ROAD AND WORKSHOP by Handyman
Page 68
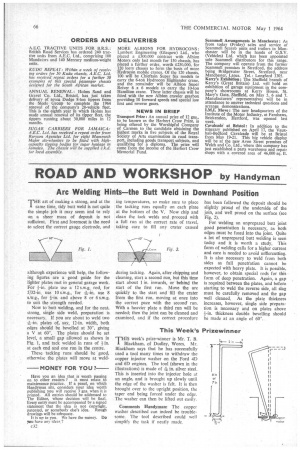
If you've noticed an error in this article please click here to report it so we can fix it.
Arc Welding Hints—the Butt Weld in Downhand Position
THE art of making a strong, and at the same time, tidy butt weld is not quite the simple job it may seem and to rely on a sheer mass of deposit is not sufficient. First and foremost is the need to select the correct gauge electrode, and although experience will help, the following figures are a good guide for the lighter plates met in general garage work. For fin, plate use a 12 s.w.g. rod, for 5/32-in. use 10 s.w.g., for *-in. use 8 s.w.g., for fin, and above 8 or 6 s.w.g. to suit the strength needed.
Now to butt welding, and for the neat, strong, single side weld, preparation is necessary. If you are about to weld two *-in. plates of, say, 12-in, width, both edges should be bevelled at 300, giving a V at 60°. The plates should be set level, a small gap allowed as shown in Fig. 1, and tack welded in runs of in. at each end and one run in the centre.
These tacking runs should be good, otherwise the plates will move at weld
-MONEY FOR YOU?
Have you an idea that is worth passing
on to other readers ? It must relate to maintenance practice. If a panel, on which Handyman sits, considers your idea worth publishing you will receive 3 gns. when it is printed. All entries should be addressed to The Editor, whose decision will be final. Every entry must be accompanied by a signed statement that the idea is not copyright, patented, or somebody else's idea. Rough drawings will be adequate. It is up to you. We have the money. Do you have any ideas ? ing temperatures, so make sure to place the tacking runs equally on each plate at the bottom of the V. Now chip and clean the tack welds and proceed with a full run at the correct rate of travel, taking care to fill any crater caused during tacking. Again, after chipping and cleaning, start a second run, but this time start about 1 in. inwards, or behind the start of the first run. Move the arc quickly to the start and fill the crater from the first run, moving at once into the correct pace with the second run. With a heavier plate a third run will be needed; then the joint can be cleaned and examined, and if the correct procedure has been followed the deposit should be slightly proud of the underside of the join, and well proud on the surface (see Fig, 2).
For welding an unprepared butt joint good penetration is necessary, as both edges must be fused into the joint. Quite a lot of unprepared butt welding is seen today and it is worth a study. This form of welding calls for a higher current and care is needed to avoid untlereutting. It is also necessary to weld from both sides as full penetration cannot be expected with heavy plate. It is possible, however, to obtain special rods for this form of deep penetration. Again, a gap is required between the plates, and before starting to weld the reverse side, all slag must be carefully removed and the gap well cleaned. As the plate thickness increases, however, single side preparation is necessary and on plates above 4-in. thickness double bevelling should be made at an angle of 60°.