Bulk Refuse Disposal—A New System
Page 11
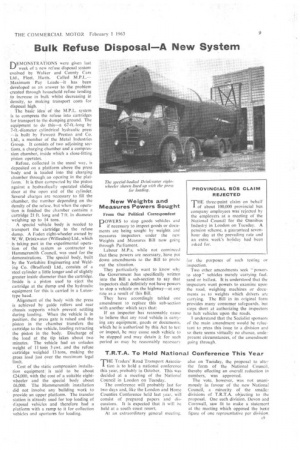
If you've noticed an error in this article please click here to report it so we can fix it.
DEMONSTRATIONS were given last week of -a new refuse disposal system evolved by Walker and County Cars Ltd., Fleet, Hants. Called M.P.L.— Maximum Pay Loads—it has been developed as an answer to the problem created through household refuse tending to increase in bulk whilst decreasing in density, so making transport costs for disposal high.
The basic idea of the M.P.L. system is to compress the refuse into cartridges for transport to the dumping ground. The equipment to do this—a 67-ft.-long by 7-ft.-diameter cylindrical hydraulic press —is built by Fawcett Preston and Co. Ltd., a member of the Metal Industries Group. It consists of two adjoining sections, a charging chamber and a compression chamber, inside which a close-fitting piston operates.
Refuse, collected in the usual way, is deposited on a platform above the press body and is loaded into the charging chamber through an opening in the platform. It is then compacted by the piston against a hydraulically operated sliding door at the open end of the cylinder. Several charges arc necessary to fill the chamber, the number depending on the density of the refuse, but when the operation is finished the chamber contains a cartridge 21 ft. long and 7 ft. in diameter weighing up to 14 tons.
A special vehicle body is needed to transport the cartridge to the refuse dump. A Foden eight-wheeler owned by W._ W. Drinkwater (Willesden) Ltd., which is taking part in the experimental operation of the system as contractor to Hammersmith Council. was used for the demonstrations. The special body, built by the Yorkshire Engineering and Welding Co. (Bradford) Ltd., consists of a steel cylinder a little longer and of slightly greater inside diameter than the cartridge. Inside is a piston used to eject the cartridge at the dump and the hydraulic equipment for this is carried in a Lutontype head.
Alignment of the body with the press is achieved by guide rollers and rear chassis supports which prevent settling during loading. When the vehicle is in position, the press gate is raised and the piston in the chamber transfers the cartridge to the vehicle, loading retracting the piston in the body. Discharge of the load at the tip takes about two minutes. The vehicle had an unladen weight of 11 torts 3 cwt. and the refuse cartridge weighed 13 tons, making the gross load just over the maximum legal limit.
Cost of the static compression installation equipment is said to be about £24,000, with the cost of a suitable eightwheeler and the special body about £6,000. The Hammersmith installation did not involve any building work to provide an upper platform. The transfer station is already used for top loading of d:sposal vehicles and therefore had a platform with a ramp to it for collection vehicles and apertures for loading.