HI TECH TYRES
Page 32
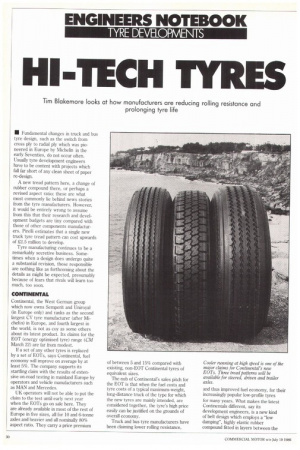
Page 33
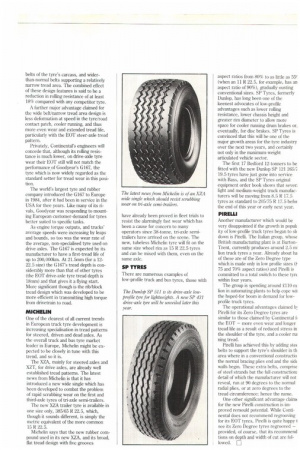
If you've noticed an error in this article please click here to report it so we can fix it.
Tim Blakemore looks at how manufacturers are reducing rolling resistance and prolonging tyre life
• Fundamental changes in truck and bus tyre design, such as the switch from cross ply to radial ply which was pioneered in Europe by Michelin in the early Seventies, do not occur often. Usually tyre development engineers have to be content with projects which fall far short of any clean sheet of paper re-design.
A new tread pattern here, a change of rubber compound there, or perhaps a revised aspect ratio; these are what most commonly lie behind news stories from the tyre manufacturers. However, it would be entirely wrong to assume from this that their research and development budgets are tiny compared with those of other components manufacturers. Pirelli estimates that a single new truck tyre tread pattern can cost upwards of £2.5 million to develop.
Tyre manufacturing continues to be a remarkably secretive business. Sometimes when a design does undergo quite a substantial revision, those responsible are nothing like as forthcoming about the details as might be expected, presumably because of fears that rivals will learn too much, too soon.
CONTINENTAL
Continental, the West German group which now owns Semperit and Uniroyal (in Europe only) and ranks as the second largest CV tyre manufacturer (after Michelin) in Europe, and fourth largest in the world, is not as coy as some others about its latest product. Its claims for the EOT (energy optimised tyre) range (CM March 22) are far from modest.
If a set of any other tyres is replaced by a set of EOTs, says Continental, fuel economy will improve on average by at least 5%. The company supports its startling claim with the results of extensive on-road testing in mainland Europe by operators and vehicle manufacturers such as MAN and Mercedes.
UK operators will not be able to put the claim to the test until early next year when the EOTs go on sale here. They are already available in most of the rest of Europe in five sizes, all for 10 and 6-tonne axles and heavier and all nominally 80% aspect ratio. They carry a price premium of between 5 and 15% compared with existing, non-EOT Continental tyres of equivalent sizes.
The nub of Continental's sales pitch for the EOT is that when the fuel costs and tyre costs of a typical maximum-weight, long-distance truck of the type for which the new tyres are mainly intended, are considered together, the tyre's high price easily can be justified on the grounds of overall economy.
Truck and bus tyre manufacturers have been claiming lower rolling resistance, and thus improved fuel economy, for their increasingly popular low-profile tyres for many years. What makes the latest Continentals different, say its development engineers, is a new kind of belt design which employs a "low damping", highly elastic rubber compound fitted in layers between the belts of the tyre's carcass, and widerthan-normal belts supporting a relatively narrow tread area. The combined effect of these design features is said to be a reduction in rolling resistance of at least 18% compared with any competitor tyre.
A further major advantage claimed for the wide belt/narrow tread area design is less deformation at speed in the tyre/road contact patch, cooler running, and thus more even wear and extended tread life, particularly with the EOT steer-axle tread pattern.
Privately, Continental's engineers will concede that, although its rolling resistance is much lower, on drive-axle tyre wear their EOT still will not match the performance of Goodyear's G167, the tyre which is now widely regarded as the standard setter for tread wear in this position.
