
This operator uses propane-powered auxiliary engines which, he claims, are greatly to be preferred to the petrol-driven type on the score of reduced maintenance. He also claims that the condenser systems have been improved.
Cost analyses provided by Petters Ltd., makers of Thermo-King equipment, have been evaluated by several operators who consider they are "rather on the low side" but of the right order. The analyses cover operation of a Thermo-King KL2OSG sea-going unit that has a thermal capacity of 27,600 Btu /h at an ambient temperature of 80deg. F.
On a five-day journey, it is estimated that the total cost would be £8 15s if it were necessary to maintain a temperature of 30deg. F. in an ambient temperature of 90deg. F. and a heat leak of 1,680 Btu /h, the operating time in this case being 12/13h. The
total is made up of £3 15s for operating costs and £5 for capital and depreciation costs, which is common to all the examples given.
Maintaining a box temperature of Odeg. F. in this ambient temperature and a heat leak of 2,520 Btu /h would increase the unit operating time to 40h and the total cost to £13 15s, which represents an additional operating cost of £5.
In an ambient temperature of 55deg. F., the unit operating time would be five hours if a box temperature of 30deg. F. were to be provided at a heat-leak rate of 700 Btu /h. In this case the total operating cost would be £2, which would give a total cost of £7.
If it were necessary to reduce the box temperature to Odeg. F. the heat leak would be 1,540 Btu /h and running time would be 18 hr. £4 would be expended on operation to bring the total up to £9.
Based on 300 working days, total annual costs of the four examples given would be £560, £865, £540 and £590 respectively.
CAREFUL STUDY
Mr. G. C. Alliston, managing director of Walter M. Hatton Ltd., Woodside Road, Eastleigh, Hants., has not employed liquid nitrogen for refrigerating containers transported by 10 road vehicles on UK and Continental long-distance runs (with payloads up to 20 tons). But he has made a careful study of the system's potential.
He prefers Thermo-King mechanical refrigeration because of its lower operating cost and because it can be operated electrically from depot mains and on all ferries.
For hanging meat there is ample air space for efficient operation of the refrigerating units but with "packed" loads of lamb, liquid nitrogen would have an advantage in that free air circulation is not required.
For longer journeys, carrying lamb, dry ice is occasionally loaded at the back of the container to obviate the necessity to provide space at the top of the container to facilitate circulation of the cold air produced by the Thermo-King unit.
Petrol-driven auxiliary engines are used to facilitate refuelling on the Continent. Containers, purchased from Silverdale Motor Bodies Ltd., are insulated with polyurethane foam.
Petter reports that hydraulic drive is becoming increasingly popular because of maintenance savings. In this system an engineor p.t.o.-driven variable-delivery pump drives an hydrostatic motor, mounted on the unit, at a constant speed.