SIDE BET
Page 48
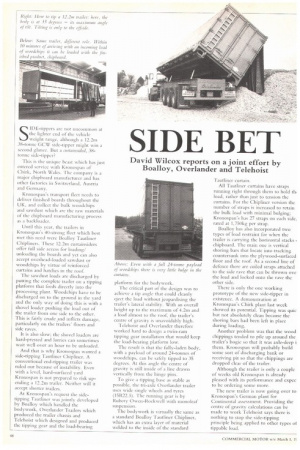
If you've noticed an error in this article please click here to report it so we can fix it.
David Wilcox reports on a joint effort by Boalloy, Overlander and Telehoist
SIDE-tippers are not uncommon at the lighter end of the vehicle weight range, although a 12.2in 38-tonne GCW side-tipper might win a second glance. But a curtainsided, 38tonne side-tipper?
This is the unique beast which has just entered service with K ronospan of Chirk, North Wales. 'Flie company is a major chipboard manufacturer and has other factories in Switzerland, Austria and Germany.
Kronospan's transport fleet needs to deliver finished boards throughout the UK, and collect the bulk woodchips and sawdust which are the raw materials of the chipboard manufacturing process as a backloader.
Until this year, the trailers in Kronospan's 40-strong fleet which best met this need were Boalloy Taudiner Chipliners. These 12.2m curtainsiders offer full side access for loading/ unloading the boards and yet can also accept overhead-loaded sawdust or wood chips by virtue of reinforced curtains and hatches in the roof.
The sawdust loads are discharged by putting the complete trailer on a tipping platform that feeds directly into the processing plant. Woodchips have to be discharged on to the ground in the yard and the only way of doing this is with a shovel loader pushing the load out of the trailer from one side to the other. This is fairly crude and inflicts damage, particularly on the trailers' floors and side raves.
It is also slow; the shovel loaders are hard-pressed and lorries can sometimes wait well over an hour to be unloaded.
And that is why Kronospan wanted a side-tipping Taudiner Chipliner. A conventional end-tipping trailer was ruled out because of instability. Even with a level, hard-surfaced yard Kronospan is not prepared to risk upending a 12.2m trailer. Neither will it accept shorter trailers.
At Kronospan's request the sidetipping Taudiner was jointly developed by Boalloy which handled the bodywork, Overlander Trailers which produced the trailer chassis and Telehoist which designed and produced the tipping gear and the load-hearing platform for the bodywork.
The critical part of the design was to achieve a tip angle that could cleanly eject the load without jeopardising the trailer's lateral stability. With an overall height up to the maximum of 4.2ni and a load almost to the roof, the trailer's centre or gravity is unavoidably high.
Telehoist and Overlander therefore worked hard to design a twin-rain tipping gear installation that would keep the load-bearing platform low.
The result is that the fully-laden body, with a payload of around 24-tonnes of woodchips, can be safely tipped to 35 degrees. At this angle the centre of gravity is still inside of a line drawn vertically from the lunge pins.
To give a tipping base as stable as possible, the tri-axle Overlander trailer uses wide single wheels and tyres (151222.5). The running gear is by Rubery Owen-Rockwell with monoleaf suspension.
The bodywork is virtually the same as a standard Boalloy Tautliner Chipliner, which has an extra layer of material welded to the inside of the standard Tautliner curtain.
All Tautliner curtains have straps running right through theni to hold till load, rather than just to tension the curtains. For the Chipliner version the number of straps is increased to retain the bulk load with minimal bulging; Kronospan's has 27 straps on each side, rated at 1,750kg per strap.
Boalloy has also incorporated two types of load restraint for when the trailer is carrying the horizontal stacks chipboard. The main one is vertical shoring bars that locate into tracking countersunk into the plywood-surfaced floor and the roof. As a second line of defence there are coiled straps attached to the side rave that can be thrown ove the load and locked onto the rave the other side.
There is only the one working prototype of the new side-tipper in existence. A demonstration at Kronospan's Chirk plant last week showed its potential. Tipping was (pie but not absolutely clean because the shoring bars had been left in place during loading.
Another problem was that the wood chippings tended to pile up around the trailer's bogie so that it was axle-deep i them. Kronospan will probably build some sort of discharging bank or receiving pit so that the chippings are dropped clear of the trailer.
Although the trailer is only a couple of weeks old Kronospan is already pleased with its performance and expec. to be ordering some more.
The new trailer is now going over to Kronospan's German plant for Continental assessment. Providing the centre of gravity calculations can be made to work Telehoist says there is nothing to stop the side-tipping principle being applied to other types of tippable load.