IT'S a big job, distributing more than 26 million gallons
Page 92
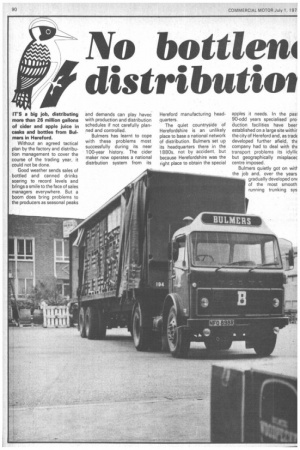
Page 93
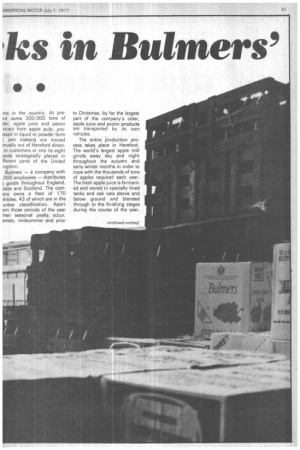
Page 94
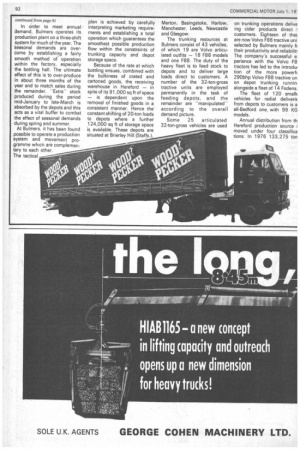
Page 95
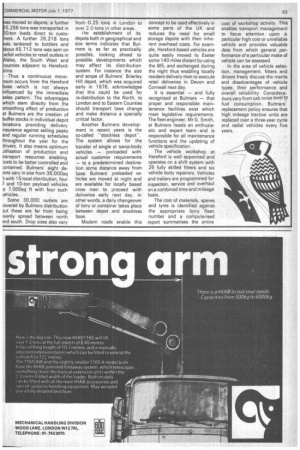
If you've noticed an error in this article please click here to report it so we can fix it.
of cider and apple juice in casks and bottles from Sulmars in Hereford.
Without an agreed tactical plan by the factory and distribution management to cover the course of the trading year, it could not be done.
Good weather sends sales of bottled and canned drinks soaring to record levels and brings a smile to the face of sales managers everywhere. But a boom does bring problems to the producers as seasonal peaks and demands can play havoc with production and distribution schedules if not carefully planned and controlled.
Bulmers has learnt to cope with these problems most successfully during its near 100-year history. The cider maker now operates a national distrbution system from its Hereford manufacturing headquarters.
The quiet countryside of Herefordshire is an unlikely place to base a national network of distribution. Bulmers set up its headquarters there in the 1880s, not by accident, but because Herefordshire was the right place to obtain the special apples it needs. In the past 90-odd years specialised pro. duction facilities have beer established on a large site withir the city of Hereford and, as tradE developed further afield, thE company had to deal with thE transport problems its idyllic but geographically rnisplacec centre imposed.
Bulmers quietly got on witf the job and, over the years gradually developed on of the most smooth running trunking sys ms in the country. At pre!nt some 300,000 tons of der, apple juice and pectin xtract from apple pulp, proJssed in liquid or powder form r jam makers) are moved mually out of Hereford directto customers or into its eight pots strategically placed in fferent parts of the United ngdom.
Bulmers — a company with ,000 employees — distributes 3 goods throughout England, /ales and Scotland. The corn3ny owns a fleet of 170 ?hides, 43 of which are in the unker classification. Apart om those periods of the year 'hen seasonal peaks occur, amely, midsummer and prior
to Christmas, by far the largest part of the company's cider, apple juice and pectin products are transported by its own vehicles.
The entire production process takes place in Hereford. The world's largest apple mill grinds away day and night throughout the autumn and early winter months in order to cope with the thousands of tons of apples required each year. The fresh apple juice is fermented and stored in specially lined tanks and oak vats above and below ground and blended through to the finishing stages during the course of the year.
_ In Order to meet annual demand, Bulmers operates its production plant on a three-shift system for much of the year. The 'seasonal demands are overcome by establishing a fairly smooth method of operation within the factory, especially the bottling hall. The ultimate effect of this is to over-produce in about three months of the year and to match sales during the remainder. "Extra" stock produced during the period mid-January to late-March is absorbed by the depots and this acts as a vital buffer to combat the effect of seasonal demands during spring and summer.
At Bulmers, it has been found possible to operate a production system and movement programme which are complementary to each other. The tactical plan is achieved by carefully interpreting marketing requirements and establishing a total operation which guarantees the smoothest possible production flow within the constraints of trunking capacity and depot storage space.
