TREADING NEW GROUND
Page 42
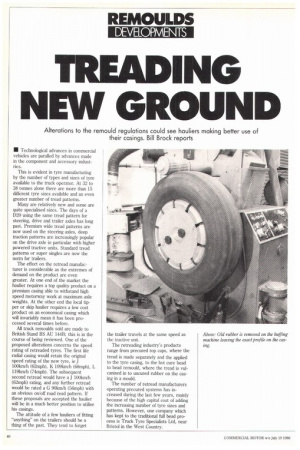
Page 43
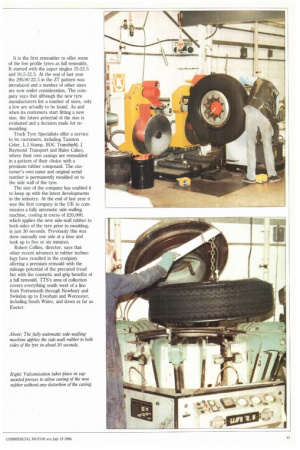
If you've noticed an error in this article please click here to report it so we can fix it.
Alterations to the remould regulations could see hauliers making better use of their casings. Bill Brock reports
• Technological advances in commercial vehicles are paralled by advances made in the component and accessory industries.
This is evident in tyre manufacturing by the number of types and sizes of tyre available to the truck operator. At 32 to 38 tonnes alone there are more than 15 different tyre sizes available and an even greater number of tread patterns.
Many are relatively new and some are quite specialised sizes. The days of a D20 using the same tread pattern for steering, drive and trailer axles has long past. Premium wide tread patterns are now used on the steering axles, deep traction patterns are increasingly popular on the drive axle in particular with higher powered tractive units. Standard tread patterns or super singles are now the norm for trailers.
The effect on the retread manufacturer is considerable as the extremes of demand on the product are even greater. At one end of the market the haulier requires a top quality product on a premium casing able to withstand high speed motorway work at maximum axle weights. At the other end the local tipper or skip haulier requires a low cost product on an economical casing which will invariably mean it has been processed several times before.
All truck remoulds sold are made to British Stand BS AU 144B; this is in the course of being reviewed. One of the proposed alterations concerns the speed rating of retreaded tyres. The first life radial casing would retain the original speed rating of the new tyre, ie J 100km/h (62mph), K 109km/h (68mph), L 1191u-n/h (74mph). The subsequent second retread would have a J 100Iun/h (62mph) rating, and any further retread would be rated a G 90km/h (56mph) with an obvious on/off road read pattern. If these proposals are accepted the haulier will be in a much better position to utilise his casings.
The attitude of a few hauliers of fitting "anything" on the trailers should be a thing of the past. They tend to forget the trailer travels at the same speed as the tractive unit.
The retreading industry's products range from precured top caps, where the tread is made separately and the applied to the tyre casing, to the hot cure bead to bead remould, where the tread is vulcanised in to uncured rubber on the casing in a mould.
The number of retread manufacturers operating precured systems has increased during the last few years, mainly because of the high capital cost of adding the increasing number of tyre sizes and patterns. However, one company which has kept to the traditional full bead process is Truck Tyre Specialists Ltd, near Bristol in the West Country. It is the first remoulder to offer some of the low profile tyres as full remoulds. It started with the super singles 15-22.5 and 16.5-22.5. At the end of last year the 295/80-22.5 in the ZT pattern was introduced and a number of other sizes are now under consideration. The company says that although the new tyre manufacturers list a number of sizes, only a few are actually to be found, As and when its customers start fitting a new size, the future potential of the size is evaluated and a decision made for remoulding.
Truck Tyre Specialists offer a service to its customers, including Taunton Cider, L J Stamp, BOC Transhield, J Raymond Transport and Hales Cakes, where their own casings are remoulded in a pattern of their choice with a premium rubber compound. The customer's own name and original serial number is permanently moulded on to the side wall of the tyre.
The size of the company has enabled it to keep up with the latest developments in the industry. At the end of last year it was the first company in the UK to commission a fully automatic side-walling machine, costing in exess of £20,000, which applies the new side-wall rubber to both sides of the tyre prior to moulding, in just 30 seconds. Previously this was done manually one side at a time and took up to five or six minutes.
Robert Collins, director, says that other recent advances in rubber technology have resulted in the company offering a premium remould with the mileage potential of the precured tread but with the cosmetic and grip benefits of a full remould. TTS's area of collection covers everything south west of a line from Portsmouth through Newbury and Swindon up to Evesham and Worcester, including South Wales, and down as far as Exeter.