LONGER LIFI nd Easie /laintenance
Page 130
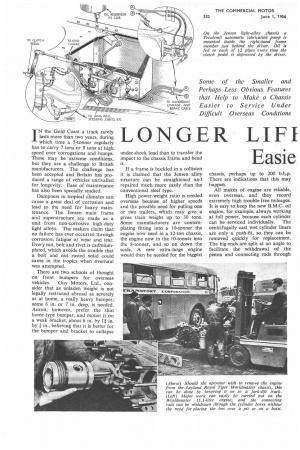
Page 131
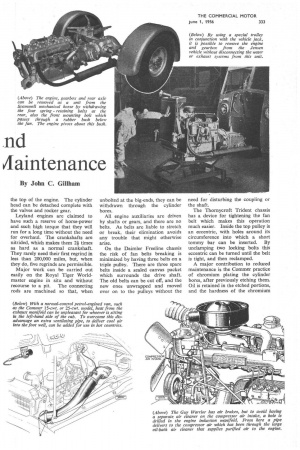
Page 132
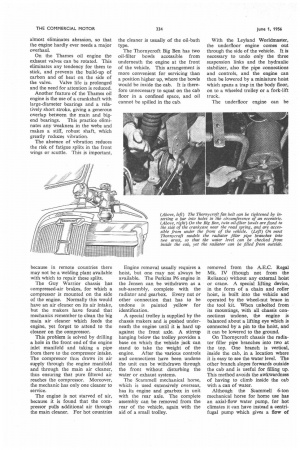
Page 133
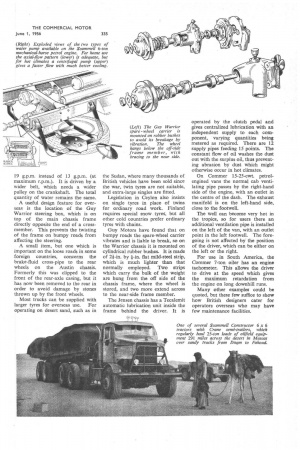
If you've noticed an error in this article please click here to report it so we can fix it.
By John C. Gillham
IN the Gold Coast a truck rarely lasts more than two years, during which time a 5-tonner regularly has to carry 7 tons or 8 tons at high speed over corrugations and bumps. These may be extreme conditions, but they are a challenge to British manufacturers. The challenge has been accepted and Britain has produced a range of vehicles unrivalled for longevity. Ease of maintenance has also been specially studied.
Dampness in tropical climates can cause a great deal of corrosion and lead to the need for heavy maintenance. The Jensen main frame and superstructure are made as a unit from non-corrosive high-duty light alloys. The makers claim that no failure has ever occurred through corrosion, fatigue or wear and tear. Every nut, bolt and rivet is cadmiumplated, which avoids the trouble that a bolt and nut rusted solid could cause in the tropics when overhaul was attempted.
There are two schools of thought on front bumpers for overseas vehicles. Guy Motors, Ltd., consider that as unladen weight is not legally restricted abroad as severely as at home, a really heavy bumper, some 6 in. or 7 in. deep, is needed. Austin, however, prefer the thin home-type bumper, and mount it on a weak bracket, about 6 in. by I f in. by k in., believing that it is better for the bumper and bracket to collapse under shock load than to transfer the impact to the chassis frame and bend it.
If a frame is buckled in a collision it is claimed that the Jensen alloy structure can be straightened and repaired much more easily than the conventional steel type.
High power-weight ratio is needed overseas because of higher speeds and the possible need for pulling one or two trailers, which may give a gross train weight up to 30 tons. Some manufacturers are contemplating fitting into a 10-tonner the engine now used in a 12-ton chassis, the engine now in the 10-tonner into the 8-tonner, and so on down the scale. A new extra-large engine would then be needed for the biggest chassis, perhaps up to 200 b.h.p. There are indications that this may happen.
