Exacting quality control is engine plant hallmark
Page 62
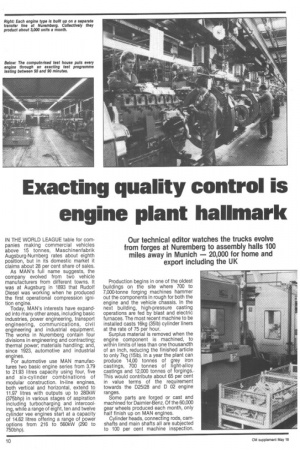
Page 63
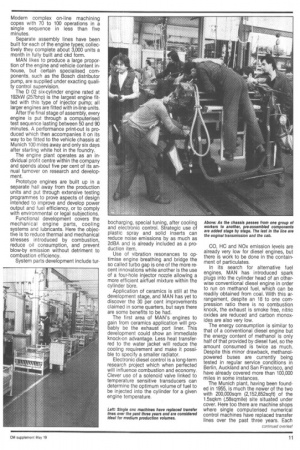
Page 64
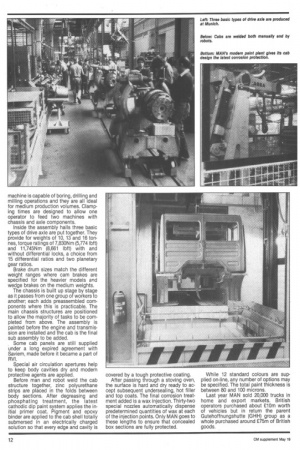
If you've noticed an error in this article please click here to report it so we can fix it.
Our technical editor watches the trucks evolve from forges at Nuremberg to assembly halls 100 miles away in Munich — 20,000 for home and export including the UK
IN THE WORLD LEAGUE table for companies making commercial vehicles above 15 tonnes, Maschinenfabrik Augsburg-Nurnberg rates about eighth position, but in its domestic market it claims about 28 per cent share of sales.
As MAN's full name suggests, the company evolved from two vehicle manufacturers from different towns. It was at Augsburg in 1893 that Rudolf Diesel was working when he produced the first operational compression ignition engine.
Today, MAN's interests have expanded into many other areas, including basic industries, power engineering, transport engineering, communications, civil engineering and industrial equipment. The works in Nuremberg contain four divisions in engineering and contracting; thermal power; materials handling; and, since 1923, automotive and industrial engines. For automotive use MAN manufactures two basic engine series from 3.79 to 21.93 litres capacity using four, five and six-cylinder combinations of modular construction. In-line engines, both vertical and horizontal, extend to 11.97 litres with outputs up to 280kW (375bhp) in various stages of aspiration including turbocharging and intercooling, while a range of eight, ten and twelve cylinder vee engines start at a capacity of 14.62 litres offering a range of power options from 216 to 560kW (290 to 750bhp). Production begins in one of the oldest buildings on the site where 700 to 7,000-tonne forging machines hammer out the components in rough for both the engine and the vehicle chassis. In the next building, high-pressure casting operations are fed by blast and electric furnaces. The most recent machine to be installed casts 16kg (351b) cylinder liners at the rate of 75 per hour.
Surplus material is removed when the engine component is machined, to within limits of less than one thousandth of an inch, reducing the finished article to only 7kg (151b). In a year the plant can produce 14,00 tonnes of grey iron castings, 700 tonnes of light-alloy castings and 12,000 tonnes of forgings.. This would contribute about 65 per cent in value terms of the requirement towards the D25128 and D 02 engine ranges. Some parts are forged or cast and machined for Daimler-Benz. Of the 60,000 gear wheels produced each month, only half finish up on MAN engines.
Cylinder heads, connecting rods, camshafts and main shafts all are subjected to 100 per cent machine inspection. Modern complex on-line machining copes with 70 to 100 operations in a single sequence in less than five minutes.
Separate assembly lines have been built for each of the engine types; collectively they complete about 3,000 units a month in fully built and ckd form.
MAN likes to produce a large proportion of the engine and vehicle content inhouse, but certain specialised components, such as the Bosch distributor pump, are supplied under exacting quality control supervision.
The D 02 six-cylinder engine rated at 192kW (257bhp) is the largest engine fitted with this type of injector pump; all larger engines are fitted with in-line units. After the final stage of assembly, every engine is put through a computerised test sequence lasting between 50 and 90 minutes. A performance print-out is produced which then accompanies it on its way to be fitted to the vehicle chassis at Munich 100 miles away and only six days after starting white hot in the foundry. The engine plant operates as an individual profit centre within the company and spends about five per cent of its annual turnover on research and development.
