SOME fleet engineers may be forgiven for believing that the
Page 50
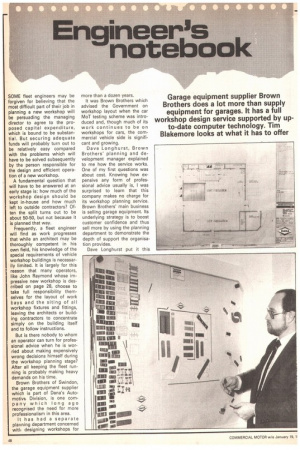
Page 53
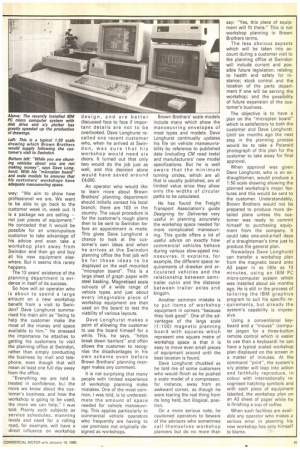
If you've noticed an error in this article please click here to report it so we can fix it.
most difficult part of their job in planning a new workshop will be persuading the managing director to agree to the proposed capital expenditure, which is bound to be substantial. But securing adequate funds will probably turn out to be relatively easy compared with the problems which will have to be solved subsequently by the person responsible for the design and efficient operation of a new workshop.
A fundamental question that will have to be answered at an early stage is: how much of the workshop design should be kept in-house and how much left to outside contractors? Often the split turns out to be about 50-50, but not because it is planned that way.
Frequently, a fleet engineer will find as work progresses that while an architect may be thoroughly competent in his own field, his knowledge of the special requirements of vehicle workshop buildings is necessarily limited. It is largely for this reason that many operators, like John Raymond whose impressive new workshop is described on page 28, choose to take full responsibility themselves for the layout of work bays and the siting of all workshop fixtures and fittings, leaving the architects or building contractors to concentrate simply on the building itself and to follow instructions.
But is there nobody to whom an operator can turn for professional advice when he is worried about making expensively wrong decisions himself during the workshop planning stage? After all keeping the fleet running is probably making heavy demands on his time.
Brown Brothers of Swindon, the garage equipment supplier which is part of Dana's Automotivb Division, is one company which long ago recognised the need for more professionalism in this area.
It has had a separate planning department concerned with designing workshops for more than a dozen years.
It was Brown Brothers which advised the Government on workshop layout when the car MoT testing scheme was introduced and, though much of its work continues to be on workshops for cars, the commercial vehicle side is significant and growing.
Dave Longhurst, Brown Brothers' planning and development manager explained to me how the service works. One of my first questions was about cost. Knowing how expensive any form of professional advice usually is, I was surprised to learn that this company makes no charge for its workshop planning service. Brown Brothers' main business is selling garage equipment. Its underlying strategy is to boost customer confidence and thus sell more by using the planning department to demonstrate the depth of support the organisation provides.
Dave Lcmghurst put it this
way: -We aim to show how professional we are. We want to be able to go back to the customer week in, week out. It is a package we are selling not just pieces of equipment." He conceded that it would be possible for an unscrupulous customer to take advantage of his advice and even take a workshop plan away from Swindon and then go and buy all his new equipment elsewhere. But it seems this rarely happens.
The 13 years' existence of the planning department is evidence in itself of its success.
So how will an operator who is about to spend a large amount on a new workshop benefit from a visit to Swindon? Dave Longhurst summarised his main aim as "being to help the customer make the most of the money and space available to him." He stressed the importance he attaches to getting his customers to visit the planning office at Swindon, rather than simply conducting the business by mail and telephone, even though that will mean at least one full day away from the office.
"Everything we are told is treated in confidence, bc"... the more we know about the customer's business, and how the workshop is going to be used, the more we can help," I was told. Plainly such subjects as service schedules, manning levels and need for a rolling road, for example, will have a direct influence on workshop
design, and are better discussed face to face if important details are not to be overlooked. Dave Longhurst recalled one recent customer who, when he arrived at Swindon, was sure that his workshop would need six doors. It turned out that only two would do the job just as well, and this decision alone would have saved around £4,000.
