let managers Involved in trailer maintenance —it's the only way'
Page 46
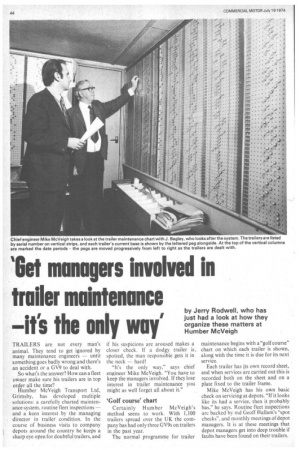
Page 47
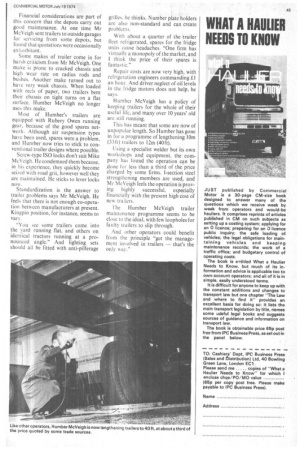
If you've noticed an error in this article please click here to report it so we can fix it.
by Jerry Rodwell, who has just had a look at how they organize these matters at Humber McVeigh
TRAILERS are not every man's animal. They tend to get ignored by many maintenance engineers — until something goes badly wrong and there's an accident or a GV9 to deal with.
So what's the answer? How can a fleet owner make sure his trailers are in top order all the time?
Humber McVeigh Transport Ltd, Grimsby, has developed multiple solutions: a carefully charted maintenance system, routine fleet inspections — and a keen interest by the managing director in trailer condition. In the course of business visits to company depots around the country he keeps a sharp eye open for doubtful trailers, and if his suspicions are aroused makes a closer check. If a dodgy trailer is spotted, the man responsible gets it in the neck — hard!
"It's the only way," says chief engineer Mike McVeigh. "You have to keep the managers involved. If they lose interest in trailer maintenance you might as well forget all about it."
'Golf course' chart
Certainly Humber McVeigh's method seens to work. With 1,100 trailers spread over the UK the company has had only three GV9s on trailers in the past year.
The normal programme for trailer maintenance begins with a "golf course" chart on which each trailer is shown, along with the time it is due for its next service.
Each trailer has its own record sheet, and when services are carried out this is recorded both on the sheet and on a plate fixed to the trailer frame.
Mike McVeigh has his own basic check on servicing at depots. "If it looks like its had a service, then it probably has," he says. Routine fleet inspections are backed by md Geoff Hallam's "spot checks", and monthly meetings of depot managers. It is at these meetings that depot managers get into deep trouble if faults have been found on their trailers. Financial considerations are part of this concern that the depots carry out good maintenance. At one time Mr McVeigh sent trailers to outside garages for servicing from some depots, but found that quotations were occasionally exhorhitant.
Some makes of trailer come in for harsh criticism from Mr McVeigh. One make is prone to cracked chassis and high wear rate on radius rods and bushes. Another make turned out to ha‘e very weak chassis. When loaded with reels of paper, two trailers bent their chassis on tight turns on a flat surface. Humber McVeigh no longer uses this make.
Most of Humber's trailers are equipped with Rubery Owen running gear, because of the good spares network. Although air suspension types have been used, spares were a Problem, and !lumber now tries to stick to conventional trailer designs where possible.
Screw-type ISO locks don't suit Mike McVeigh. He condemned them because, in his experience, they quickly become sei/ed with road grit, however well they are maintained. He sticks to lever locks .now.
Standardization is the answer to trailer problems says Mr McVeigh. He feels that there is not enough co-operation between manufacturers at present. Kingpin position, for instance, seems to vary.
"You see some trailers come into the yard running flat, and others on identical tractors running at a pronounced angle." And lighting sets should all be fitted with anti-pilferage grilles, he thinks„ Number plate holders are also non-standard and can create Pr oblems.
With about a quarter of the trailer fleet refrigerated, spares for the fridge units cause headaches. "One firm has virtually a monopoly of the market, and I think the price of their spares is fantastic."
Repair costs are now very high, with refrigeration engineers commanding 1 an hour. And driver neglect of oil levels in the fridge motors does not help, he says.
Humber McVeigh has a policy of keeping trailers for the whole of their useful life, and many over 10 years' old are still running.
This has meant that some are now of unpopular length. So Humber has gone in for a programme of lengthening 10m (33 ft) trailers to 12m (40 ft).
Using a specialist welder but its own workshops and equipment, the company has found the operation can be .done for less than a third of the price charged by some firms. l-section steel strengthening members are used, and Mr McVeigh feels the operation is proving highly successful, especially financially with the present high cost of new trailers.
.1-he Humber McVeigh trailer maintenance programme seems to be close to the ideal, with few loopholes for faulty trailers to slip through.
And other operators could benefit from the principle "get the management involved in trailers -that's the only way."