Surface treated Metals Find New Applications
Page 34
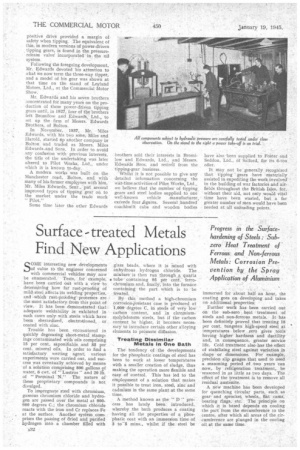
Page 37
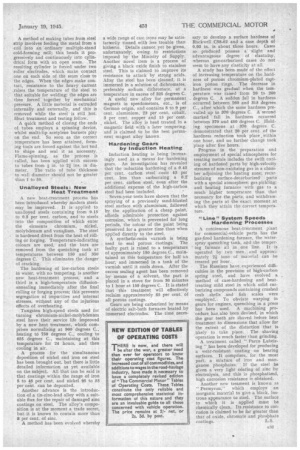
If you've noticed an error in this article please click here to report it so we can fix it.
Progress in the Surfacehardening of Steels : Subzero Heat Treatment of' Ferrous and Non-ferrous Metals: Corrosion Prevention by the Spray Application of Aluminium
SOME interesting new deVeloprnents of value tb the engineer concerned with commercial vehicles may now be enumerated. Tests, for example, have, been carried out with a view to determining how far rust-proofing' of mild..ste.el affects its welding properties, and -Which rifsi-Probfing: protesSes. are .• the mcist satisfactory.frotn this point of view. It has been demonstrated that adequate weldability is exhibited in such cases only with steels which have been = sherardized, electrotinned, or coated with zinc.
Trouble has been encountered in quickly degreasing sheet-metal stamp-jugs' contaminated with oils comprising 15 per cent, saponifiable and 85 per cent, mineral oils. In order to find a satisfactory wetting agent', various experiments were carried out, and success was eventually. achieved by means of a solution comprising 800 gallons a water, 6 cwt. of " Lustros " and 20
of " Perminal N." The nature of these proprietary compounds is not divulged.
To impregnate steel with chromium. gaseous chromium chloride and hydrogen are passed over the metal at 900980 degrees C.; the chromium chloride reacts with the iron and Cr replaces Fe at the surface. Another system cornprises the passing of dried and purified hydrogen into a chamber filled with • glass beads, where it is mixed with anhydrous hydrogen chloride. The mixture is then run through a. quartz *tubecontaining 95 per cent. ferrochromium and, finally, into the furnace containing the part which is to .be treated, By this method a high-chromium corrosioniresistant case is produced at '1,000degrees C. in steels of very loW carbon content, and in chromiummolybdenum steels, but if the carbon content be higher, it becomes necessary to introduce certain other alloying elements to promote diffusion.
Treating Dissimilar Metals in One Bath
The tendency of the developments for the phosphatic coatings of steel has been to work at lower temperatures with a smaller creation of sludge, thus making the operation more flexible and easy of control. This has led to the employment of a solution that makes it possible to treat iron, steel, zinc and cadmium in the same plant at the same time.
A method known as the " D " process has lately been introduced. whereby the bath produces a coating having all the properties of a phosphatic coat with an immersion time of 3 to-5 rains., whilst if the steel be
immersed for about half an hour, the coating goes on developing and takes on additional properties. • Further work has been carried out on the sub-zero heat treatment of steels and non-ferrous. metals. It has been definitely proved that treating 18 per cent. tungsten high-speed steel at temperatures below zero gives tools having higher hardness and ductility and, in consequence, greater service life. Cold treatment also has the effect of stabilizing steel against variation in shape or dimensions. For example, precision slip gauges that used to need a seasoning period of two years can now, by refrigeration treatment, be 'seasoned in as little as two days. The effect of the treatment is to remove all residual austenite.
A new machine has been developed for quenching circular parts, such as gearand sprocket wheels,, flat cams, bearing rings, etc. The principle on which it is based depends on cooling the part from the circumference to the centre, after which all areas of the circumference are plunged in the cooling oil at the same time.
A method of making tubes from steel strip involves feeding the metal from a coil into an 'ordinary multiple-stand cold-forming mill; this bends it progressively and continuously inte cylindrical form with an open scam. The resulting cylinder is forced under two roller electrodes, which make contact one on each side of the seam close to the edges. When the edges make contact, resistance to the heavy current raises the temperature of the steel to that suitable for welding; the edges are then forced together by mechanical pressure. A little material is extruded internally and externally, and this is removed while the steel is still hot. Heat treatment and testing follow.
A quick method of closing the ends of tubes employs a spinning device, whilst multi-tip acetylene burners play on the end. So soon as the correct temperature has been attained, forming tools are forced against the hot 'end to shape and seal it as necessary. Flame-spinning, as the process is called, has been applied with success
to tubes from in. to 2,f, ins, in diameter. The ratio of tube thickness to wall diameter should not be greater than 1 to 50.
Unalloyed Steels: New Heat Treatment
A new heat-treatment process has been introduced whereby modern steels may be improved. It is applied to unalloyed steels containing from 0.15 to 0.5 per cent, carbon, and' to steels into the composition of which enter the elements chromium, nickel, molybdenum and vanabdium. The steel
is hardened direct from the heat of rolling or forging. Temperature-indicating colours arc used, and the bars are removed from the quenching tank at temperatures between 150 and 350 degrees C. This eliminates the danger of cracking.
