Fatigue testing and quality assurance the MAN way
Page 65
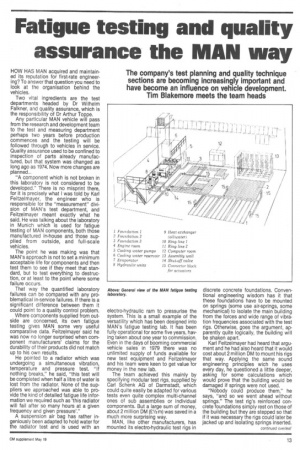
Page 66
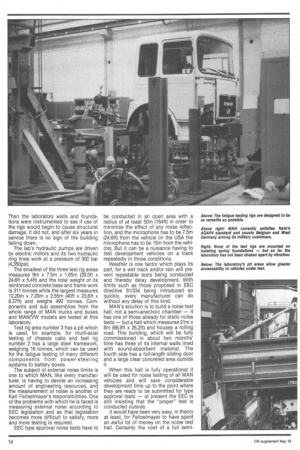
Page 67
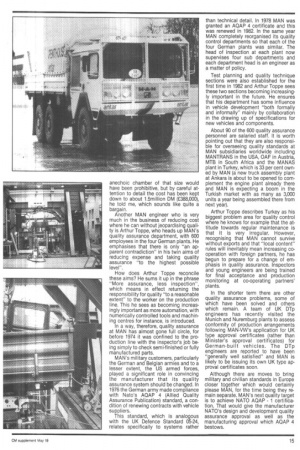
If you've noticed an error in this article please click here to report it so we can fix it.
The company's test planning and quality technique sections are becoming increasingly important and have become an influence on vehicle development. Tim Blakemore meets the team heads
HOW HAS MAN acquired and maintained its reputation for first-rate engineer ing? To answer that question you need to look at the organisation behind the vehicles.
Two vital ingredients are the test departments headed by Dr Wilhelm Falkner, and quality assurance, which is the responsibility of Dr Arthur Toppe.
Any particular MAN vehicle will pass from the research and development team to the test and measuring department perhaps two years before production commences and the testing will be followed through to vehicles in service.
Quality assurance used to be confined to inspection of parts already manufac tured, but that system was changed as long ago as 1974. Now more changes are planned...
"A component which is not broken in this laboratory is not considered to be developed." There is no misprint there, for it is precisely what I was told by Karl Feitzelmayer, the engineer who is responsible for the "measurement' divi sion of MAN's test department, and Feitzelmayer meant exactly what he said. He was talking about the laboratory in Munich which is used for fatigue testing of MAN components, both those manufactured in-house and those supplied from outside, and full-scale vehicles.
The point he was making was that MAN's approach is not to set a minimum acceptable life for components and then test them to see if they meet that standard, but to test everything to destruction, or at least to the point where some failure occurs.
That way the quantified laboratory failures can be compared with any pro blematical in-service failures. If there is a significant difference between them it could point to a quality control problem. Where components supplied from outside are concerned, its own fatigue testing gives MAN some very useful comparative data. Feitzelmayer said he was now no longer surprised when com ponent manufacturers' claims for the durability of their products did not match up to his own results.
He pointed to a radiator which was undergoing a simultaneous vibration, temperature and pressure test. "If nothing breaks," he said, "this test will be completed when half a litre of water is lost from the radiator. None of the sup pliers we approached was able to provide the kind of detailed fatigue life infor mation we required such as 'this radiator will fail after so many hours at a given frequency and given pressure'," A suspension air bag has rather ingeniously been adapted to hold water for the radiator test and is used with an electro-hydraulic ram to pressurise the system. This is a small example of the versatility which has been designed into MAN's fatigue testing lab. It has been fully operational for some five years, having taken about one year to commission. Even in the days of booming commercial vehicle sales in 1979 there was no unlimited supply of funds available for new test equipment and Feitzelmayer and his team were keen to get value for money in the new lab.
The team achieved this mainly by specifying modular test rigs, supplied by Carl Schenk AG of Darmstadt, which could quite easily be adapted for various tests even quite complex multi-channel ones of sub assemblies or individual components. But a large sum of money, about 2 million DM (£1/2m) was saved in a much more surprising way.
MAN, like other manufacturers, has mounted its electro-hydraulic test rigs in discrete concrete foundations. Conventional engineering wisdom has it that these foundations have to be mounted on springs (some use air-springs, some mechanical) to isolate the main building from the forces and wide range of vibration frequencies associated with the test rigs. Otherwise, goes the argument, apparently quite logically, the building will be shaken apart.
Karl Feitzelmayer had heard that argument and he had also heard that it would cost about 2 million DM to mount his rigs that way. Applying the same sound engineering principles wich he uses every day, he questioned a little deeper, asking for some calculations which would prove that the building would be damaged if springs were not used.
"Nobody could produce them," he says, "and so we went ahead without springs." The test rig's reinforced concrete foundations simply rest on those of the building but they are stepped so that if it was necessary the rigs could later be jacked up and isolating springs inserted. Then the laboratory walls and foundations were instrumented to see if use of the rigs would begin to cause structural damage. It did not, and after six years in service there is no sign of the building falling down.
The lab's hydraulic pumps are driven by electric motors and its two hydraulic ring lines work at a pressure of 300 bar (4,350ps i).
