7. Using the engineer's Crystal ball
Page 30
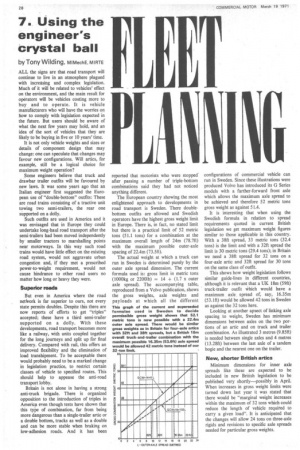
Page 31
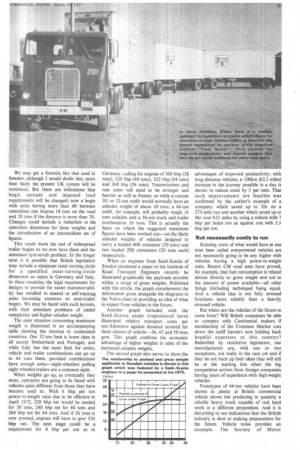
Page 32
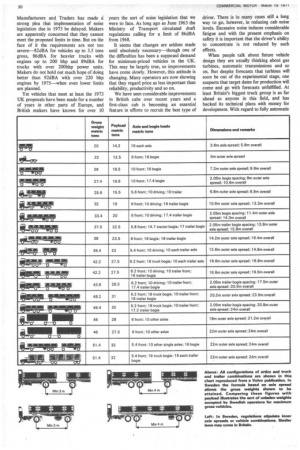
Page 33
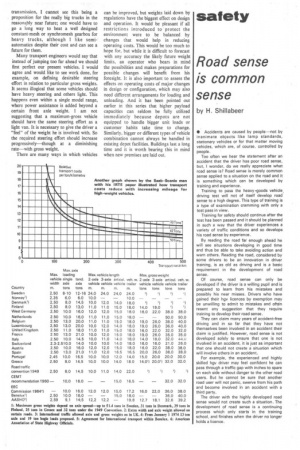
If you've noticed an error in this article please click here to report it so we can fix it.
by Tony Wilding, MIMechE, MIRTE
ALL the signs are that road transport will continue to live in an atmosphere plagued with increasing and complex legislation. Much of it will be related to vehicles' effect on the environment, and the main result for operators will be vehicles costing more to buy and to operate. It is vehicle manufacturers who will have the worries on how to comply with legislation expected in the future. But users should be aware of what the next few years may hold, and an idea of the sort of vehicles that they are likely to be buying in five or 10 years' time.
It is not only vehicle weights and sizes or details of component design that may change: one can speculate that changes may favour new configurations. Will artics, for example, still be a logical choice for maximum weight operation?
Some engineers believe that truck and drawbar trailer outfits will be favoured by new laws. It was some years ago that an Italian engineer first suggested the European use of "double-bottom" outfits: These are road trains consisting of a tractive unit towing two semi-trailers, the rear one supported on a dolly.
Such outfits are used in America and it was envisaged that in Europe they could undertake long-haul road transport after the semi-trailers had been moved independently by smaller tractors to marshalling points near motorways. In this way such road trains would have little effect on the existing road system, would not aggravate urban congestion and, if they met a prescribed power-to-weight requirement, would not cause hindrance to other road users no matter how long or heavy they were.
Superior roads But even in America where the road netivork is far superior to ours, not every state permits doubles. Despite this there are now reports of efforts to get "triples" accepted; these have a third semi-trailer supported on a dolly. With these developments, road transport becomes more like a railway, with units coupled together for the long journeys and split up ror final delivery. Compared with rail, this offers an improved flexibility and the elimination of load transhipment. To be acceptable there would probably need to be a marked change in legislation practice, to restrict certain classes of vehicle to specified routes. This should help to appease the anti-road transport lobby.
Britain is not alone in having a strong anti-truck brigade. There is organized opposition to the introduction of triples in America even though tests have shown that this type of combination, far from being more dangerous than a single-trailer artic or a double bottom, tracks as well as a double and can be more stable when braking on low-adhesion roads. And it has been
reported that motorists who were stopped. after passing a number of triple-bottom combinations said they had not noticed anything different.
The European country showing the most enlightened approach to developments in road transport is Sweden. There doublebottom outfits are allowed and Swedish operators have the highest gross weight limit in Europe. There is, in fact, no stated limit but there is a practical limit of 52 metric tons (51.1 tons) for a combination at the maximum overall length of 24m (78.7ft) with the maximum possible outer-axle spacing of 22.4m (73.5ft).
