Energy saving is the long-term r and d goal
Page 60
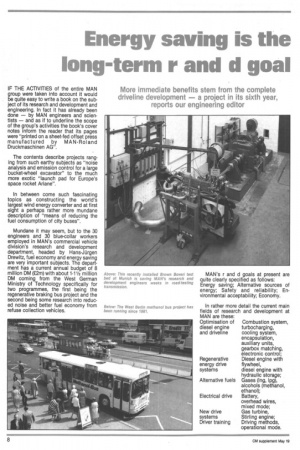
Page 61
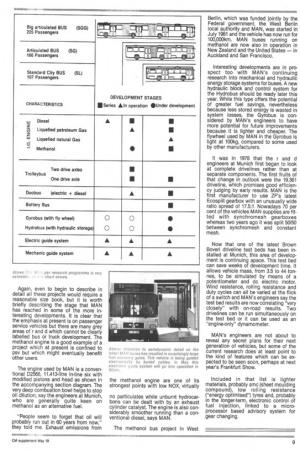
If you've noticed an error in this article please click here to report it so we can fix it.
More immediate benefits stem from the complete driveline development — a project in its sixth year, reports our engineering editor
IF THE ACTIVITIES of the entire MAN group were taken into account it would be quite easy to write a book on the subject of its research and development and engineering. In fact it has already been done — by MAN engineers and scientists — and as if to underline the scope of the group's activities the book's cover notes inform the reader that its pages were "printed on a sheet-fed offset press manufactured by MAN-Roland Druckmaschinen AG".
The contents describe projects ranging from such earthy subjects as "noise analysis and emission control for a large bucket-wheel excavator" to the much more exotic "launch pad for Europe's space rocket Ariane".
In between come such fascinating topics as constructing the world's largest wind energy converter and at first sight a perhaps rather more mundane description of "means of reducing the fuel consumption of city buses".
Mundane it may seem, but to the 30 engineers and 30 blue-collar workers employed in MAN's commercial vehicle division's research and development department, headed by Hans-JOrgen Drewitz, fuel economy and energy saving are very important subjects. The department has a current annual budget of 8 million DM (£2m) with about 1-11/2 million DM coming from the West German Ministry of Technology specifically for two programmes, the first being the regenerative braking bus project and the second being some research into reduced noise and better fuel economy from refuse collection vehicles. MAN's r and d goals at present are quite clearly specified as follows: Energy saving; Alternative sources of energy; Safety and reliability; Environmental acceptability; Economy. Again, even to begin to describe in detail all these projects would require a reasonable size book, but it is worth briefly describing the stage that MAN has reached in some of the more interesting developments. It is clear that the emphasis at present is on passenger service vehicles but there are many grey areas of r and d which cannot be clearly labelled bus or truck development. The methanol engine is a good example of a project which at present is confined to psv but which might eventually benefit other users.
The engine used by MAN is a conventional D2566, 11.413-litre in-line six with modified pistons and head as shown in the accompanying section diagram. The very deep combustion bowl helps to stop oil dilution, say the engineers at Munich, who are generally quite keen on methanol as an alternative fuel.
"People seem to forget that oil will probably run out in 60 years from now," they told me. Exhaust emissions from the methanol engine are one of its strongest points with low NOX, virtually no particulates while unburnt hydrocarbons can be dealt with by an exhaust cylinder catalyst. The engine is also considerably smoother running than a conventional diesel, says MAN. Berlin, which was funded jointly by the Federal government, the West Berlin local authority and MAN, was started in July 1981 and the vehicle has now run for 100,000km. MAN buses running on methanol are now also in operation in New Zealand and the United States — in Auckland and San Francisco.
Interesting developments are in prospect too with MAN's continuing research into mechanical and hydraulic energy storage systems for buses. A new hydraulic block and control system for the Hydrobus should be ready later this year. While this type offers the potential of greater fuel savings, nevertheless because less stored energy is wasted in system losses, the Gyrobus is considered by MAN's engineers to have more potential for future improvements because it is lighter and cheaper. The flywheel used by MAN in the Gyrobus is light at 100kg, compared to some used by other manufacturers.
It was in 1978 that the r and d engineers at Munich first began to look at complete drivelines rather than at separate components. The first fruits of that change in outlook were the 19.361 driveline, which promises good efficiency judging by early results. MAN is the first manufacturer to use ZF's latest Ecosplit gearbox with an unusually wide ratio spread of 17.5:1. Nowadays 70 per cent of the vehicles MAN supplies are fitted with synchromesh gearboxes whereas two years ago it was split 50/50 between synchromesh and constant mesh.
Now that one of the latest Brown Boveri driveline test beds has been installed at Munich, this area of development is continuing apace. This test bed can save weeks of development time. It allows vehicle mass, from 3.5 to 44 tonnes, to be simulated by means of a potentiometer and dc electric motor. Wind resistance, rolling resistance and duty cycles can all be varied at the flick of a switch and MAN's engineers say the test bed results are now correlating "very closely" with on-road results. Two drivelines can be run simultaneously on the test bed or it can be used as an "engine-only" dynamometer.
MAN's engineers are not about to reveal any secret plans for their next generation of vehicles, but some of the current research does at least point to the kind of features which can be expected to be seen soon, perhaps at next year's Frankfurt Show.
Included in that list is lighter materials, probably smc (sheet moulding compound), low rolling resistance ("energy optimised") tyres and, probably in the longer-term, electronic control of fuel injection, linked to a microprocessor based advisory system for gear changing.