Fluid drive for fans and alternators
Page 54
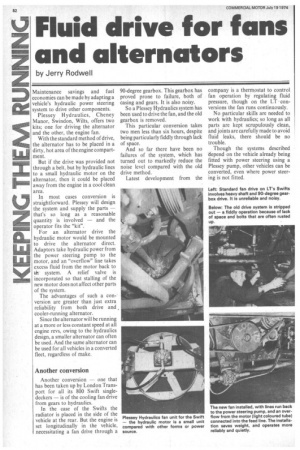
If you've noticed an error in this article please click here to report it so we can fix it.
by Jerry Rodwell
Maintenance savings and fuel economies can be made by adapting a vehicle's hydraulic power steering system to drive other components.
Plessey Hydraulics, Cheney Manor, Swindon, Wilts, offers two kits; one for driving the alternator and the other, the engine fan.
With the standard method of drive, the alternator has to be placed in a dirty, hot area of the engine compartment.
But if the drive was provided not through a belt, but by hydraulic lines to a small hydraulic motor on the alternator, then it could be placed away from the engine in a cool clean area.
In most cases conversion is straightforward. Plessey will design the system and supply the parts that's so long as a reasonable quantity is involved — and the operator fits the "kit".
For an alternator drive the hydraulic motor would be mounted to drive the alternator direct. Adaptors take hydraulic power from the power steering pump to the motor, and an "overflow" line takes excess fluid from the motor back to th system. A relief valve is incorporated so that stalling of the new motor does not affect other parts of the system.
The advantages of such a conversion are greater than just extra reliability from both drive and cooler-running alternator.
Since the alternator will be running at a more or less constant speed at all engine revs, owing to the hydraulics design, a smaller alternator can often be used. And the same alternator can be used for all vehicles in a converted fleet, regardless of make.
Another conversion
Another conversion — one that has been taken up by London Transport for all its 800 Swift singledeckers — is of the cooling fan drive from gears to hydraulics.
In the case of the Swifts the radiator is placed in the side of the vehicle at the rear. But the engine is set longitudinally in the vehicle, necessitating a fan drive through a 90-degree gearbox. This gearbox has proved prone to failure, both of casing and gears. It is also noisy.
So a Plessey Hydraulics system has been used to drive the fan, and the old gearbox is removed.
This particular conversion takes two men less than six hours, despite being particularly fiddly through lack of space.
And so far there have been no failures of the system, which has turned out to markedly reduce the noise level compared with the old drive method.
Latest development from the company is a thermostat to control fan operation by regulating fluid pressure, though on the LT conversions the fan runs continuously.
No particular skills are needed to work with hydraulics; so long as all parts are kept scrupulously clean, and joints are carefully made to avoid fluid leaks, there should be no trouble.
Though the systems described depend on the vehicle already being fitted with power steering using a Plessey pump, other vehicles can be converted, even where power steering is not fitted.