The actual weight at which a truck can run in Sweden is determined purely by the outer axle spread dimension. The current formula used is: gross limit in metric tons (1000kg or 22001b) = 14 + (1.7 x outer axle spread). The accompanying table, reproduced from a Volvo publication, shows the gross weights, axle weights and payloads at which all the different configurations of commercial vehicle can run in Sweden. Since these illustrations were produced Volvo has introduced its G Series models with a farther-forward front axle which allows the maximum axle spread to be achieved and therefore 52 metric tons gross weight as against 51.4.
It is interesting that when using the Swedish formula in relation to spread requirements quoted in current British legislation we get maximum weight figures similar to those applicable in this country. With a 38ft spread, 33 metric tons (32.4 tons) is the limit and with a 32ft spread the limit is 30 metric tons (29.4 tons); in Britain we need a 38ft spread for 32 tons on a four-axle artic and 32ft spread for 30 tons on the same class of outfit.
This shows how weight legislation follows similar guide-lines in different countries, although it is relevant that a UK 18m (59ft) truck-trailer outfit Which would have a maximum axle spread of, say, 16.35m (53.1ft) would be allowed 42 tons in Sweden as against the 32 tons here.
Looking at another apsect of linking axle spacing to weight, Sweden has minimum dimensions between axles on the two portions of an artic and on truck and trailer combination. As illustrated 3 metres (9.8511) is needed between single axles and 4 metres (13.28ft) between the last axle of a tandem bogie and the nearest one on the trailer.
New, shorter British artics Minimum dimensions for inner axle spreads like these are expected to be included in new British legislation to be published very shortly—possibly in April. When increases in gross weight limits were turned down last year it was stated that there would be "marginal weight increases within the maximum of 32 tons which could reduce the length of vehicle required to carry a given load". It is anticipated that the changes will allow 24 tons on three-axle rigids and revisions to specific axle spreads needed for particular gross weights. We may get a formula like that used in Sweden, although I would•doubt this; more than likely the present UK system will be continued. But there are indications that bogie spreads and imposed load requirements will be changed; now a bogie with axles having more than 4ft between centrelines can impose 18 tons on the road and 20 tons if the distance is more than 7ft. Changes could include a reduction in the centreline dimension for these weights and the introduction of an intermediate set of figures.
This could mark the end of widespread trailer bogies as we now have them and the attendant tyre-scrub problem. In the longer term it is possible that British legislation may include a minimum inner turning circle for a specified outer-turning-circle dimension as exists in Germany and Italy. In these countries the legal requirement for designs to provide for easier manoeuvrability has resulted in steered or self-tracking axles becoming common on semi-trailer bogies. We may be faced with such layouts, with their attendant problems of added complexity and higher unladen weight.
The poor situation concerning maximum weight is illustrated in an accompanying table showing the maxima in continental countries. Our 32-ton limit is lower than in all except Switzerland and Portugal; and while Italy has the same limit for artics, vehicle and trailer combinations can go up to 44 tons there, provided combinations have enough axles—eight-wheelers pulling eight-wheeled trailers are a common sight.
When weights go up, as eventually they must, operators are going to be faced with vehicles quite different from those they have become used to. With 6 bhp per ton power-to-weight ratio due to be effective in April 1972, 228 bhp net would be needed for 38 tons, 240 bhp net for 40 tons and 264 bhp net for 44 tons. And if 56 tons is ever granted, engines will have to give 336 bhp • net. The next stage could be a requirement for 8 bhp per ton as in Germany. calling for engines of 304 bhp (38 tons), 320 bhp (40 tons), 352 bhp (44 tons) and 368 bhp (56 tons). Transmissions and rear axles will need to be stronger and heavier as well as frames, so while a current 30or 32-ton outfit would normally have an unladen weight of about 10 tons, a 44-ton outfit, for example, will probably weigh 14 tons unladen and a 56-ton truck and trailer combination 16 tons. This is actually the basis on which the suggested maximum figures have been worked out—on the likely unladen weights of vehicles designed to carry a loaded 40ft container (30 tons) and two loaded 20ft containers (20 tons each) respectively.
When an engineer from Saab-Scania of Sweden presented a paper to the Institute of Road Transport Engineers recently he illustrated graphically the payloads possible within a range of gross weights. Published with this article, the graph complements the information given alongside the diagrams in the Volvo chart in providing an idea of what to expect from vehicles in the future.
Another graph included with the Saab-Scania paper (reproduced here) illustrated relative transport costs per ton /kilometre against distance covered for three classes of vehicle-36, 42 and 50 tons gcw. This graph confirms the economic advantage of higher weights in spite of the increased unladen weights.
