costing • for maximum
Page 50
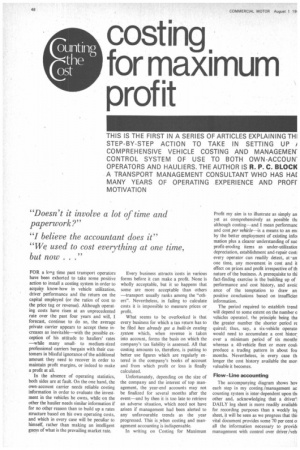
Page 51
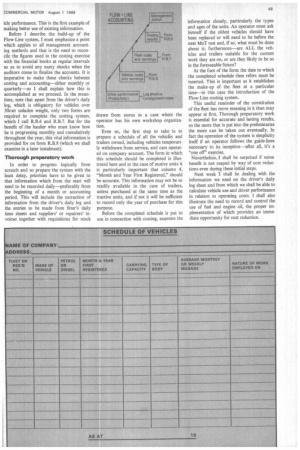
If you've noticed an error in this article please click here to report it so we can fix it.
profit
THIS IS THE FIRST IN A SERIES OF ARTICLES EXPLAINING THI STEP-BY-STEP ACTION TO TAKE IN SETTING UP COMPREHENSIVE VEHICLE COSTING AND MANAGEMEN" CONTROL SYSTEM OF USE TO BOTH OWN-ACCOUN• OPERATORS AND HAULIERS. THE AUTHOR IS R. P. C. BLOCK A TRANSPORT MANAGEMENT CONSULTANT WHO HAS HA( MANY YEARS OF OPERATING EXPERIENCE AND PROF!' MOTIVATION
"Doesn't it involve a lot of time and paperwork?"
"I believe the accountant does it" "We used to cost everything at one time, but now . . ."
FOR a long time past transport operators have been exhorted to take some positive action to install a costing system in order to acquire know-how in vehicle utilization, driver performance and the return on the capital employed (or the ratios of cost to the price tag or revenue). Although operating costs have risen at an unprecedented rate over the past four years and will, I forecast, continue to do so, the average private carrier appears to accept these increases as inevitable—with the possible exception of his attitude to hauliers' rates —while many smallto medium-sized professional carriers bargain with their customers in blissful ignorance of the additional amount they need to recover in order to maintain profit margins, or indeed to make a profit at all.
In the absence of operating statistics, both sides are at fault. On the one hand, the own-account carrier needs reliable costing information in order to evaluate the investment in the vehicles he owns, while on the other the haulier needs similar information if for no other reason than to build up a rates structure based on his own operating costs, and which in every case will be peculiar to himself, rather than making an intelligent guess of what is the prevailing market rate. Every business attracts costs in various forms before it can make a profit. None is wholly acceptable, but it so happens that some are more acceptable than others —transport usually ranks among the "others". Nevertheless, in failing to calculate costs it is impossible to measure prices or profit.
What seems to be overlooked is that every business for which a tax return has to be filed has already got a built-in costing system which, when revenue is taken into account, forms the basis on which the company's tax liability is assessed. All that costing amounts to, therefore, is putting to better use figures which are regularly entered in the company's books of account and from which profit or loss is finally calculated.
Unfortunately, depending on the size of the company and the interest of top management, the year-end accounts may not be finalized for several months after the event—and by then it is too late to retrieve an adverse situation, which need not have arisen if management had been alerted to any unfavourable trends as the year progressed. This is when costing and management accounting is indispensable.
In writing on Costing for Maximum
Profit my aim is to illustrate as simply an yet as comprehensively as possible thi although costing--and I mean performanc and cost per vehicle--is a means to an em by the better employment of existing infoi mation plus a clearer understanding of sue profit-eroding items as under-utilizatior depreciation, establishment and-repair cost: every operator can readily detect, at an one time, any movement in cost and it effect on prices and profit irrespective of th nature of the business. A prerequisite to thi fact-finding exercise is the building up of performance and cost history, and avoid ance of the temptation to draw an positive conclusions based on insufficien information.
The period required to establish trend will depend to some extent on the number c vehicles operated, the principle being tha the greater number the shorter period re quired; thus, say, a six-vehicle operato would need to accumulate a cost histor: over a minimum period of six months whereas a 40-vehicle fleet or more coul( produce a trading pattern in about fou months. Nevertheless, in every case till longer the cost history available the mon valuable it becomes.
Flow-Line accounting The accompanying diagram shows hov each step in my costing /management ac counting system is inter-dependent upon the other and, acknowledging that a driver': DAILY log sheet is more readily available for recording purposes than a weekly loi sheet, it will be seen as we progress that thi: vital document provides some 70 per cent oi all the information necessary to providi management with control over driver /veh
icle performance. This is the first example of making better use of existing information.
Before I describe the build-up of the Flow-Line system, I must emphasize a point which applies to all management accounting methods and that is the need to reconcile the figures used in the costing exercise with the financial books at regular intervals so as to avoid any nasty shocks when the auditors come to finalize the accounts. It is imperative to make these checks between costing and accounting—either monthly or quarterly—so I shall explain how this is accomplished as we proceed. In the meantime, note that apart from the driver's daily log, which is obligatory for vehicles over 30cwt unladen weight, only two forms are required to complete the costing system, which I call R.B.6 and R.B.7. But for the benefit of the haulier who must know how he is progressing monthly and cumulatively throughout the year, this vital information is provided for on form R.B.8 (which we shall examine in a later instalment).
Thorough preparatory work In order to progress logically from scratch and so prepare the system with the least delay, priorities have to be given to that information which from the start will need to be recorded daily—preferably from the beginning of a month or accounting period. This will include the extraction of information from the driver's daily log and the entries to be made from fitter's daily time sheets and suppliers' or repairers' invoices together with requisitions for stock drawn from stores in a case where the operator has his own workshop organization.
Even so, the first step to take is to prepare a schedule of all the vehicles and trailers owned, including vehicles temporarily withdrawn from service, and cars operated on company account. The form in which this schedule should be completed is illustrated here and in the case of motive units it is particularly important that column 4, "Month and Year First Registered," should be accurate. This information may not be so readily available in the case of trailers, unless purchased at the sarne time as the tractive units, and if not it will be sufficient to record only the year of purchase for this purpose.
Before the completed schedule is put to use in connection with costing, examine the information closely, particularly the types and ages of the units. An operator must ask himself if the oldest vehicles should have been replaced or will need to be before the next MoT test and, if so, what must be done about it; furthermore—are ALL the vehicles and trailers suitable for the current work they are on, or are they likely to be so in the foreseeable future?
At the foot of the form the date to which the completed schedule then refers must be • inserted. This is important as it establishes the make-up of the fleet at a particular time—in this case the introduction of the Flow-Line costing system.
This useful reminder of the constitution of the fleet has more meaning in it than may appear at first. Thorough preparatory work is essential for accurate and lasting results, so the more that is put into the preliminaries the more can be taken out eventually. In fact the operation of the system is simplicity itself if an operator follows the guide-lines necessary to its inception—after all, it's a "one off" exercise.
Nevertheless, I shall be surprised if sdrrie benefit is not reaped by way of cost reductions even during these initial steps.
Next week shall be dealing with the information we need on the driver's daily log sheet and from which we shall be able to calculate vehicle use and driver performance in relation to operating costs. I shall also illustrate the need to record and control the use of fuel and engine oil, the proper implementation of which provides an immediate opportunity for cost reduction.