Prototype engines are built up in a separate hall away from the production units and put through extensive testing programmes to prove aspects of design intended to improve and develop power output and fuel efficiency, or to comply with environmental or legal subjections.
Functional development covers the mechanical engine parts, cooling systems and lubricants. Here the objective is to reduce thermal and mechanical stresses introduced by combustion, reduce oil consumption, and prevent blow-by emission without detriment to combustion efficiency.
System parts development include tur bocharging, special tuning, after cooling and electronic control. Strategic use of plastic spray and solid inserts can reduce noise emissions by as much as 2dBA and is already included as a production item.
Use of vibration resonances to optimise engine breathing and bridge the so called turbo gap is one of the more recent innovations while another is the use of a four-hole injector nozzle allowing a more efficient air/fuel mixture within the cylinder bore.
Application of ceramics is still at the development stage, and MAN has yet to discover the 30 per cent improvements claimed in some quarters, but says there are some benefits to be had.
The first area of MAN's engines to gain from ceramics application will probably be the exhaust port liner. This development could show an immediate knock-on advantage. Less heat transferred to the water jacket will reduce the cooling requirement and make it possible to specify a smaller radiator.
Electronic diesel control is a long-term research project which when perfected will influence combustion and economy. Clever use of a solenoid valve linked to temperature sensitive transducers can determine the optimum volume of fuel to be injected into the cylinder for a given engine temperature. CO, HC and NOx emission levels are already very low for diesel engines, but there is work to be done in the containment of particulates.
In its search for alternative fuel engines, MAN has introduced spark plugs into the cylinder head of an otherwise conventional diesel engine in order to run on methanol fuel, which can be readily obtained from coal. With this arrangement, despite an 18 to one compression ratio there is no combustion knock, the exhaust is smoke free, nitric oxides are reduced and carbon monoxides are also very low.
The energy consumption is similar to that of a conventional diesel engine but the energy content of methanol is only half of that provided by diesel fuel, so the amount consumed is twice as much. Despite this minor drawback, methanolpowered buses are currently being tested in regular service conditions in Berlin, Auckland and San Francisco, and have already covered more than 100,000 miles in some instances.
The Munich plant, having been founded in 1955, is much the newer of the two with 200,000sqm (2,152,852sqft) of the 1.5sqkm (.58sqmile) site situated under cover. Here too there are machine shops where single computerised numerical control machines have replaced transfer lines over the past three years. Each machine is capable of boring, drilling and milling operations and they are all ideal for medium production volumes. Clamping times are designed to allow one operator to feed two machines with chassis and axle components.
Inside the assembly halls three basic types of drive axle are put together. They provide for weights of 10, 13 and 16 tonnes, torque ratings of 7,830Nm (5,774 lbft) and 11,745Nm (8,661 lbft) with and without differential Jocks, a choice from 15 differential ratios and two planetary gear ratios.
Brake drum sizes match the different weight ranges where cam brakes are specified for the heavier models and wedge brakes on the medium weights.
The chassis is built up stage by stage as it passes from one group of workers to another; each adds preassennbled components where this is practicable. The main chassis structures are positioned to allow the majority of tasks to be completed from above. The assembly is painted before the engine and transmission are installed and the cab is the final sub assembly to be added.
Some cab panels are still supplied under a long expired agreement with Saviem, made before it became a part of RVI.
Special air circulation apertures help to keep body cavities dry and modern protective agents are applied.
Before man and robot weld the cab structure together, zinc polyurethane strips are placed in the folds between body sections. After degreasing and phosphating treatment, the latest cathodic dip paint system applies the initial primer coat. Pigment and epoxy binder are applied to the cab shell totally submersed in an electrically charged solution so that every edge and cavity is covered by a tough protective coating.
After passing through a stoving oven, the surface is hard and dry ready to accept subsequent undersealing, hot filler and top coats. The final corrosion treatment added is a wax injection. Thirty-two special nozzles automatically dispense predetermined quantities of wax at each of the injection points. Only MAN goes to these lengths to ensure that concealed box sections are fully protected. While 12 standard colours are supplied on-line, any number of options may be specified. The total paint thickness is between 80 and 100 microns.
Last year MAN sold 20,000 trucks in home and export markets. British operators purchased about £10m worth of vehicles but in return the parent Gutehoffnungshutte (GHH) group as a whole purchased around £75m of British goods.