GREATER POWER can reduce costs
Page 119
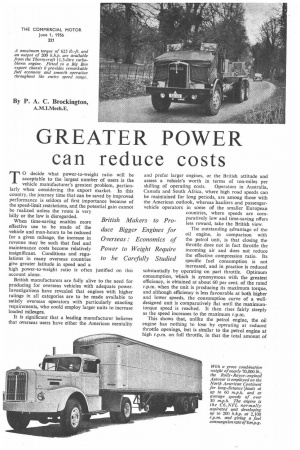
Page 120
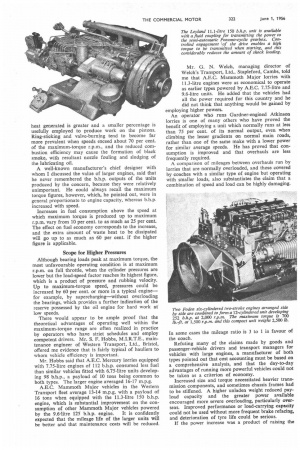
Page 121
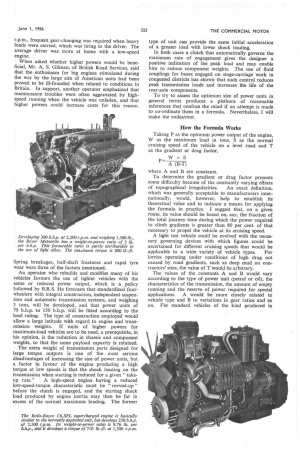
Page 122
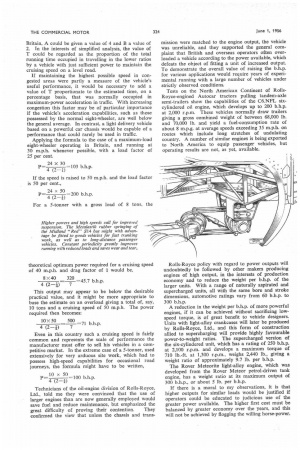
If you've noticed an error in this article please click here to report it so we can fix it.
By P. A. C. Brockington,
A.M.I.Mech.E.
T0 decide what power-to-weight ratio will be acceptable to the largest number of users is the vehicle manufacturer's greatest problem, particularly when considering the export market. In this country, the journey time that can be saved by improved performance is seldom of first importance because of the speed-limit restrictions, and the potential gain cannot be realized unless the route is very hilly or the law is disregarded.
When time-saving enables more effective use to be made of the vehicle and man-hours to be reduced for a given mileage, the increase in revenue may be such that fuel and maintenance costs become relatively insignificant. Conditions and regulations in many overseas countries give greater latitude in speed and a high power-to-weight ratio is often account alone.
British manufacturers are fully alive to the need for producing for overseas vehicles with adequate power. Investigations have revealed that engines with higher ratings in all categories are to be made available to satisfy overseas operators with particularly exacting requirements, who could employ larger units to increase loaded mileages.
It is significant that a leading manufacturer believes that overseas users have either the American mentality justified on this
and prefer larger engines, or the British attitude and assess a vehicle's worth in terms of ton-miles per shilling of operating costs. Operators in Australia, Canada and South Africa, where high road speeds can be maintained for long periods, are among those with the American outlook, whereas hauliers and passenger vehicle operators in some of the smaller European countries, where speeds are com
paratively low and time-saving offers less reward, take the British view. The outstanding advantage of the oil engine, in comparison with the petrol unit, is that closing the throttle does not in fact throttle the incoming air and does not reduce the effective compression ratio. Its specific fuel consumption is not increased, and in practice is reduced substantially by operating on part throttle. Optimum consumption, which is synonymous with the greatest efficiency, is obtained at about 60 per cent. of the rated r.p.m. when the unit is producing its maximum torque, and although efficiency is less favourable at both higher and lower speeds, the consumption curve of a welldesigned unit is comparatively flat until the maximum torque speed is reached. It then rises fairly steeply as the speed increases to the maximum r.p.m.
