One-piece glassfibre tipper body saves 5 cwt
Page 33
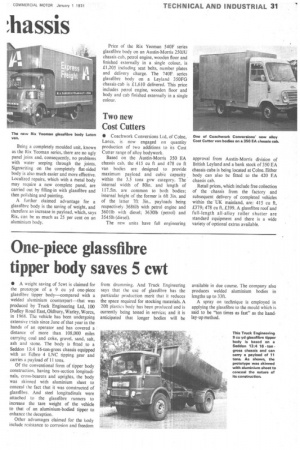
If you've noticed an error in this article please click here to report it so we can fix it.
• A weight saving of 5cwt is claimed for the prototype of a 9 cu yd one-piece glassfibre tipper body—compared with a welded aluminium counterpart—that was produced by Truck Engineering Ltd, 100 Dudley Road East, Oldbury, Warley, Worcs, in 1968. The vehicle has been undergoing extensive trials since June of that year in the hands of an operator and has covered a distance of more than 108,000 miles carrying coal and coke, gravel, sand, salt, ash and stone. The body is fitted to a Seddon 13:4 16-ton-gross chassis equipped with an Edbro4 LNC tipping gear and carries a payload of 11 tons.
Of the conventional form of tipper body construction, having box-section longitudinals, cross-bearers and uprights, the body was skinned with aluminium sheet to conceal the fact that it was constructed of glassfibre. And steel longitudinals were attached to the glassfibre runners to increase the tare weight of the vehicle to that of an aluminium-bodied tipper to enhance the deception.
Other advantages claimed for the body include resistance to corrosion and freedom
from drumming. And Truck Engineering says that the use of glassfibre has the particular production merit that it reduces the space required for stocking materials. A 20ft plastics body has been produced and is currently being tested in service; and it is anticipated that longer bodies will be
available in due course. The company alsQ produces welded aluminium bodies in lengths up to 33ft.
A spray on technique is employed in applying the glasshbre to the mould which is said to be "ten times as fast" as the handlay-up method.