Because of the rate at which bottling ensues, combined with the bulkiness of crated and cartoned goods, the receiving warehouse in Hereford — in spite of its 91,000 sq ft of space — is dependent upon the • removal of finished goods in a consistent manner. Hence the constant shifting of 20-ton loads to depots where a furthet 124,000 sq ft of storage space is available. These depots are situated at Brierley Hill (Staffs.). Merton, Basingstoke, Harlow, Manchester, Leeds, Newcastle and Glasgow.
The trunking resources at Bulmers consist of 43 vehicles, of which 19 are Volvo articulated outfits — 18 F86 models and one F88. The duty of the heavy fleet is to feed stock to depots and to deliver large loads direct to customers. A number of the 32-ton-gross tractive units are employed permanently in the task of feeding depots, and the remainder are -manipulated"_ according to the overall demand picture.
Some 25 articulated 32-ton-gross vehicles are used
on trunking operations delive ing cider products direct I customers. Eighteen of the are now Volvo F86 tractive uni. selected by Bulmers mainly f( their productivity and reliabilit, The company's successful e: perience with the Volvo F8 tractors has led to the introdui tion of the more powerft 290bhp Volvo F88 tractive un on depot trunking runnift alongside a fleet of 14 Fodens.
The fleet of 120 small( vehicles for radial deliverie from depots to customers is a all-Bedford one with 99 KG models.
Annual distribution from th Hereford production source i moved under four classifica tions. In 1976 133,275 ton
was moved to depots; a further 5,256 tons was transported in 20-ton loads direct to custo-ners. A further 26,318 tons as tankered to bottlers and 3bout 45,712 tons was sent on -adial vehicles to retail outlets in iNales, the South West and counties adjacent to Hereford;hire.
Thus a continuous movement occurs from the Hereford base which is not always influenced by the immediate sales pattern. The advantages which stem directly from the smoothing effect of production at Bulmers are the creation of buffer stocks in individual depot locations providing delivery insurance against selling peaks and regular running schedules throughout the year for the irivers. It also means optimum Jtilisation of production and transport resources enabling costs to be better controlled and contained. Bulmers' eight depots vary in size from 36,000sq 't with 15 local distribution, four 7 and 10-ton payload vehicles o 7,000sq ft with four such iehicles.
Some 30,000 outlets are covered by Bulmers distribution put these are far from being .3venly spread between north 3nd south. Drop sizes also vary from 0.25 tons in London to over 2.0 tons in other areas.
I he establishment of its depots both in geographical and size terms indicates that Bulmers is, as far as practically possible, looking ahead to possible developments which may affect its distribution system. For instance the size and scope of Bulmers' Brierley 'Hill depot, which was acquired early in 1976, acknowledges that this could be used for re-distribution to the North, to London and to Eastern Counties should transport laws change and make distance a specially critical factor.
Another Bulmers development in recent years is the so-called "stockless depot... The system allows for the transfer of single or swop-body vehicles — preloaded with actual customer requirements — to a predetermined destination some distance away from base. Bulmers' preloaded vehicles are moved at night and are available for locally based crew men to proceed with deliveries early next day. In other words, a daily changeover of lorry or container takes place between depot and stockless base.
Modern roads enable this concept to be used effectively in some parts of the UK and reduces the need for small storage depots with their inherent overhead costs. For example, Hereford-based vehicles are quite easily moved to Exeter some 140 miles distant by using the M5, and exchanged during the night thus enabling locally resident delivery men to execute retail deliveries in Devon and Cornwall next day.
It is essential — and fully recognised at BuIrners — that proper and responsible maintenance facilities exist which meet legislative requirements. The fleet engineer, Mr G. Smith, at Bulmers heads an enthusiastic and expert team and is responsible for all maintenance functions and the updating of vehicle specification.
The vehicle workshop at Hereford is well appointed and operates on a shift system with 26 fully skilled fitters and six vehicle body repairers. Vehicles and trailers are programmed for inspection, service and overhaul on a combined time and mileage basis.
The cost of materials, spares and tyres is identified against the appropriate lorry fleet number and a computerised report summarises the entire cost of workshop activity. This enables transport management to focus attention upon a particular high cost or unreliable vehicle and provides valuable data from which general performance of a particular make of vehicle can be assessed.
In the area of vehicle selection, management, fitters and drivers freely discuss the merits and disadvantages of vehicle types, their performance and overall reliability. Considerations vary from-cab noise level to fuel consumption. Bulmers' replacement policy ensures that high mileage tractive units are replaced over a three-year cycle and radial vehicles every five years.