The second graph also serves to show the advantages of improved productivity; with long-distance vehicles, a 100km (62.5 miles) increase in the journey possible in a day is shown to reduce costs by 5 per cent. That such improvements are feasible was confirmed by the author's example of a company which saved up to 2hr on a 373-mile run and another which saved up to 4hr over 621 miles by using a vehicle with 7 bhp per laden ton as against one with 5.5 bhp per ton.
Not necessarily costly to run Running costs of what would have at one time been called overpowered vehicles are not necessarily going to be any higher with vehicles having a high power-to-weight ratio. Recent CM road tests have proved, for example, that fuel consumption is related almost directly to gross weight and not to the amount of power available—all other things (including technique) being equal. And a vehicle that is not fully stressed functions more reliably than a heavily stressed vehicle.
But where are the vehicles of the future to come from? Will British companies be able to compete with Continental makers if membership of the Common Market cuts down the tariff barriers now holding back hopeful exporters to this country? Bedevilled by restrictive legislation, our manufacturers are, with one or two exceptions, not really in the race yet and if they do not buck up their ideas they will still be at the starting line when the big competition arrives from foreign companies having years of experience with high-weight vehicles.
Prototypes of 44-ton vehicles have been shown in plenty at British commercial vehicle shows but producing in quantity a reliable heavy truck capable of real hard work is a different proposition. And it is disturbing to see indications that the British industry is slow at making preparations for the future. Vehicle noise provides an example. The Society of Motor Manufacturers and Traders has made i strong plea that implementation of noise legislation due in 1973 be delayed. Makers are apparently concerned that they cannot meet the proposed limits in time. But on the face of it the requirements are not too severe-82dBA for vehicles up to 3.5 tons gross, 86dBA for heavier trucks with engines up to 200 bhp and 89dBA for trucks with over 200bhp power units. Makers do not hold out much hope of doing better than 92dBA with over 220 bhp engines by 1975-when even lower limits are planned.
Yet vehicles that meet at least the 1973 UK proposals have been made for a number of years in other parts of Europe, and British makers have known for over 10 years the sort of noise legislation that we were to face. As long ago as June 1963 the Ministry of Transport circulated draft regulations calling for a limit of 86dBA from 1968.
It seems that changes are seldom made until absolutely necessary-though one of the difficulties has been a supposed demand for minimum-priced vehicles in the UK. This may be largely true, so improvements have come slowly. However, this attitude is changing. Many operators are now showing that they regard price as less important than reliability, productivity and so on.
We have seen considerable improvements in British cabs over recent years and a first-class cab is becoming an essential feature in efforts to recruit the best type of driver. There is in many cases still a long way to go, however, in reducing cab noise levels. Excessive noise induces considerable fatigue and with the present emphasis on safety it is important that the driver's ability to concentrate is not reduced by such effects.
When people talk about future vehicle design they are usually thinking about gas turbines, automatic transmissions and so on. But despite forecasts that turbines will soon be out of the experimental stage, one suspects that target dates for production will come and go with forecasts unfulfilled. At least Britain's biggest truck group is as far ahead as anyone in this field, and has backed its technical plans with money for development. With regard to fully automatic transmission, I cannot see this being a proposition for the really big trucks in the reasonably near future; one would have to go a long way to beat a well designed constant-mesh or synchromesh gearbox for heavy trucks, although I like semiautomatics despite their cost and can see a future for them.
Many transport engineers would say that instead of juinping too far ahead we should first perfect our present vehicles. I would agree and would like to see work done, for example, on defining desirable steering effort in relation to particular gross weights. It seems illogical that some vehicles should have heavy steering and others light. This happens even within a single model range, where power assistance is added beyond a certain front axle weight. I am not suggesting that a maximum-gross vehicle should have the same steering effort as a light van. It is necessary to give the driver a "feel" of the weight he is involved with. So the required steering effort should increase progressively-though at a diminishing rate-with gross weight.
There are many ways in which vehicles can be improved, but weights laid down by regulations have the biggest effect on design and operation. It would be pleasant if all restrictions introduced to protect the environment were to be balanced by changes that would help in reducing operating costs. This would be too much to hope for, but while it is difficult to forecast with any accuracy the likely future weight limits, an operator who bears in mind the possibilities and makes preparations for possible changes will benefit from his foresight. It is also important to assess the effects on operating costs of major changes in design or configuration, which may also need different arrangements for loading and unloading. And it has been pointed out earlier in this series that higher payload capacities can seldom be fully utilized immediately because depots are not equipped to handle bigger unit loads or customer habits take time to change. Similarly, bigger or different types of vehicle combination cannot always be handled in existing depot facilities. Buildings last a long time and it is worth bearing this in mind when new premises are laid out.