The Mechanism of Lubrication
Page 32
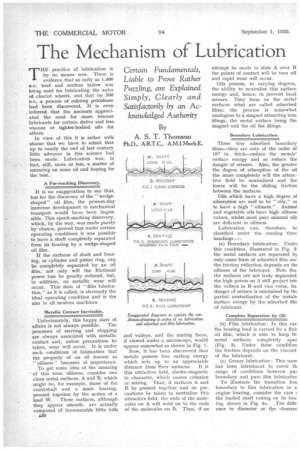
Page 33
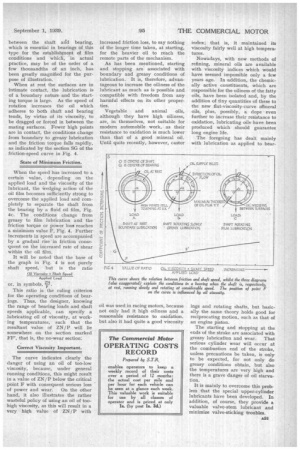
If you've noticed an error in this article please click here to report it so we can fix it.
Certain Fundamentals, Liable to Prove Rather Puzzling, are Explained Simply, Clearly and Satisfactorily by an Ac.
knowledged Authority
By
A. S. T. Thomson
PhD., A.R.T.C.,
THE practice of lubrication is by no means new. There is evidence that as early as 1,400 B.c. beef and mutton tallow was being used for lubricating the axles of, chariot wheels, and that by 500 B.C. a process of refining petroleum had been discovered. It is even . inferred that the ancients appreciated the need for more viscous lubricants for certain duties and less viscous or lighter-bodied oils for others.
In view of this it is rather with shame that we have to admit that up to nearly the end of last century little advance in this science had been made. Lubrication was, in fact, still, more or less, a matter of smearing on some oil and hoping for the best.
A Far-reaching Discovery.
It is no exaggeration to say that, but for the discovery of the " wedgeshaped" oil film, the present-day immense development in mechanical transport would have been impossible. This epoch-marking discovery, which, by the way, was made purely by chance, proved that under certain operating conditions it was possible to have a shaft completely separated from its bearing by a wedge-shaped oil film.
If the surfaces of shaft and bearing, or cylinder and piston ring, cat„t be completely separated by an oil film, not only will the frictional power loss be greatly reduced, but, in addition, no metallic wear will occur. This state of "film lubrication," as it is called, is obviously the ideal operating condition and is the aim in all modern machines.
Metallic Contact Inevitable.
Unfortunately, this happy state of affairs is not always possible. The processes of starting and stopping are always associated with metallic contact and, unless precautions be taken, wear will occur. It is under such conditions of lubrication that the property of an oil known as " oiliness" becomes of importance. To get some idea of the meaning • of this term oiliness, consider two clean metal surfaces, A and B, which might be, for example, those of the crankshaft and a main bearing, pressed together by the action of a load W. These surfaces, although they appear smooth, are actually composed of innumerable little hills £30
and valleys, and the mating faces, if viewed under a microscope, would appear somewhat as shown in Fig. I. Now, it has been discovered that metals possess free surface energy which acts up to an appreciable distance from their surfaces. It is this attractive field, electro-magnetic in character, which causes cohesion or seizing. Thus, if surfaces A and B be pressed together and no precautions be taken to neutralize this attractive field, the ends of the molecules on A will weld on to the ends
of the molecules on B. Thus, if an
attempt be made to slide A over B the points of contact will be torn off and rapid wear will occur.
Oils possess, in varying degrees, the ability to neutralize this surface energy and, hence, to prevent local seizure. They form on the metal surfaces what are called adsorbed films; the process is somewhat analogous to a magnet attracting iron filings, the metal surface being the magnet and the oil the filings.
Boundary Lubrication.
These tiny adsorbed boundary films—they are only of the order of 10-7 in. thick—reduce the metals' surface energy and so reduce the danger of seizure. Also, the greater the degree of adsorption of the oil the more completely will the attractive field be neutralized and the lower will be the sliding friction between the surfaces.
Oils which have a high degree of adsorption are said to be "Oily," cps to have a high "oiliness." Animal and vegetable oils have high oiliness values, whilst most pure mineral oils are deficient in oiliness.