This shows that, unlike the petrol engine, the oil engine has nothing to lose by operating at reduced throttle openings, but is similar to the petrol engine at high r.p.m. on full throttle, in that the total amount of
heat generated is greater and a smaller percentage is usefully employed to produce work on the pistons. Ring-sticking and valve-burning tend to become far more prevalent when speeds exceed about 70 per cent. of the maximum-torque r.p.m., and the reduced combustion efficiency may cause the formation of black smoke, with resultant nozzle fouling and sludging of the lubricating oil.
A well-known manufacturer's chief designer with whom I discussed the value of larger engines, said that he never remembered the b.h.p. outputs of the units produced by the concern, because they were relatively unimportant. He could always recall the maximum torque figures, however, which, he pointed out, were in general proportionate to engine capacity, whereas b.h.p. increased with speed.
Increases in fuel consumption above the speed at which maximum torque is produced up to maximum r.p.m. vary from 10 per cent, to as much as 25 per cent. The effect on fuel economy corresponds to the increase, and the extra amount of waste heat to be dissipated will go up to as much as 60 per cent. if the higher figure is applicable.
Scope for Higher Pressures Although bearing loads peak at maximum torque, the most unfavourable operating condition is at maximum r.p.m. on full throttle, when the cylinder pressures are lower but the load-speed factor reaches its highest figure, which is a product of pressure and rubbing velocity. Up to maximum-torque speed, pressures could be increased by 60 per cent. or more in a typical engine— for example, by supercharging—without overloading the bearings, which provides a further indication of the reserve possessed by the oil engine for hard work at low speeds.
There would appear to be ample proof that the theoretical advantages of operating well within the maximum-torque range are often realized in practice by operators who have strict schedules and employ competent drivers. Mr. S. F. Hobbs, M.1.R.T.E., maintenance engineer of Western Transport, Ltd., Bristol, offered me evidence that is fairly typical of hauliers to whom vehicle efficiency is important.
Mr. Hobbs said that A.E.C. Mercury lorries equipped with 7.75-litre engines of 112 b.h.p. consumed less fuel than similar vehicles fitted with 6.75-litre units developing 98 b.h.p., a payload of 10 tons being common to both types. The larger engine averaged 16-17 m.p.g.
A.E.C. Mammoth Major vehicles in the Western Transport fleet average 13-14 m.p.g. with a payload of 16 tons when equipped with the 11.3-litre 150 b.h.p. engine, which is substantial improvement on the consumption of other Mammoth Major vehicles powered
by the 9.6-litre 125 b.h.p. engine. It is confidently expected that the mileage life of the larger units will be better and that maintenance costs will be reduced.
Mr. G. N. Welch, managing director of Welch's Transport, Ltd., Stapleford, Cambs, told me that A.E.C. Mammoth Major lorries with 11.3-litre engines were as economical to operate as earlier types powered by A.E.C. 7.75-litre and 9.6-litre units. He added that the vehicles had all the power required for this country and he did not think that anything would be gained by employing higher powers.
An operator who runs Gardner-engined Atkinson lorries is one of many others who have proved the benefit of employing a unit which normally runs at less than 75 per cent. of its normal output, even when climbing the lesser gradients on normal main roads, rather than one of the same make with a lower power for similar average speeds. He has proved that consumption is improved and that overhauls are less frequently required.
A comparison of mileages between overhauls run by lorries that are normally overloaded, and those covered by coaches with a similar type of engine but operating with smaller loads, also substantiates the claim that a combination of speed and load can be highly damaging.
In some cases the mileage ratio is 3 to 1 in favour of the coach.
Refuting many of the claims made by goods and passenger-vehicle drivers and transport managers for vehicles with large engines, a manufacturer of both types pointed out that cost accounting must be based on a comprehensive analysis, and that the day-to-day advantages of running more powerful vehicles could not be taken as a criterion of economy.