All makes of engine are reliable, even overseas, and they record extremely high trouble-free mileages. It is easy to keep the new B.M.C. oil engine, for example, always working at full power, because each cylinder can be serviced individually. The centrifugally cast wet cylinder liners are only a push-fit, so they can be removed quickly for replacement. The big-ends are split at an angle to facilitate the withdrawal of the piston and connecting rods through the top of the engine_ The cylinder head can be detached complete with the valves and rocker gear.
Leyland engines are claimed to have such a reserve of horse-power and such high torque that they will run for a long time without the need for overhaul. The crankshafts are nitrided, which makes them 2i times as hard as a normal crankshaft. They rarely need their first regrind in less than 200,000 miles, but, when they do, five regrinds are permissible.
Major work can be carried out easily on the Royal Tiger Worldmaster engine in situ and without recourse to a pit_ The connecting rods are machined so that, when unbolted at the big-ends, they can be withdrawn through the cylinder bores.
All engine auxiliaries are driven by shafts or gears, and there are no belts. As belts are liable to stretch or break, their elimination avoids any trouble that might otherwise arise.
On the Daimler Freeline chassis the risk of fan belts breaking is minimized by having three belts on a triple pulley. There are three spare belts inside a sealed canvas packet which surrounds the drive shaft. The old belts can be cut off, and the new ones unwrapped and moved over on to the pulleys without the need for disturbing the coupling or the shaft.
The Thornycroft Trident chassis has a device for tightening the fan belt which makes this operation much easier. Inside the top pulley is an eccentric, with holes around its circumference into which a short tommy bar can be inserted. By unclamping two locking bolts this eccentric can be turned until the belt is tight, and then reclamped.
A major contribution to reduced maintenance is the Commer practice of chromium plating the cylinder bores, after previously etching them. Oil is retained in the etched portions, and the hardness of the chromium almost eliminates abrasion, so that the engine hardly ever needs a major overhaul.
On the Thames oil engine the exhaust valves can be rotated. This eliminates any tendency for them to stick, and prevents the build-up of carbon and of heat on the side of the valve. Valve Life is prolonged and the need for attention is reduced.
Another feature of the Thames oil engine is the use of a crankshaft with large-diameter bearings and a relatively short stroke, giving a generous overlap between the main and big end bearings. This practice eliminates any weakness in the webs and makes a stiff, robust shaft, which greatly reduces vibration.
The absence of vibration reduces the risk of fatigue splits in the front Wings or scuttle. This is important, because in remote countries there may not be a welding plant available with which to repair these splits.
The Guy Warrior chassis has compressed-air brakes, for which a compressor is mounted on the side of the engine. Normally this would have an air cleaner on its air intake, but the makers have found that mechanics remember to clean the big main air cleaner which feeds the engine, yet forget to attend to the cleaner on the compressor.
This problem is solved by drilling a hole in the front end of the engine inlet manifold and taking a pipe from there to the compressor intake. The compressor thus draws its air supply through the engine manifold and through the main air cleaner, thus ensuring that pure filtered air reaches the compressor. Moreover, the mechanic has only one cleaner to service.
The engine is not starved of air, because it is found that the compressor pulls additional air through the main cleaner. For hot countries the cleaner is usually of the oil-bath type.
The Thornycroft Big Ben has two oil-filter bowls accessible from underneath the engine at the front of the vehicle. This arrangement is more convenient for servicing than a position higher up, where the bowls would be inside the cab. It is therefore unnecessary to squat on the cab floor in a confined space, and oil cannot be spilled in the cab.
Engine removal usually requires a hoist, but one may not always be available. The Perkins P6 engine in the Jensen can be withdrawn as a sub-assembly, complete with the radiator and gearbox. Every nut or other connection that has to be undone is painted yellow for identification.
A special trolley is supplied by the chassis makers and is pushed underneath the engine until it is hard up against the front axle. A stirrup hanging below the trolley provides a base on which the vehicle jack can stand to take the weight of the engine. After the various controls and connections have been undone the unit can be withdrawn through the front without disturbing the water or exhaust systems.
