HINTS ON MAINTENANCE.
Page 26
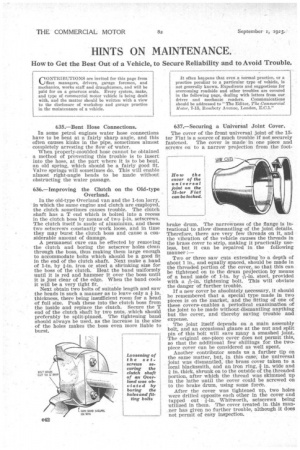
If you've noticed an error in this article please click here to report it so we can fix it.
How to Get the Best Out of a Vehicle, to Secure Reliability and to Avoid Trouble.
635.—Bent Hose Connections.
In some petrol engines water hose connections have to be bent at a fairly sharp angle, and this often causes kinks in the pipe, sometimes almost completely arresting the flow of water.
When properly-moulded hose cannot be obtained a method of preventing this trouble is to insert into the hose, at the part where it is to be bent, an old spring, which should be a fairly good tit. Valve springs will sometimes do. This will enable almost right-angle bends to be made without obstructing the water passage.
636.—Improving the Clutch on the Old-type Overland.
In the old-type Overland van and the 1-ton lorry, in which the same engine and clutch are employed, the clutch sometimes causes trouble. The clutch shaft has a T end which is bolted into a recess in the clutch boss by means of two Fin. setscrews. The clutch itself is made of aluminium, and these two setscrews constantly work loose, and in time they may burst the clutch boss and cause a considerable amount of damage.
A permanent cure can be effected by removing the clutch and boring the setscrew holes clean through the boss, thus making them large enough to accommodate bolts which should be a good fit in the end of the clutch shaft. Next make a band of 1-in, by i-in. iron or, steel a shrinking size for the boss of the clutch. Heat the band uniformly until it is red and hammer it over the boss until it is just clear of the edge. When the band cools it will be a very tight fit.
Next obtain two bolts of suitable length and saw the heads in such a manner as to leave only a in. thickness, there being insufficient room for a head of full size. Push these into the clutch boss from the inside and replace the clutch. Secure the T end of the clutch shaft by two nuts, which should preferably be split-pinned. The tightening band should always be used, as the increase in the size of the holes makes the boss even more liable te burst. 637.—Securing a Universal Joint Cover.
The cover of the front universal joint of the 15ter Fiat is a source of much trouble if not securely fastened. The cover is made' in one piece and screws on to a narrow projection from the foot brake drum. The narrowness of the flange is intentional to allow dismantling of the joint details. Therefore, there are very few threads on it, and the vibration of the vehicle causes the threads in the brass cover to strip, making it practically useless, but it can be repaired in the following manner :— Two or three saw cuts extending *to a depth of about 1 in., and equally spaced, should be made in the threaded portion of the cover, so that this can be tightened on to the drum prOjection by means of a band made of 1-in, by steel, provided with a tv-in. tightening bolt. This will obviate the danger of further trouble.
If a new cover be absolutely necessary, it should be remembered that a special type made in two pieces is on the market, and the fitting of one of these coversenables a periodical examination of the joint to be made without dismantling anything but the cover, and thereby saving trouble and expense.
The joint itself depends on a main assembly bolt, and an occasional glance at the nut and split pin of this bolt will save many a smashed joint. The original one-piece cover does not permit this, so that the additional few shillings for the twopiece cover can be considered as well spent.
Another contributor sends us a further tip On the same matter, but, in this case, the universal joint was dismantled, the brass cover taken to a local blacksmith, and an iron ring, in. wide and g in. thick, shrunk on to the outside of the threaded portion, after which the thread was skimmed up in the lathe until the cover could be screwed on to the brake drum, using some force.
After the cover was tightened up, two holes were drilled opposite each other in the cover and tapped out 1-in. Whitworth, setscrews being utilized in them. The cover, treated in this manner has given no further trouble, although it does not permit of easy inspection.