The smallest of the three test rig areas measures 9m x 7.5m x 1.65m (29.5ft x 24.6ft x 5.4ft) and the total weight of its reinforced concrete base and frame work is 311 tonnes while the largest measures 12.20m x 7.20m x 2.55m (40ft x 23.6ft x 8.37ft) and weighs 492 tonnes. Components and sub assemblies from the whole range of MAN trucks and buses and MANNW models are tested at this laboratory.
Test rig area number 3 has a pit which is used, for example, for multi-axial testing of chassis cabs and test rig number 2 has a large steel framework, weighing 16 tonnes, which can be used for the fatigue testing of many different components from power-steering systems to battery boxes.
The subject of external noise limits is one to which MAN, like every manufacturer, is having to devote an increasing amount of engineering resources, and the measurement of noise is another of Karl Feitselmayer's responsibilities. One of the problems with which he is faced is measuring external noise according to EEC legislation and as that legislation becomes more difficult to satisfy, more and more testing is required.
EEC type approval noise tests have to be conducted in an open area with a radius of at least 50m (164ft) in order to minimise the effect of any noise reflection, and the microphone has to be 7.5m (24.6ft) from the vehicle (in the USA the microphone has to be 15m from the vehicle). But it can be a nuisance having to test development vehicles on a track repeatedly in those conditions.
Weather is one factor which plays its part, for a wet track and/or rain will prevent repeatable tests being conducted and 'thereby delay development. With limits such as those proposed in EEC directive 81/334 being introduced so quickly, every manufacturer can do without any delay of this kind.
MAN's solution is to build a noise test hall, not a semi-anechoic chamber — it has one of those already for static noise tests — but a hall which measures 21m x 8m (68.9ft x 26.2ft) and houses a rolling road. This building, which will be fully commissioned in about two months' time has three of its internal walls lined with sound-absorbent material. The fourth side has a full-length sliding door and a large clear concreted area outside it When this hall is fully operational it will be used for noise testing of all MAN vehicles and will save considerable development time up to the point where they are ready to be submitted for type approval tests — at present the EEC is still insisting that the "proper" test is conducted outside.
It would have been very easy, in theory at least, for Feitzelmayer to have spent an awful lot of money on the noise test hall. Certainly the cost of a full semi anechoic chamber of that size would have been prohibitive, but by careful attention to detail the cost has been kept down to about 1.5million DM (£388,000), he told me, which sounds like quite a bargain.
Another MAN engineer who is very much in the business of reducing cost where he can without jeopardising quality is Arthur Toppe, who heads up MAN's quality assurance department, with 600 employees in the four German plants. He emphasises that there is only "an apparent contradiction" in his twin aims of reducing expense and taking quality assurance "to the highest possible level".
How does Arthur Toppe reconcile these aims? He sums it up in the phrase "More assurance, less inspection", which means in effect returning the responsibility for quality "to a reasonable extent" to the worker on the production line. This he sees as becoming increasingly important as more automation, with numerically controlled tools and machining centres for instance, is introduced.
In a way, therefore, quality assurance at MAN has almost gone full circle, for before 1974 it was confined to the production line with the inspector's job being simply to check semi-finished or fully manufactured parts.
MAN's military customers, particularly the German and Belgian armies and to a lesser extent, the US armed forces, played a significant role in convincing the manufacturer that its quality assurance system should be changed. In 1976 the German army made compliance with Nato's AQAP 4 (Allied Quality Assurance Publication) standard, a condition of renewing contracts with vehicle suppliers.
This standard, which is analogous with the UK Defence Standard 05-24, relates specifically to systems rather than technical detail. In 1978 MAN was granted an AQAP 4 certificate and this was renewed in 1982. In the same year MAN completely reorganised its quality control departments so that each of the four German plants was similar. The head of inspection at each plant now supervises four sub departments and each department head is an engineer as a matter of policy.
Test planning and quality technique sections were also established for the first time in 1982 and Arthur Toppe sees these two sections becoming increasingly important in the future. He ensures that his department has some influence in vehicle development "both formally and informally" mainly by collaboration in the drawing up of specifications for new vehicles and components.
About 90 of the 600 quality assurance personnel are salaried staff. It is worth pointing out that they are also responsible for overseeing quality standards at MAN subsidiaries worldwide including MANTRANS in the USA, OAF in Austria, MTB in South Africa and the MANAS plant in Turkey, which is 33 per cent owned by MAN (a new truck assembly plant at Ankara is about to be opened to complement the engine plant already there and MAN is expecting a boom in the Turkish market with as many as 3,000 units a year being assembled there from next year).
Arthur Toppe describes Turkey as his biggest problem area for quality control where he knows for example that the attitude towards regular maintenance is that it is very irregular. However, recognising that MAN cannot survive without exports and that "local content" rules will inevitably mean increasing cooperation with foreign partners, he has begun to prepare for a change of emphasis in quality assurance. Inspectors and young engineers are being trained for final acceptance and production monitoring at co-operating partners' plants.
In the shorter term there are other quality assurance problems, some of which have been solved and others which remain. A team of UK DTp engineers has recently visited the Munich and Nuremburg plants to assess conformity of production arrangements following MAN-VW's application for UK type approval certificates (rather than Minister's approval certificates) for German-built vehicles. The Dip engineers are reported to have been "generally well satisfied" and MAN is likely to be issuing its own UK type approval certificates soon.
Although there are moves to bring military and civilian standards in Europe closer together which would certainly please MAN, for the time being they remain separate. MAN's next quality target is to achieve NATO AQAP 1 certification. That would give the manufacturer NATO's design and development quality assurance approval as well as the manufacturing approval which AQAP 4 bestows.