The hardening of low-carbon steels in water, with no tempering, is another new heat-treatment process, and a third is a high-temperature diffusionannealing immediately after the final rolling or forging process; this prevents segregation of impurities and internal stresses, without any of the injurious effects of overheating.
Tungsten. high-speed steels used for turning chromium-nickel-molybdenum steel have their service life improved by a new heat treatment, which comprises normalizing at 900 degrees C., heating to 750 degrees C., cooling to 655 degrees C., maintaining at this temperature for 24 hours, and then cooling in air.
A process for the simultaneous deposition of nickel and iron on steel has been brought out, but there is little detailed information as yet available on the subject. All that can be said is that coatings within the range of iron 5 to 45 per cent, and nickel 95 to 55 per cent. can be deposited.
Another advance is the introduction of a tin-zinc-lead alloy with a suitable flux for the repair of damaged zinc coatings on steel. The alloy's composition is at the moment a trade secret, but it is known to contain more than 8 per cent, of zinc.
A method has been evolved whereby a wide range of cast irons may be satisfactorily tinned with less trouble than hitherto. Details cannot yet be given, unfortunately, owing to restrictions• imposed by the Ministry of Supply. Another novel item is a process of giving a black oxide finish to stainless steel. This is claimed to improve its resistance to attack by strong acids. After the steel has been cleaned, it is immersed in a solution of dichromates. preferably sodium dichromate, at a temperature in excess of 325 degrees C.
A useful new alloy for permanent magnets in speedometers, etc., is of German origin, and contains 8 to 9 per cent. aluminium, 23 per cent. cobalt, 3 per cent. copper and 15 per cent. nickel. The alloy is heat treated in a magnetic field with a later tempering, and is claimed to be the best permanent magnet alloy known.
Hardening Gears by Induction Heating
Induction heating is being increasingly used as a means for hardening gears. An investigation has revealed that the induction hardenine° of a 0.45 per cent, carbon steel costs 43 per cent. less than carburizing a 0.2' per cent. carbon .steel, even after the additional expense of the high-carbon steel had been included.
Seven-year tests have shown that the spraying of a previously sand-blasted steel surface with aluminium, followed by the application of a cheap paint, affords admirable protection against corrosion, which is prevented for long periods, the colour of the paint being preserved for a greater time than when applied directly to the steel.
A synthetic-resin varnish is being used to seal porous castings. The faulty part is raised to a temperature of approximately 150 degrees C., maintained at this temperature for half -an hour; and immersed in a tank of the varnish until it cools down. After the excess sealing agent has been removed by means of a solvent, the part is placed in a stove for from 30 minutes to 1 hour at 150 degrees C. It is stated that this treatment will effectively reclaim approximately 85 per cent: of all porous castings. Gears are being carburized by means of electric salt-bath furnaces heated by immersed electrodes. The time neces sary to develop a surface hardness of Rockwell C58-62 and a case depth of 0.03 in. is about three hours. Cases so produced possess a slight and advantageous degree of elasticity, whereas gas-carburized cases do not seem to have any elasticity at all.
A study has been madE of the effect of increasing temperature on the hardness of porous chromium-plated cqtiron piston rings. The decrease in hardness was gradual when the temperature was raised from 20 to 200 degrees C.A sudden fall in hardness occurred between 260 and 315 degrees C., after which the same hardness prevailed up to 370 'degrees C. A second marked fall in hardness occurred between 370 and 480 degrees C. Holding specimens at 370 degrees C. demonstrated that 20 per cent, of the hardness reduction took place, within one hour, and no further change took place after five hours.
Progress in the preparation and employment of special atmospheres for treating metals includes the swift cooling of hardened parts by high-velocity streams of non-oxidizing gas in a chamber adjoining the heating zone; man burizing surface-decarburized parts with a special atmosphere; gas pickling; and heating furnaces with gas to a much higher temperature than that necessary for the parts, and withdrawing the parts at the exact moment at which they attain the correct temperature.
"Line" System Speeds Hardening Processes
A continuous beat-treatment pant for commercial-vehicle parts has the gas-fired hardening furnace, the waterspray quenching tank, and the temper ing , furnace an in one line. It is operated by two men, and approximately 2i tons of material can be treated per hour.
The Russians have experienced difficulties in the provision of high-carbon spring steel, and have evolved a method of case-hardening and heattreating mild steel in which solid carburizing compounds containing crushed crab shells and fish scales were employed.. To obviate warping in gears for engines, quenching in a press has been used. A machining procedure has.also been devised, in which the gear teeth are shaved before heat treatment to dimensions that allow for the extent of the distortion that is likely to take place. The shaving operation is much faster than grinding.
A treatment called " Parco Lubrizing " has been developed for producing a wear-resistant coating on bearing surfaces. It comprises, for the most part, a mixture of iron and manganese phosphates. If the steel be given a very light coating of zinc by electrolysis, and this is phosphatized, high corrosion resistance is obtained.
Another new treament is known as " Permyron;" which employs an inorganic material to give a black, lustrous appearance to steel. The surface to which it is applied must be chemically clean. Its resistance to corrogion is claimed to be far greater than that of oxide, chromate and phosPhate coatings. L.S.