COSTS THAT COUNT (10)
Page 73
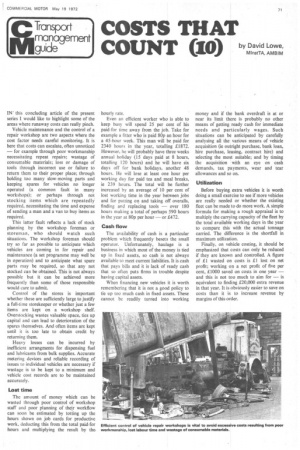
If you've noticed an error in this article please click here to report it so we can fix it.
by David Lowe,
MI nstTA, AIVIBIM IN' this concluding article of the present series I would like to highlight some of the areas where runaway costs can really pinch.
Vehicle maintenance and the control of a repair workshop are two aspects where the cost factor needs careful monitoring. It is here that costs can escalate, often unnoticed — for example through poor workmanship necessitating repeat repairs; wastage of consumable materials; loss or damage of tools through incorrect use or failure to return them to their proper place; through holding too many 'slow-moving parts and keeping spares for vehicles no longer operated (a common fault in many workshops); or perhaps through not stocking items which are repeatedly' required, necessitating the time and expense of sending a man and a van to buy items as required.
This latter fault reflects a lack of stock planning by the workshop foreman or storeman, who should watch such situations. The workshop foreman should try so far as possible to anticipate which vehicles are coming in for repair and maintenance (a set programme may well be in operation) and to anticipate what spare parts may be required, so that any not stocked can be obtained. This is not always possible but it can be achieved more frequently than some of those responsible would care to admit.
Control of the stores is important whether these are sufficiently large to justify a full-time storekeeper or whether just a few items are kept on a workshop shelf. Overstocking wastes valuable space, ties up capital and can lead to deterioration of the spares themselves. And often items are kept until it is too late to obtain credit by returning them.
Heavy losses can be incurred by inefficient arrangments for dispensing fuel and lubricants from bulk supplies. Accurate metering devices and reliable recording of issues to individual vehicles are necessary if wastage is to be kept to a minimum and vehicle cost records are to be maintained accurately.
Lost time The amount of money which can be wasted through poor control of workshop staff and poor planning of their workflow can soon be estimated by totting up the hours shown on job cards for productive work, deducting this from the total paid-for hours and multiplying the result by the. hourly rate.
Even an efficient worker who is able to keep busy will spend 25 per cent of his paid-for time away from the job. Take for example a fitter who is paid 80p an hour for a 45-hour week. This man will be paid for 2340 hours in the year, totalling £1872. However, he will probably have three weeks annual holiday (15 days paid at 8 hours, totalling 120 hours) and he will have six days off for bank holidays, another 48 hours. He will lose at least one hour per working day for paid tea and meal breaks, ie 239 hours. The total will be further increased by an average of 10 per cent of lost working time in the year between jobs and for putting on and taking off overalls, finding and replacing tools — over 180 hours making a total of perhaps 590 hours in the year at 80p per hour — or £472.
Cash flow The availability of cash is a particular problem which frequently besets the small operator. Unfortunately, haulage is a business in which most of the money is tied up in fixed assets, so cash is not always available to meet current liabilities. It is cash that pays bills and it is lack of ready cash that so often puts firms in trouble despite having capital assets.
When financing new vehicles it is worth remembering that it is not a good policy to tie up too much cash in fixed assets. These cannot be readily turned into working money and if the bank overdraft is at or near its limit there is probably no other means of getting ready cash for immediate needs and particularly wages. Such situations can be anticipated by carefully analysing all the various means of vehicle acquisition (ie outright purchase, bank loan, hire purchase, leasing, contract hire) and selecting the most suitable; and by timing the acquisition with an eye on cash demands, tax payments, wear and tear allowances and so on.
Utilization Before buying extra vehicles it is worth doing a small exercise to see if more vehicles are really needed or whether the existing fleet can be made to do more work. A simple formula for making a rough appraisal is to multiply the carrying capacity of the fleet by the total available working days in the year to compare this with the actual tonnage carried. The difference is the shortfall in maximum utilization.
Finally, on vehicle costing, it should be emphasized that costs can only be reduced if they are known and controlled. A figure of £1 wasted on costs is £1 lost on net profit; working on a net profit of five per cent, £1000 saved on costs in one year — and this is not too much to aim for — is equivalent to finding £20,000 extra revenue in that year. It is obviously easier to save on costs than it is to increase revenue by margins of this order.