Increased size and torque necessitated heavier transmission components, and sometimes chassis frames had to be stiffened. A higher unladen weight reduced payload capacity and the greater power available encouraged more severe overloading, particularly overseas. Improved performance or load-carrying capacity could not be used without more frequent brake refacing, and deterioration of tyre life could be serious.
If the power increase was a product of raising the r.p.m., frequent gear-changing was required when heavy Loads were carried, which was tiring to the driver. The average driver was more at home with a low-speed engine.
When asked whether higher powers would be beneficial, Mr. A. S. Gilman, of British Road Services, said that the enthusiasm for big engines stimulated during the war by the large size of American units had been proved to be ill-founded when related to conditions in Britain. In support, another operator emphasized that maintenance troubles were often aggravated by highspeed running when the vehicle was unladen, and that higher powers could increase costs for this reason.
Spring breakages, half-shaft fractures and rapid tyre wear were three of the factors mentioned.
An operator who rebuilds and modifies many of his vehicles favours the use of lighter vehicles with the same or reduced power output, which is a policy followed by B.R.S. He forecasts that standardized fourwheelers with integral construction, independent suspension and automatic transmission systems, and weighing 3 tons, will be developed, and that power units of 70 b.h.p. to 150 b.h.p. will be fitted according to the load rating. The type of construction employed would allow a large latitude with regard to engine and transmission weights. If units of higher powers for maximum-load vehicles are to be used, a prerequisite, in his opinion, is the reduction in chassis and component weights, so that the same payload capacity is retained.
The extra weight of transmission parts designed for large torque outputs is one of the most serious disadvantages of increasing the size of power units, but a factor in favour of the engine producing a high torque at low speeds is that the shock loading on the transmission when starting is reduced for a given "take up rate." A high-speed engine having a reduced low-speed-torque characteristic must be " revved-up " before the clutch is engaged, and the starting shock load produced by engine inertia may then be far in excess of the normal maximum loading. The former type of unit can provide the same initial acceleration of a greater load with lower shock loading.
In both cases a clutch that automatically governs the maximum rate of engagement gives the designer a positive indication of the peak load and may enable him to reduce component weights. The use of fluid couplings for buses engaged on stage-carriage work in congested districts has shown that such control reduces peak transmission loads and increases the life of the rear-axle components.
To try to assess the optimum size of power units in general terms produces a plethora of reasonable inferences that confuse the mind if an attempt is made to co-ordinate them in a formula. Nevertheless, I will make the endeavour.
How the Formula Works Taking P as the optimum power output of the engine, W as the maximum load in tons, S as the normal cruising speed of the vehicle on a level road and T as the gradient or drag factor, P W x S A (B-T)
where A and B are constants.
To determine the gradient or drag factor presents some difficulty because of the constantly varying effects
of topographical irregularities. An exact definition, which was generally acceptable to manufacturers internationally, would, however, help to establish its theoretical value and to indicate a means for applying the formula in practice. I suggest that, on a given route, its value should be based on, say, the fraction of the total journey time during which the power required to climb gradients is greater than 80 per cent. of that necessary to propel the vehicle at its cruising speed.
A light test vehicle could be evolved with the necessary governing devices with which figures could be ascertained for different cruising speeds that would be
applicable to a wide variety of vehicle types. For lorries operating under conditions of high drag not caused by road gradients, such as deep mud on contractors' sites, the value of T would be arbitrary.
The values of the constants A and B would vary according to the type of power unit (petrol or oil), the characteristics of the transmission, the amount of empty running and the reserve of power required for special applications. A would be more closely related to vehicle type and B to variations in gear ratios and so on. For standard vehicles of the kind produced in Britain, A could be given a value of 4 and B a value of 2. In the interests of simplified analysis, the value of T could be regarded as the proportion of the total running time occupied in travelling in the lower ratios by a vehicle with just sufficient power to maintain the cruising speed on a level road.
