Lessons from Industrial Dual-fuel Engines
Page 28
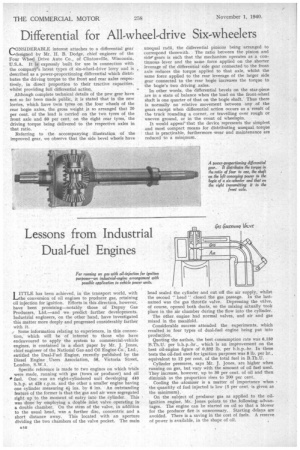
If you've noticed an error in this article please click here to report it so we can fix it.
La 1 ITTLE has been achieved, in the transport world, with the conversion of oil engines to producer gas, retaining oil injection for ignition. Efforts in this .directed, however, have been promising—notably those of Dupuy Gas Producers, Ltd.—and we predict further developments. Industrial engineers, on the other hand, have investigated this matter more deeply and progressed considerably farther with it. .
, Some information relating to experiences, in this connection, which will be of interest to those who have endeavoured to apply the system to commercial-vehicle engines, is contained in a short paper by Mr. J. Jones, chief engineer of the National Gas and Oil Engine Co., Ltd., entitled the Dual-Fuel Engine, recently published by the Diesel Engine Users Association, 56, Victoria Street, London, S.W.1.
Specific reference is made to two engines on which trials were made, running with gas (town or producer) and oil
• fuel. One was an eight-cylindered unit developing 440 b.h.p. at 428 r.p.m. and the other a smaller engine having one cylinder measuring 4+ ins. by 6 ins. An outstanding feature of the former is that the gas and air were segregated right up to the moment of entry into the cylinder. This was done by employing a double inlet valve operating in a double chamber. On the stem of the valve, in addition to the usual head, was a further disc, concentric and a short distance away. This located with an aperture dividing the two chambers of the valve pocket. The main
head sealed the cylinder and cut off the air supply, whilst the second " head " closed the gas passage. In the lastnamed was the gas throttle valve. Depressing the valve, of course, opened both ducts, so the mixing actually took place in the air chamber during the flow into the cylinder.
The other, engine had normal valves, and air and gas mixed in the manifold.
Considerable success attended the experiments, which resulted in four types of dual-fuel engine being put into production.
Quoting the author., the best consumption rate was 6,150 B.Th.U. per b.h.p.-hr., which is an improvement on the best oil-engine figure of 0.832 lb. per b.h.p.-hr. In these tests the oil-fuel used for ignition purposes was 8 lb. per hr„ equivalent to 12 per cent, of the total fuel in B.Th.U.
Cylinder pressures, says Mr. J. Rules, are higher when running on gas, but vary with the amount of oil fuel used. They increase, however, up to 30 per cent, of oil and then diminish as the proportion rises to 100 per cent.
Cooling the atomiser is a matter of importance when the quantity of fuel injected is low (5 per cent, is given as the minimum). the e subject of producer gas as applied to the oil ignition engine, Mr. Jones points to the following advantages. The engine can be started on oil so that a blower for the producer fire is unnecessary. Starting delays are avoided. There is a saving in the cost of fuels. A reserve of power is available, in the shape of oil.