A NOSE FOR PROGRESS
Page 60
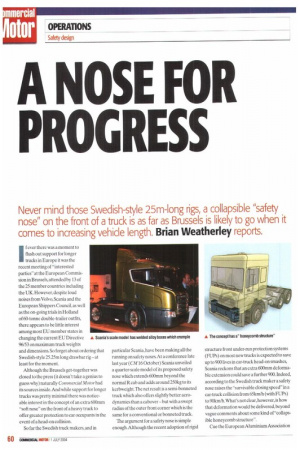
Page 61
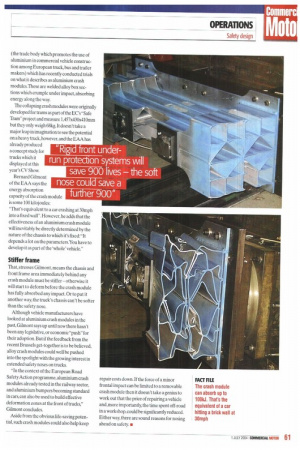
If you've noticed an error in this article please click here to report it so we can fix it.
Never mind those Swedish-style 25m-long rigs, a collapsible "safety nose" on the front of a truck is as far as Brussels is likely to go when it comes to increasing vehicle length. Brian Weatherley reports.
1 f ever there was a moment to flush out support for longer trucks in Europe it was the recent meeting of "interested parties" at the European Commission in Brussels, attended by 13 of the 25 member countries including the UK. However, despite loud noises from Volvo, Scania and the European Shippers Council. as well as the on-going trials in Holland of 60-tonne double-trailer outfits, there appears to be little interest among most EU member states in changing the current ELT Directive 96/53 on maximum truck weights and dimensions. So forget about ordering that Swedish-style 25.25m long drawbar rig — at least for the moment.
Although the Brussels get-together was closed to the press (it doesn't take a genius to guess why) naturally Commercial Motor had its sources inside. And while support for longer trucks was pretty minimal there was noticeable interest in the concept of an extra 600nun "soft nose" on the front of a heavy truck to offer greater protection to car occupants in the event of a head-on collision.
So far the Swedish truck makers, and in particular Scania, have been making all the running on safety noses. At a conference late last year (CM 16 October) Scathe unveiled a quarter-scale model of its proposed safety nose which extends 600nun beyond the normal R cab and adds around 250kg to its kerbweight.The net result is a semi-bonneted truck which also offers slightly better aerodynamics than a cabover — but with a swept radius of the outer front corner which is the same for a conventional or bonneted truck.
The argument for a safety nose is simple enough.Although the recent adoption of rigid structure front under-run protection systems (FUPs) on most new trucks is expected to save up to 900 lives in car-truck head-on smashes, Scania reckons that an extra 600mm deformable extension could save a further 900. Indeed, according to the Swedish truck maker a safety nose raises the "survivable closing speed" in a car-truck collision from 65km/h (with FUPs) to 90km/h.What's not clear, however, is how that deformation would be delivered, beyond vague comments about some kind of "collapsible honeycomb structure".
Cue the European Aluminium Association (the trade body which promotes the use of aluminium in commercial vehicle construction among European truck, bus and trailer makers) which has recently conducted trials on what it describes as aluminium crash modules.These are welded alloy box sections which crumple under impact, absorbing energy along the way.
The collapsing crash modules were originally developed for trains as part of the EC's "Safe Tram" project and measure 1,457x430x410mm but they only weigh 68kg. It doesn't take a major leap in imagination to see the potential on a heavy truck, however, and the EAA has already produced a concept study for trucks which it displayed at this year's CV Show.
Bernard Gilmont of the EAA says the energy absorption capacity of the crash module is some 100 kilojoules: "That's equivalent to a car crashing at 30mph into a fixed wall". However, he adds that the effectiveness of an aluminium crash module will inevitably be directly determined by the nature of the chassis to which it's fixed: "It depends a lot on the paratneters.You have to develop it as part of the 'whole' vehicle."
Stiffer frame
That, stresses Gilmont, means the chassis and front frame area immediately behind any crash module must be stiffer — otherwise it will start to deform before the crash module has fully absorbed any impact. Or to put it another way, the truck's chassis can't be softer than the safety nose.
Although vehicle manufacturers have looked at aluminium crash modules in the past, Gilmont says up until now there hasn't been any legislative, or economic "push" for their adoption. But if the feedback from the recent Brussels get-together is to be believed, alloy crash modules could well be pushed into the spotlight with the growing interest in extended safety noses on trucks.
-In the context of the European Road Safety Action programme, aluminium crash modules already tested in the railway sector, and aluminium bumpers becoming standard in cars, can also be used to build effective deformation zones at the front of trucks," Gilmont concludes.
Aside from the obvious life-saving potential, such crash modules could also help keep repair costs down. If the force of a minor frontal impact can be limited to a removable crash module then it doesn't take a genius to work out that the price of repairing a vehicle and,more importantly, the time spent off-road in a workshop, could be significantly reduced. Either way, there are sound reasons for nosing ahead on safety.