Pioneering test tactics
Page 27
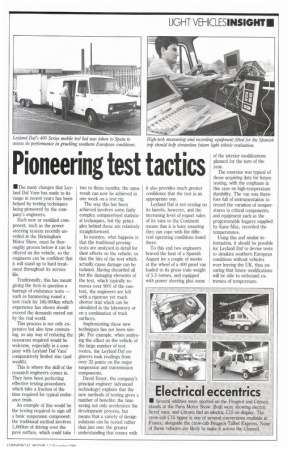
If you've noticed an error in this article please click here to report it so we can fix it.
MThe many changes that Leyland Daf Vans has made to its range in recent years has been helped by testing techniques being pioneered by the company's engineers.
Each new or modified component, such as the power steering system recently unveiled at the Birmingham Motor Show, must be thoroughly proven before it can be offered on the vehicle, so the engineers can be confident that it will stand up to hard treatment throughout its service life.
Traditionally, this has meant giving the item in question a barrage of endurance tests — such as hammering round a test track for 160,000km which experience has shown should exceed the demands meted out by the real world.
This process is not only expensive but also time consuming, so any way of reducing the resources required would be welcome, especially in a company with Leyland Daf Vans' comparatively limited size (and wealth).
This is where the skill of the research engineers comes in. They have been perfecting effective testing procedures which take a fraction of the time required for typical endurance trials.
An example of this would be the testing required to sign off a basic suspension component: the traditional method involves 1,600km of driving over the pave surface, which could take two to three months; the same result can now be achieved in one week on a test rig.
The way this has been achieved involves some fairly complex computerised statistical techniques, but the principles behind these are relatively straightforward.
In essence, what happens is that the traditional proving tests are analysed in detail for their effects on the vehicle, so that the bits of the test which actually cause damage can be isolated. Having discarded all but the damaging elements of the test, which typically removes over 90% of the content, the engineers are left with a rigorous yet much shorter trial which can be simulated in the laboratory or on a combination of track surfaces.
Implementing these new techniques has not been simple. For example, when analysing the effect on the vehicle of the large number of test routes, the Leyland Daf engineers took readings from over 32 points on the major suspension and transmission components.
David Ensor, the company's principal engineer (advanced technology) explains that the new methods of testing gives a number of benefits: the time saving not only accelerates the development process, but means that a variety of design solutions can be tested rather than just one; the greater understanding that comes with it also provides much greater confidence that the test is an appropriate one.
Leyland Daf is not resting on its laurels, however, and the increasing level of export sales of its vans to the Continent means that it is busy ensuring they can cope with the different operating conditions found there.
To this end two engineers braved the heat of a Spanish August for a couple of weeks at the wheel of a 400 panel van loaded to its gross train weight of 5.5 tonnes, and equipped with power steering plus some of the interior modifications planned for the turn of the year.
The exercise was typical of those acquiring data for future testing, with the emphasis in this case on high-temperature durability. The van was therefore full of instrumentation to record the variation of temperatures in critical components, and equipment such as the programmable loggers supplied by Kane-May, recorded the temperatures.
Using this and similar information, it should be possible for Leyland Daf to devise tests to simulate southern European conditions without vehicles ever leaving the UK, thus ensuring that future modifications will be able to withstand extremes of temperature.