Dirty work in the workshop
Page 121
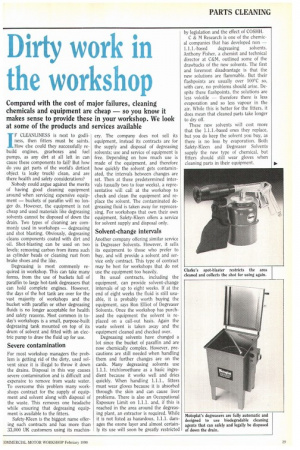
Page 122
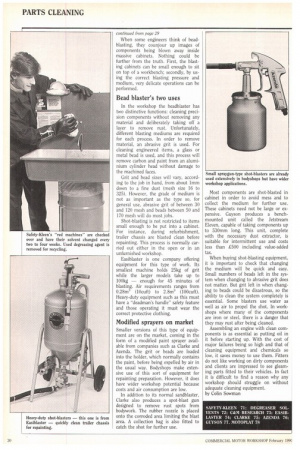
If you've noticed an error in this article please click here to report it so we can fix it.
Compared with the cost of major failures, cleaning chemicals and equipment are cheap — so you know it makes sense to provide these in your workshop. We look at some of the products and services available
IF CLEANLINESS is next to godliness, then fitters must be saints. How else could they successfully rebuild engines, gearboxes and fuel pumps, as any dirt at all left in can cause these components to fail? But how do you get parts of the world's dirtiest object (a leaky truck) clean, and are there health and safety considerations?
Nobody could argue against the merits of having good cleaning equipment around when servicing expensive equipment — buckets of paraffin will no longer do. However, the equipment is not cheap and used materials like degreasing solvents cannot be disposed of down the drain. Two types of cleaning are commonly used in workshops — degreasing and shot blasting. Obviously, degreasing cleans components coated with dirt and oil. Shot-blasting can be used on two levels: removing carbon from items such as cylinder heads or cleaning rust from brake shoes and the like.
Degreasing is most comrnenly required in workshop. This can take many forms, from the use of buckets full of paraffin to large hot-tank degreasers that can hold complete engines. However, the days of the hot tank are over for the vast majority of workshops and the bucket with paraffin or other degreasing fluids is no longer acceptable for health and safety reasons. Most common in today's workshops is a small, purpose-built degreasing tank mounted on top of its drum of solvent and fitted with an electric pump to draw the fluid up for use.
Severe contamination
For most workshop managers the problem is getting rid of the dirty, used solvent since it is illegal to throw it down the drains. Disposal in this way causes severe contamination and is difficult and expensive to remove from waste water. To overcome this problem many workshops contract for the supply of equipment and solvent along with disposal of the waste. This removes one headache while ensuring that degreasing equipment is available to the fitters.
Safety-Kleen is the biggest name offering such contracts and has more than 33,000 UK customers using its machin ery. The company does not sell its equipment, instead its contracts are for the supply and disposal of degreasing solvents; use and service of equipment is free. Depending on how much use is made of the equipment, and therefore how quickly the solvent gets contaminated, the intervals between changes are set. Then at these predetermined intervals (usually two to four weeks), a representative will call at the workshop to check and clean the equipment and replace the solvent. The contaminated degreasing fluid is taken away for reprocessing. For workshops that own their own equipment, Safety-Kleen offers a service for solvent supply and disposal only.
Solvent-change intervals Another company offering similar service is Degreaser Solvents. However, it sells its equipment to those who prefer to buy, and will provide a solvent and service only contract. This type of contract may be best for workshops that do not use the equipment too heavily.
Its usual contracts, including the equipment, can provide solvent-change intervals of up to eight weeks. If at the end of eight weeks the fluid is still usuable, it is probably worth buying the equipment, says Ron Elliot of Degreaser Solvents. Once the workshop has purchased the equipment the solvent is replaced on a call-out basis. Again the waste solvent is taken away and the equipment cleaned and checked over.
