A NEW ROLLED-STEEL WHEEL.
Page 9
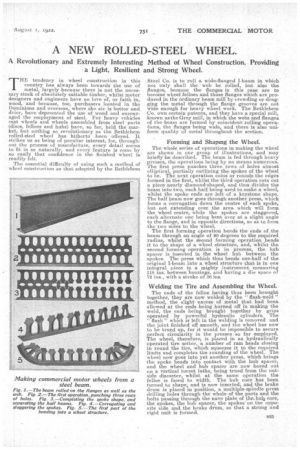
Page 10
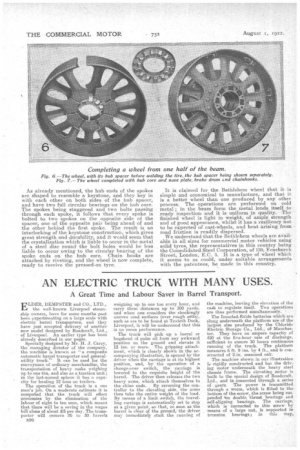
If you've noticed an error in this article please click here to report it so we can fix it.
A Revolutionary and Extremely Interesting Method of Wheel Construction, Providing a Light, Resilient and Strong Wheel.
THE tendency in wheel construction in this country has always been towards the use of metal, largely because there is not the necessary stock of absolutely suitable timber, whilst motor designers and engineers have no love of, or faith in, wood, and because, too, purchasers located in the Dominions and overseas, where the air is hotter and drier, have deprecated the use of wood and encouraged the employment of steel. For heavy vehicles cast wheels and wheels assembled from steel parts (discs, felloes and hubs) have, so far, held the market, but nothing so revolutionary as the Bethlehem rolled-steel wheel has hitherto been offered. It strikes us as being of peculiar interest, for, throughout the process of manufacture, every detail seems to fit in so naturally, and every feature is come by so easily that confidence in the finished wheel is ' readily felt.
.The essential difficulty of using such a method of wheel construction as that adopted by the Bethlehem
Steel Co. is to roll a wide-flanged I-beam in which not only shall the web be rolled, but also the flanges, because the flanges in this ease are to become wheel felloes and those flanges which are produced in the ordinary beam mill by crowding or dragging the metal through the flange grooves are not wide enough for heavy wheel work. The Bethlehem Co. own certain patents, and they have a special mill, known as the Grey mill, in which the webs and flanges of the beam are formed by coincident rolling operations, the flanges being wide, and there is also uniform quality of metal throughout the section.
Forming and Shaping the Wheel.
The whole series of operations in making the wheel are shown in our group of illustrations, and may briefly`be described. The beam is fed through heavy presses, the operations being by no means numerous. The first press punches three rows of holes almost elliptical, partially outlining the spokes of the wheel to be. The next operation coins or rounds the edges formed in the first, whilst the third operation cuts out a piece nearly diamond-shaped, and thus divides the beam into two' each half being used to make a wheel, whilst the spoke ends are left of a keystone shape. The half beam now goes through another press, which forms a corrugation down the centre of each spoke, but not extending over the area which will form the wheel centre, while the spokes are staggered, each alternate one being bent over at a slight angle to the flange, and in opposite directions, so as to form the two sides to the wheel.
The first forming operation bends the ends of the beam through an angle of 90 degrees to the required radius, whilst the second forming operation bends it to the shape of a wheel structure, and, whilst the second forming operation is in process, the hub spacer is inserted in the wheel hub between the spokes. The press which thus bends one-half of the original I-beam into a wheel structure that is in one integral piece is a mighty instrument, measuring 118 ins, between housings, and having a die space of n ins., with a stroke of 36 ins.
Welding the Tire and Assembling the Wheel.
The ends of the felIcie having thus been brought together, they are now welded by the " flash-weld" method, the slight excess of metal that had been allowed at the ends being burned off in making the weld, the ends being brought together• by grips operated by powerful hydraulic cylinders. The " flash " which is left in the welding is removed and the joint finished off smooth, and the wheel has now to be trued up, for it would be impossible to secure perfect circularity in the presses so far employed. The wheel, therefore, is placed in an hydraulically operated tire setter, a number of ram heads closing in round the tire, which squeezes it to the required limits and completes the rounding of the wheel. The wheel now 'goes into yet another press, which brings the spoke heads into contact with the hub spacer, and the wheel and hub spacer are now bored out on a vertical turret lathe, being trued from the outside diameter, whilst at the same operation the feIloe is faced to width. The hub core has been turned to shape, and is now inserted; and the brake drum is placed in position a multiple-spindle press drilling holes through the ;hole of the parts and the bolts passing through the nave plate of the_butc core, the spokes, the hub spacer, the apokes' o the opposite side and the brake drum, so that a strong and rigid unit is formed.
As already mentioned, the hub ends of the spokes are shaped to resemble a keystone, and they key in with each other on both sides of the hub spacer, and have two full circular bearings on the hub core. The spokes being staggered and two bolts passing through each spoke, it follows that every spoke is bolted to two spokes on the opposite side of the spacer, one of the opposite pair being ahead of and the other _behind the first spoke. The result is an interlocking of the keystone construction, which gives great strength and durability, and it would seem that the crystalization which is liable to occur in the metal of a steel disc round the bolt holes would lie lessliable to occur owing to the circular bearing of the spoke ends on the hub core. Chain hooks are attached by riveting, and the wheel is now complete, ready to receive the pressed-on tyre. It is claimed for the Bethlehem wheel that it is simple and economical to manufacture, and that it is a better wheel than one produced by any other process. The operations are performed on cold metal ;. in the beam form the metal lends itself to ready inspection. and it is uniform in quality. The finished wheel is light in weight, of ample strength and of good appearance, whilst it has a resiliency not to he expected of cast-wheels, and heat arising from road friction is readily dispersed.
We understand that the Bethlehem wheels are available in all sizes for commercial motor vehicles using solid tyres, the representatives in this country being the Consolidated Steel Corporation, of 139, Fenchurch Street, London, E.C. 3. It is a ty-ne of wheel which it seems to us could, under suitable arrangements with the patentees, be made in this country.