The world's largest tyre and rubber company introduced the G167 to Europe in 1984, after it had been in service in the USA for thee years. Like many of its rivals, Goodyear was responding to mounting European customer-demand for tyres better suited to specific tasks.
As engine torque outputs, and trucks' average speeds were increasing by leaps and bounds, so too was the wear rate of the average, non-specialised tyre used on drive axles. The G167 is expected by its manufacturer to have a first-tread life of up to 200,000km. At 21.5mm (for a 1222.5 size) the G167's tread depth is considerably more than that of other tyres (the EOT drive-axle tyre tread depth is 18mm) and that gives it a flying start. More significant though is the rib/block tread design which was developed to be more efficient in transmitting high torque from drivetrain to road.
MICHELIN
One of the clearest of all current trends in European truck tyre development is increasing specialisation in tread patterns for steered, driven and dead axles. As the overall truck and bus tyre market leader in Europe, Michelin might be expected to be closely in tune with this trend, and so it is.
The VIA, mainly for steered axles and XZT, for drive axles, are already well established tread patterns. The latest news from Michelin is that it has introduced a new wide single which has been developed to combat the problem of rapid scrubbing wear on the first and third-axle tyres of tri-axle semi-trailers. The new XZA trailer tyre is available in one size only, 385/65 R 22.5, which, though it sounds different, is simply the metric equivalent of the more common 15 R 22.5.
Michelin says that the new rubber compound used in its new XZA, and its broad, flat tread design with five grooves have already been proved in fleet trials to resist the alarmingly fast wear which has been a cause for concern to many operators since 38-tonne, tri-axle semitrailers have arrived on the scene. The new, tubeless Michelin tyre will fit on the same size wheel rim as 15 R 22.5 tyres and can be mixed with them, even on the same axle.
SP TYRES
There are numerous examples of low-profile truck and bus tyres, those with aspect ratios from 80% to as little as 55' (when an 11 R 22.5, for example, has an aspect ratio of 90%), gradually ousting conventional sizes. SP Tyres, formerly Dunlop. has long been one of the keenest advocates of low-profile advantages such as lower rolling resistance, lower chassis height and greater rim diameter to allow more space for cooler running drum brakes or, eventually, for disc brakes. SP Tyres is convinced that this will be one of the major growth areas for the tyre industry over the next two years, and certainly not only in the maximum-weight articulated vehicle sector.
The first 17 Bedford 12-tonners to be fitted with the new Dunlop SP 121 265/'; 19.5 tyres have just gone into service with Bass, and the SP Tyres original equipment order book shows that seven light and medium-weight truck manufacturers will be moving from 8.5 R 17.5 tyres as standard to 205/75 R 17.5 befoi the end of this year or early next year.
PIRELLI
Another manufacturer which would be very disappointed if the growth in popuk ity of low-profile truck tyres began to sic down is Pirelli. The Italian group, whose British manufacturing plant is at Burton-. Trent, currently produces around 2.5 mi lion truck tyres a year. Already about ha of these are of the Zero Degree type which is made only in low profile sizes (F 75 and 70% aspect ratios) and Pirelli is committed to a total switch to these tyrt within four years.
The group is spending around £110 in lion in automating plants to help cope wit the hoped-for boom in demand for lowprofile truck tyres.
The operational advantages claimed!): Pirelli for its Zero Degree tyres are similar to those claimed by Continental f4 the EOT — more even wear and longer tread life as a result of reduced stress in the shoulder of the tyre, and a cooler rui ning tread.
Pirelli has achieved this by adding stet belts to support the tyre's shoulder in th area where in a conventional constructio the normal bracing plies end and the sick walls begin. These extra belts, comprise of steel strands but the full construction detail of which the manufacturer will not reveal, run at 90 degrees to the normal radial plies, or at zero degrees to the tread circumference; hence the name.
One other significant advantage claimt for the new Pirelli construction is improved remould potential. While Continental does not recommend regrooving for its EOT tyres, Pirelli is quite happy see its Zero Degree tyres regrooved — provided, of course, that its recommend tions on depth and width of cut are followed.