Container filling and emptying ICI's experience
Page 49
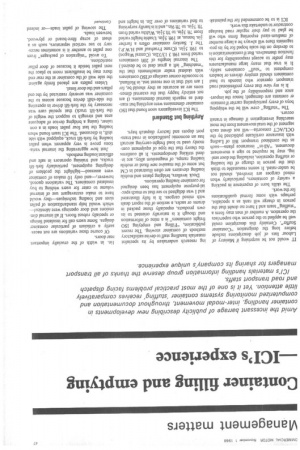
If you've noticed an error in this article please click here to report it so we can fix it.
Amid the incessant barrage of publicity describing new developments in container handling, inter-modal movement, throughout documentation and computerized monitoring systems container 'stuffing' receives comparatively little attention. Yet it is one of the most practical problems facing dispatch and road transport staffs.
ICI's materials handling information group deserve the thanks of all transport managers for sharing its company's unique experience.
IT would not be surprising if Ministry of Labour lists of job descriptions include before long the designation "Container Stuffer". Certainly this description could well be applied to the person who supervises the operation. A number of men may form a "stuffing" team and I have no doubt that the person in charge will rank as a specialist, perhaps with some formal qualifications for the work.
The skills born of experience in packing a variety of containers, particularly when mixed cargoes are involved, should not be under-rated. It seems reasonable to think that the person in charge of the loading or stuffing operation, including the door sealing, may be required to sign a movement document. "All-in" insurance plans—such as the combined transport Bill of Lading with insurance certificate publicized by the OCL/ACT consortia—will not divest each segment of the total movement from the most searching investigation if damage in transit occurs.
The "stuffing" crew will be the whipping boys of every participating carrier if container contents are damaged; hence the importance and responsibility of the job.
It is my view that every professional road transport operator who intends to haul containers should employ drivers or loaders competent to "stuff" containers safely. It is true that many large manufacturers may prefer to accept responsibility for this function themselves. But if containerization is to develop on the scale hoped for by its protagonists there will always be a large number of medium-sized exporting firms who will be glad to pay their regular road haulage contractor to undertake this work.
ICI is to be commended for the painstak
ing research undertaken by its specialist materials handling staff to devise satisfactory methods of container stowing. The recent publication, "Filling and emptying ISO freight containers" is a mine of information and though it is naturally oriented to its own products, especially those packed in drums or sacks, a section of the report deals with mixed cargoes. It is fully illustrated and I was delighted to see that so much special-purpose equipment has been designed for container-loading operations.
Dock levellers, bridging plates and mobile loading elevators are often illustrated in CM but some of the massive new fixed or mobile loading ramps, of magnesium alloy, are indeed striking developments. It all confirms the theory that the type of equipment commonly used to load freight-carrying aircraft has an economic justification in road transport depots and factory dispatch bays.
Anything but Standard
The ICI investigators soon found that ISO container dimensions were anything but standard as regards internal demensions. (I am not entirely happy that the external dimensions are as accurate as they should be, for I am told that in one recent test, in Holland, to reconcile corner castings of ISO containers with skeletal trailer attachments that the "matching" left a great deal to be desired.) The internal lengths of 20ft containers varied from 19ft 3 13/32in. (Central Wagon) to 19ft 5-in. (Crane Fruehauf and H.W.P.) The J. Sankey container offers a further lin. bonus, at 19ft 5iin. Usable height varied from 7ft 3-fin. to 7ft 5+in. Widths varied from 7ft 7+in. to 7ft 9in., and it is hardly surprising to find variations of over 2in. in height and 1 in. in width of the crucially important rear doors.
Of course these variations are not neces sarily a criticism of particular container designs. Some users call for insulated linings or specially robust floors. If all internal dimensions and door openings were identical— which would help standardization of pallet sizes and loading techniques—they would have to make extravagant use of internal volume to cater for users wishing to buy insulated containers. The variations quoted, however,—and only 10 makes of container were assessed—highlight the problem of designing equipment, particularly fork-lift trucks, and training operators in safe and efficient loading methods.
Just how aggravating the internal variations prove is very apparent when pallet loading by fork-lift truck, equipped with side shift, is discussed. The ICI team found when loading the last four pallet loads in a con tamer, (using a bridging device of adequate area and strength to support the weight or the fork-lift truck) that special care was necessary by the fork-lift driver in operating the side-shift device because access to the container was severely restricted by the end pillars and the door lintel.
Unless pallets are placed firmly against the side wall of the container at the rear end there may be insufficient room to place the next pallet beside it because of door pillar restrictions.
To avoid "migration of packages" from one pallet to another it is sometimes necessary to use vertical separators, such as a sheet of scrap fibre-board or plywood. between loads.
The stowing of pallet loads—or indeed
Continued