The Scammell mechanical horse, which is used extensively overseas, has its engine and gearbox in unit with the rear axle. The complete assembly can be removed from the rear of the vehicle, again with the aid of a small trolley. With the Leyland WorIdmaster, the underfloor engine comes out through the side of the vehicle. It is necessary to undo only the three suspension links and the hydraulic stabilizer, also the pipe connections and controls, and the engine can then be lowered by a miniature hoist which spans a trap in the body floor, on to a wheeled trolley or a fork-lift truck.
The underfloor engine can be removed from the A.E.C. Regal Mk. IV (though not from the Reliance) without any external hoist or crane. A special lifting device, in the form of a chain and roller hoist, is built into the vehicle and operated :by the wheel-nut brace in the tool kit. When unbolted from its mountings, with all chassis connections undone, the engine is balanced about a lifting eye which is connected by a pin to the hoist, and it can be lowered to the ground.
On Thornycroft chassis the radiator filler pipe branches into two at the top. One branch is vertical, inside the cab, in a location where it is easy to see the water level. The other branch slopes forwards outside the cab and is useful for filling up. This method avoids the awkwardness of having to climb inside the cab with a can of water.
Although the Scammell 6-ton mechanical horse for home use has an axial-flow water pump, for hot climates it can have instead a centrifugal pump which gives a flow of 19 g.p.m. instead of 13 g.p.m. (at maximum r.p.m.). It is driven by a wider belt, which needs a wider pulley on the crankshaft The total quantity of water remains the same.
A useful design feature for overseas is the location of the Guy Warrior steering box, which is on top of the main chassis frame directly opposite the end of a crossmember. This prevents the twisting of the frame on bumpy roads from affecting the steering.
A small item, but one which is important on the loose roads in some foreign countries, concerns the brake-fluid cross-pipe to the rear wheels on the Austin chassis. Formerly this was clipped to the front of the rear-axle casing, but it has now been removed to the rear in order to avoid damage by stones thrown up by the front wheels.
Most trucks can be supplied with larger tyres for overseas use. For operating on desert sand, such as in the Sudan, where many thousands of British vehicles have been sold since the war, twin tyres are not suitable, and extra-large singles are fitted.
Legislation in Ceylon also insists on single tyres in place of twins for ordinary road work. Finland requires special snow tyres, but all other cold countries prefer ordinary tyres with chains.
Guy Motors have found that on bumpy roads the spare-wheel carrier vibrates and is liable to break, so on the Warrior chassis it is mounted on cylindrical rubber bushes. It is made of 2i-in. by fin, flat mild-steel strip, which is much lighter than that normally employed. Two strips which carry the bulk of the weight are hung from the off side of the chassis frame, where the wheel is stored, and two more extend across to the near-side frame member.
The Jensen chassis has a Tecalemit automatic lubrication unit inside the frame behind the driver. It is operated by the clutch pedal and gives centralized lubrication with an independent supply to each component, varying quantities being metered as required. There are 12 supply pipes feeding 15 points. The constant flow of oil washes the dust out with the surplus oil, thus preventing abrasion by dust which might otherwise occur in hot climates.
On Commer 15-25-cwt. petrolengined vans the normal cab ventilating pipe passes by the right-hand side of the engine, with an outlet in the centre of the dash. The exhaust manifold is on the left-hand side, close to the footwell.
The well can become very hot in the tropics, so for users there an additional ventilation pipe is installed on the left of the van, with an outlet point in the left footwell. The foregoing is not affected by the position of the driver, which can be either on the left or the right.
For use in South America, the Commer 7-ton oiler has an engine tachometer. This allows the driver to drive at the speed which gives the maximum retardation from the engine on long downhill runs.
Many other examples could be quoted, but these few suffice to show how British designers cater for operators overseas who may have few maintenance facilities.