Safety measures: (10) Need for accuracy
Page 51
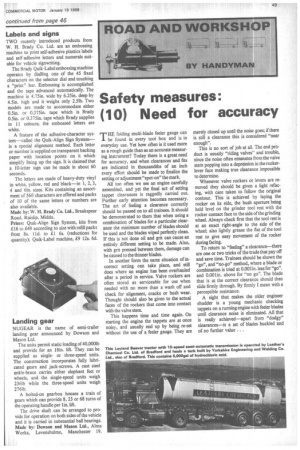
If you've noticed an error in this article please click here to report it so we can fix it.
rr HE folding multi-blade feeler gauge can be found in every tool box and is in everyday use. Yet how often is it used more as a rough guide than as an accurate measuring instrument? Today there is a great need for accuracy, and when clearances and fits are indicated in thousandths of an inch every effort should be made to finalize the setting or adjustment "spot-on" the mark.
All too often we see an engine carefully assembled, and yet the final act of setting tappet clearances is raggedly carried out. Further early attention becomes necessary. The art of feeling a clearance correctly should be passed on to all trainees. It should be demonstrated to them that when using a combination of blades for a particular clearance the minimum number of blades should be used and the blades wiped perfectly clean. If this is not done oil and grit can cause an entirely different setting to be made. Also, with grit pressed between them, damage can be caused to the thinner blades.
In another form the same situation of incorrect setting can take place, and still does where an engine has been overhauled after a period in service. Valve rockers are often stored as serviceable for use when needed with no more than a wash off and check for alignment, cracks or bush wear. Thought should also be given to the actual faces of the rockers that come into contact with the valve stem.
This happens time and time again. On starting the engine the tappets are at once noisy, and usually end up by being re-set without the use of a feeler gauge. They are merely closed up until the noise goes; if there is still a clearance this is considered "near enough".
This is no sort of job at all. The end product is usually "riding valves" and trouble, since the noise often emanates from the valve stem popping into a depression in the rockerlever face making true clearance impossible to determine.
Whenever valve rockers or levers are removed they should be given a light refacing, with care taken to follow the original contour. This is achieved by laying the rocker on its side, the bush aperture being held level on the grinder tool rest with the rocker contact face to the side of the grinding wheel. Always check first that the tool rest is at an exact right-angle to the side of the wheel; also lightly grease the flat of the tool rest to give easy movement of the rocker during facing.
To return to "feeling" a clearance—there are one or two tricks of the trade that pay off and save time. Trainees should be shown the "go", and "no-go" method, where a blade or combination is tried at 0.001in. less for "go". and 0.001in. above for "no go". The blade that is at the correct clearance should then slide firmly through. By firmly I mean with a perceptible resistance.
A sight that makes the older engineer shudder is a young mechanic checking tappets on a running engine with feeler blades until clearance noise is eliminated. All that is really achieved—apart from "dodgy" clearances—is a set of blades buckled and of no further value . .