Lubrication can, therefore, lac classified under the ensuing thre( headings :— (a) Boundary lubrication : Undei this condition, illustrated in Fig. 2 the metal surfaces are separated b3 only some form of adsorbed film anc the friction reduction depends on thi oiliness of the lubricant. Note tha. the surfaces are not truly separated the high points on A still project int( the valleys in B and vice versa, bu danger of seizure is minimized by thn partial neutralization of the metals surface energy by the adsorbed fin of lubricant.
Complete Separation by Oil.
• (b) Film lubrication : In this cas. the bearing load is carried by a fluh oil film, which is able to keep th metal surfaces completely apar (Fig. 3). Under these condition the friction depends on the viscosit of the lubricant.
(c) Greasy lubrication : This nam has been introduced to cover th range of conditions between put boundary and pure film lubricatior
To illustrate the transition fro' boundary to film lubrication in a engine bearing, consider the case ( the loaded shaft resting on its boa: ing, shown in Fig. 4A. The diffe: ence in diameter or the clearam
between the shaft arid bearing, which is essential in bearings of this type for the establishment of film conditions and which, in actual practice, may be of the order of a few thousandths of an inch, has been greatly magnified for the purpose of illustration.
When at rest the surfaces are in intimate contact, the lubrication is of a boundary nature and the starting torque is large. As the speed of rotation increases the oil which adheres to both shaft and bearing tends, by virtue of its viscosity, to be dragged or forced in between the mating surfaces. Fewer high points are in contact, the conditions change from boundary to greasy lubrication and the friction torque falls rapidly, as indicated by the section SG of the friction-speed curve in Fig. 4.
State of Minimum Friction.
When the speed has increased to a certain value, depending on the applied load and the viscosity of the lubricant, the Wedging action of the oil film becomes sufficiently strong to overcome the applied load and completely to separate the shaft from the bearing by a fluid oil film, Fig. 4c. The conditions change from greasy to film lubrication and the friction torque or power loss reaches a minimum value F, Fig.. 4. Further increments in speed are accompanied by a gradual rise in friction consequent on the increased rate of shear within the oil film.
It will be noted that the base of the graph in Fig. 4 is not purely shaft speed, but is the ratio
. oil Viscosity x Shaft Speed
Applied Load
or, in symbols, V.
This ratio is the ruling criterion for the operating conditions of bearings. Thus, the designer, knowing the range of bearing loads and shaft speeds applicable, can specify a lubricating oil of viscosity, at working temperatures, such that the resultant value of ZN/P will lie somewhere on the section marked FF', that is, the no-wear section'.
Correct Viscosity Important.
The curve indicates clearly the danger of using an oil of too-low viscosity, because, under general running conditions, this might result in a value of ZN/P below the critical point F with consequent serious loss of power and wear. On the other hand, it also illustrates the rather wasteful policy of using an oil of toohigh viscosity, as this will result in a very high value of ZN/P with increased friction loss, to say nothing of the longer time taken, at starting, for the heavier oil to reach the remote parts of the mechanism.
As has been mentioned, starting and stopping are associated with boundary and greasy conditions of lubrication. It is, therefore, advantageous to increase the oiliness of the lubricant as much as is possible and compatible with freedom from any harmful effects on its other properties.
Vegetable and animal oils, although they have high oiliness, are, in themselves, not suitable for modern automobile work, as their resistance to oxidation is much lower than that of a good mineral oil. Until quite recently, however, castor
oil was used in racing motors, because not only had it high oiliness and a reasonable resistance to oxidation, but also it had quite a good viscosity
index; that is, it maintained its viscosity fairly well at high temperatures.
Nowadays, with new methods of refining, mineral oils are available with viscosity indices which Would have seemed impossible only a few years ago. In addition, the chemically active constituents, which are responsible for the oiliness of the fatty oils, have been isolated and, by the addition of tiny quantities of these to the new flat-viscosity-curve nlineral oils, plus, possibly, a dope even further to increase their resistance to oxidation, lubricating oils have been produced which should guarantee long engine life.
The foregoing has dealt mainly with lubrication as applied to bear
ings and rotating shafts, but basically the same theory holds good for reciprocating motion, such as that of an engine piston.
The starting and stopping at the ends of the stroke are associated with greasy lubrication and wear. That serious cylinder wear will occur at the combustion end of the stroke, unless precautions be taken, is only to be expected, for not only do greasy conditions obtain, but also the temperatures are very high and there is a grave danger of oil starvation.
It is mainly to overcome this problem that the special upper-cylinder lubricants have been developed. In addition, of course, they provide a valuable valve-stem lubricant and minimize valve-sticking troubles.