Degreasing solvents have changed a lot since the bucket of paraffin and are now chemically complex. However, precautions are still needed when handling them and further changes are on the cards. Many degreasing solvents use 1.1.1. trichloroethane as a basic ingredient because it works well and dries quickly. When handling 1.1.1., fitters must wear gloves because it is absorbed through the skin and can cause liver problems. There is also an Occupational Exposure Limit on 1.1.1. and, if this is reached in the area around the degreasing plant, an extractor is required. While it is not listed as hazardous, 1.1.1. damages the ozone layer and almost certainly its use will soon he greatly restricted
by legislation and the effect of COSHH. C & M Research is one of the chemic al companies that has developed non
1.1.1.-based degreasing solvents. Anthony Fisher, a chemist and technical director at C&M, outlined some of the drawbacks of the new solvents. The first and foremost disadvantage is that the new solutions are flammable. But their flashpoints are usually over 100°C so, with care, no problems should arise. Despite these flashpoints, the solutions are less volotile — therefore there is less evaporation and so less vapour in the air. While this is better for the fitters, it does mean that cleaned parts take longer to dry off.
These new solvents will cost more that the 1.1.1.-based ones they replace, but you do keep the solvent you buy, as there is no loss by evaporation. Both Safety-Kleen and Degreaser Solvents supply the new type of chemical, but fitters should still wear gloves when cleaning parts in their equipment. When some engineers think of beadblasting, they counjour up images of components being blown away inside massive cabinets. Nothing could be further from the truth. First, the blasting cabinets can be small enough to sit on top of a workbench; secondly, by using the correct blasting pressure and medium, very delicate operations can be performed.
Bead blaster's two uses
In the workshop the beadblaster has two distinctive functions: cleaning precision components without removing any material and deliberately taking off a layer to remove rust. Unfortunately, different blasting mediums are required for each process. In order to remove material, an abrasive grit is used. For cleaning engineered items, a glass or metal bead is used, and this process will remove carbon and paint from an aluminium cylinder head without damage to the machined faces.
Grit and bead sizes will vary, according to the job in hand, from about lmm down to a fine dust (mesh size 16 to 325). However, the grade of medium is not as important as the type so, for general use, abrasive grit of between 30 and 120 mesh and beads between 50 and 170 mesh will do most jobs.
Shot-blasting is not restricted to items small enough to be put into a cabinet. For instance, during refurbishment, trailer chassis are blasted clean before repainting. This process is normally carried out either in the open or in an unfurnished workshop.
Easiblaster is one company offering equipment for this type of work. Its smallest machine holds 25kg of grit while the larger models take up to 100kg — enough for 45 minutes of blasting. Air requirements ranges from (10cuft) to 2.8m3 (100cuft). Heavy-duty equipment such as this must have a "deadman's handle" safety feature and those operating it must wear the correct protective clothing.
Modified sprayers on market
Smaller versions of this type of equipment are on the market, coming in the form of a modified paint sprayer available from companies such as Clarke and Azenda. The grit or beads are loaded into the holder, which normally contains the paint, before being expelled by air in the usual way. Bodyshops make extensive use of this sort of equipment for repainting preparation. However, it does have wider workshop potential because costs and air consumption are low.
In addition to its normal sandblaster, Clarke also produces a spot-blast gun designed to remove rust spots from bodywork. The rubber nozzle is placed onto the corroded area limiting the blast area. A collection bag is also fitted to catch the shot for further use. Most components are shot-blasted in cabinet in order to avoid mess and to collect the medium for further use. These cabinets need not be large or expensive. Guyson produces a benchmounted unit called the Jetstrearn Eleven, capable of taking components up to 530mm long. This unit, complete with the necessary dust extractor, is suitable for intermittent use and costs less than £500 including value-added tax.
When buying shot-blasting equipment, it is important to check that changing the medium will be quick and easy. Small numbers of beads left in the system when changing to abrasive grit does not matter. But grit left in when changing to beads could be disastrous, so the ability to clean the system completely is essential. Some blasters use water as well as air to propel the shot. In workshops where many of the components are iron or steel, there is a danger that they may rust after being cleaned.
Assembling an engine with clean components is as essential as putting oil in it before starting up. With the cost of major failures being so high and that of cleaning equipment and chemicals so low, it saves money to use them. Fitters do not like working on dirty components and clients are impressed to see gleaming parts fitted to their vehicles. In fact it is difficult to find a reason why any workshop should struggle on without adequate cleaning equipment.
by Cohn Sowman