MORE PUFF LESS BLOWOUTS
Page 44
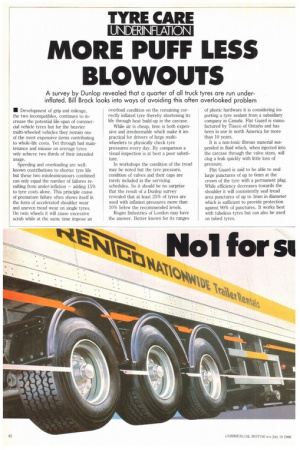
Page 45
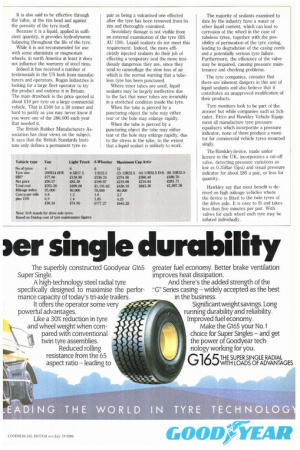
If you've noticed an error in this article please click here to report it so we can fix it.
A survey by Dunlop revealed that a quarter of all truck tyres are run underinflated. Bill Brock looks into ways of avoiding this often overlooked problem
• Development of grip and mileage, the two incompatibles, continues to increase the potential life-span of commercial vehicle tyres but for the heavier multi-wheeled vehicles they remain one of the most expensive items contributing to whole-life costs. Yet through bad maintenance and misuse on average tyres only achieve two thirds of their intended usage.
Speeding and overloading are wellknown contributions to shorter tyre life but these two misdeameanours combined can only equal the number of failures resulting from under-inflation — adding 15% to tyre costs alone. This principle cause of premature failure often shows itself in the form of accelerated shoulder wear and uneven tread wear on single tyres. On twin wheels it will cause excessive scrub while at the same time impose an overload condition on the remaining correctly inflated tyre thereby shortening its life through heat build-up in the carcase.
While air is cheap, time is both expensive and irredeemable which make it impractical for drivers of large multiwheelers to physically check tyre pressures every day. By comparison a visual inspection is at best a poor substitute.
In workshops the condition of the tread may be noted but the tyre pressure, condition of valves and their caps are rarely included in the servicing
schedules. So it should be no surprise that the result of a Dunlop survey revealed that at least 25% of tyres are used with inflation pressures more than 10% below the recommended levels.
Rogan Industries of London may have the answer. Better known for its ranges of plastic hardware it is considering importing a tyre sealant from a subsidiary company in Canada. Flat Guard is manufactured by Tiseco of Ontario and has been in use in north America for more than 10 years.
It is a non-toxic fibrous material suspended in fluid which, when injected into the carcase through the valve stem, will clog a leak quickly with little loss of pressure.
Flat Guard is said to be able to seal large punctures of up to 6rnm at the crown of the tyre with a permanent plug. While efficiency decreases towards the shoulder it will consistently seal tread area punctures of up to 3mm in diameter which is sufficient to provide protection against 90% of punctures. It works best with tubeless tyres but can also be used on tubed tyres. It is also said to be effective through the valve, at the rim bead and against the porosity of the tyre itself.
Because it is a liquid, applied in sufficient quantity, it provides hydrodynamic balancing throughout the life of the tyre.
While it is not recommended for use with some aluminium or magnesium wheels, in north America at least it does not influence the warranty of steel rims.
Indeed it has received a number of testimonials in the US both from manufacturers and operators. Rogan Industries is looking for a large fleet operator to try the product and endorse it in Britain. The main drawback is the price quoted at about £10 per tyre on a large commercial vehicle. That is £160 for a 38 tonner and hard to justify as you may never know if you were one of the 280,000 each year that needed it.
The British Rubber Manufacturers Association has clear views on the subject. It says that the British Standards Institute only defines a permanent tyre re
pair as being a vulcanised one effected after the tyre has been removed from its rim and thoroughly examined.
Secondary damage is not visible from an external examination of the tyre (BS AU 159). Liquid sealants do not meet this requirement. Indeed, the more efficiently injected sealants do their job of effecting a temporary seal the more insidiously dangerous they are, since they tend to camouflage the slow loss of air which is the normal warning that a tubeless tyre has been punctured.
Where inner tubes are used, liquid sealants may be largely ineffective due to the fact that inner tubes are invariably in a stretched condition inside the tyre.
When the tube is pierced by a puncturing object the tube may either tear or the hole may enlarge rapidly.
When the tube is pierced by a puncturing object the tube may either tear or the hole may enlarge rapidly, due to the stress in the tube, to the extent that a liquid sealant is unlikely to work. The majority of sealants examined to date by the industry have a water or other liquid content, which can lead to corrosion of the wheel in the case of tubeless tyres, together with the possibility of permeation of the tyre casing, leading to degradation of the casing cords and a potentially serious tyre failure. Furthermore, the efficiency of the valve may be impaired, causing pressure maintenance and checking problems.
The tyre companies, consider that there are inherent dangers in this use of liquid sealants and also believe that it constitutes an unapproved modification of their products.
Tyre monitors look to be part of the answer but while companies such as Schrader, Ettco and Hawkley Vehicle Equipment all manufacture tyre pressure equalisers which incorporate a pressure indicator, none of them produce a monitor for commercial vehicle tyres mounted singly.
The Hawkley device, made under licence in the UK, incorporates a cut-off valve, detecting pressure variations as low as 0.35Bar (5psi) and visual pressure indicator for about £85 a pair, or less for quantity.
Hawkley say that most benefit is derived on high mileage vehicles where the device is fitted to the twin tyres of the drive axle. It is easy to fit and takes less than five minutes per pair. With valves for each wheel each tyre may be inflated individually.