If maintaining the highest possible speed in congested areas were partly a measure of the vehicle's useful performance, it would be necessary to add a value of T proportionate to the estimated time, on a percentage basis, that was normally occupied in maximum-power acceleration in traffic. With increasing congestion this factor may be of particular importance if the vehicle's acceleration capabilities, such as those possessed by the normal eight-wheeler, are well below the general average. In contrast, a light delivery vehicle based on a powerful car chassis would be capable of a performance that could rarely be used in traffic.
Applying the formula to the case of a maximum-load eight-wheeler operating in Britain, and running at 30 m.p.h. whenever possible, with a load factor of 25 per cent.
24 x 30 =13 P=4 (2-1)0 b.h.p.
If the speed is raised to 50 m.p.h. and the load factor is 50 per cent., 24 x 50 —200 b.h.p.
For a 5-tonner with a gross load of 8 tons, the theoretical optimum power required for a cruising speed of 40 m.p.h. and drag factor of would be, 8 X 40 320 4 (2-4) 7 —45.7 b.h.p.
This output may appear to be below the desirable practical value, and it might be more appropriate to base the estimate on an overload giving a total of, say, 10 tons and a cruising speed of 50 m.p.h. The power required then becomes: Even in this country such a cruising speed is fairly common and represents the scale of performance the manufacturer must offer to sell his vehicles in a competitive market. In the extreme case of a 5-tonner, used extensively for very arduous site work, which had to possess high-speed capabilities for occasional road journeys, the formula might have to be written, P= 410(2x-510) --100 b.h.p.
Technicians of the oil-engine division of Rolls-Royce, Ltd., told me they were convinced that the use of larger engines than are now generally employed would save fuel and reduce maintenance, but emphasized the great difficulty of proving their contention. They confirmed the view that unless the chassis and trans mission were matched to the engine output, the vehicle was unreliable, and they supported the general complaint that British and overseas operators often overloaded a vehicle according to the power available, which defeats the object of fitting a unit of increased output. To demonstrate the overall value of raising the b.h.p. for various applications would require years of experimental running with a large number of vehicles under strictly observed conditions.
Tests on the North American Continent of RollsRoyce-engined Autocar tractors pulling tandem-axle semi-trailers show the capabilities of the C6.NFL sixcylindered oil engine, which develops up to 200 b.h.p. at 2,000 r.p.m. These vehicles normally draw trailers giving a gross combined weight of between 68,000 lb. and 70,000 lb. and yield a fuel-consumption rate of about 8 m.p.g. at average speeds exceeding 35 m.p.h. on routes which include long stretches of undulating country. A number of similar engines is being exported to North America to equip passenger vehicles, but operating results are not, as yet, available.
Rolls-Royce policy with regard to power outputs will undoubtedly be followed by other makers producing engines of high output, in the interests of production economy and to reduce the weight per b.h.p. of the larger units. With a range of naturally aspirated and supercharged units, all with the same bore and stroke dimensions, automotive ratings vary from 60 b.h.p. to 300 b.h.p.
A reduction in the weight per b.h.p. of more powerful engines, if it can be achieved without sacrificing lowspeed torque, is of great benefit to vehicle designers. Units with light-alloy crankcases will later be produced by Rolls-Royce. Ltd., and this form of construction allied to supercharging will provide highly favourable power-to-weight ratios. The supercharged version of the six-cylindered unit, which has a rating of 250 b.h.p. at 2,100 r.p.m. and develops a maximum torque of 710 lb.-ft. at 1,300 r.p.m., weighs 2,440 lb., giving a weight ratio of approximately 9.7 lb. per b.h.p.
The Rover Meteorite light-alloy engine, which was developed from the Rover Meteor petrol-driven tank engine, has a weight ratio at its maximum output of 300 b.h.p., or about 5 lb. per b.h.p.
If there is a moral to my observations, it is that higher outputs for similar loads would be justified if operators could be educated to judicious use of the greater power available. The higher first cost must be balanced by greater economy over the years, and this will not be achieved by flogging the willing horse-power.