An operator who would like to learn more about Brown Brothers' planning department should initially contact his local branch; there are 103 in the country. The usual procedure is for the customer's rough plans then to be sent to Swindon before an appointment is made. This gives Dave Longhurst a chance to look at the customer's own ideas and when he arrives at the Swindon planning office the first job will be for these ideas to be displayed on the wall mounted "microplan board". This is a large sheet of graph paper with steel backing. Magnetised scale cut-outs of a wide range of vehicle types and just about every imaginable piece of workshop equipment are then used on the board to test the viability of various layouts.
Dave Longhurst makes a point of allowing the customer to use the board himself for a while. This, he says, "helps break down barriers" and often allows the customer to recognise the disadvantages in his own scheme even before Brown Brothers' planning manager makes any comment.
It is not surprising that many people with limited experience of workshop planning make mistakes. One of the most common, I was told, is to underestimate the amount of space needed for vehicle manoeuvring. This applies particularly to commercial vehicle operators who frequently are having to use premises not originally designed as workshops. Brown Brothers' scale models include many which show the manoeuvring envelopes of most types and models. Dave Longhurst continually updates his file on vehicle manoeuvrability by reference to published data (including CM road tests) and manufacturers' new model specifications. But he is well aware that the minimum turning circles, which are all that is usually published, are of limited value since they allow only the widths of circular paths to be calculated.
He has found the Freight Transport Association's guide Designing for Deliveries very useful in planning accurately the workshop space needed for more complicated manoeuvring. This guide offers a lot of useful advice on exactly how commercial vehicles behave during various slow-speed manoeuvres. It explains, for example, the different space requirements of drawbar and articulated vehicles and the relationship between semitrailer cut-in and the distance between trailer axles and kingpin.
Another common mistake is to put items of workshop equipment in corners "because they look good". One of the advantages of the large scale (1:1 00) magnetic planning board with squares which represent one square metre of workshop space is that it is easy to move even small pieces of equipment around until the best location is found.
Dave Longhurst chuckled as he told me of some customers who would flinch as he pushed a scale model of a compressor, for instance, away from an awkward corner, as though he were tearing the real thing from its long held, but illogical, position.
On a more serious note, he cautioned operators to beware of the advisors who sometimes call themselves workshop planners but do no more than say: "Yes, this piece of equipment will fit there." This is not workshop planning in Brown Brothers terms.
The less obvious aspects which will be taken into ac count during a customer visit to the planning office at Swindon will include current and pos sible future legislation, relating to health and safety for instance; stock control and the location of the parts department if one will be serving the workshop; and the possibility of future expansion of the customer's business.
The objective is to have a plan on the "microplan board" which is satisfactory to both the customer and Dave Longhurst. Until' six months ago the next step in the planning process would be to take a Polaroid photograph of this plan for the customer to take away for final approval.
When approval was given Dave Longhurst, who is an exdraughtsman, would produce a 1:50 scale drawing showing the planned workshop's major features and this would be sent to the customer. Understandably, Brown Brothers would not be prepared to produce more detailed plans unless the customer was ready to commit himself to purchasing equipment from the company. It could take one-and-a-half days of a draughtsman's time just to produce the general plan.
Nowadays Dave Longhurst can transfer a workshop plan from the magnetic board onto A3 paper in as little as 10 minutes, using an IBM PC micro-computer system which was installed about six months ago. He is still in the process of tailoring the IBM graphics program to suit his specific requirements, but already the system's capability is impressive.
Using a conventional keyboard and a "mouse" (computer jargon for a three-button remote control which is easier to use than a keyboard) he can have a typical scaled workshop plan displayed on the screen in a matter of minutes. At the command "print", the system's x/y plotter will leap into action and faithfully reproduce, in colour with internationally recognised hatching symbols and with each piece of equipment labelled, the workshop plan on an A3 sheet of paper while he is finishing a cup of coffee.
When such facilities are available any operator who makes a serious error in planning his new workshop has only himself to blame.