USEFUL IDEAS FOR LATHE OPERATORS.
Page 29
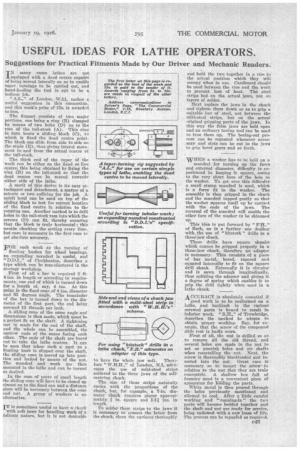
If you've noticed an error in this article please click here to report it so we can fix it.
Suggestions for Practical Fitments Made by Our Driver and Mechanic Readers.
TN many eases lathes are not 1 equipped with a dead centre capable of being moved laterally so as to enable taper turnings to be carried out, and hand-feeding the tool is apt to be a tedious job.
" A.L.," of London, W.11, makes a useful suggestion in this connection, and this week's prize of 15s. is awarded to him.
The fitment consists of two major portions, one being a ring (B) clamped by means of two bolts (I)) on to the ram of the tail-stock (A). This ring in turn bears a sliding block (C), to which is fixed the dead centre point. The block can slide from side to side on the studs (B), thus giving lateral movement to and from the actual centre of the tail-stock.
The thick end of the taper of the work can be either on the fixed or live centre; this being obtained by fixing the ring (B) on the tail-stock so that the dead centre can he moved towards either side of the lathe.
A merit of this device is its easy attachment and detachment, a matter of a minute or two sufficing for the job. A spirit level can be used on top of the sliding block to test for correct location of the fixed centre in relation to the rotating one. Another method is to drill holes in the tail-stock ram into which the screws (D) can lit, thereby ensuring that the block is truly horizontal ; this avoids checking the setting every time. but care is necessary in the first case to get absslute accuracy.
FOR such work as the turning of floating bushes for wheel bearings, an expanding mandrel is useful, and "D.D.T.." of Cleckheaton, describes a type which can be manufactured in the average workshop.
First of all a bar is required 2 ft. 4 ins, in length or according to requirements, one end of which is turned down for a length of, say, 4 ins. At this point is the fixed cone of 4 ins, diameter and 65 degrees angle. The remainder of the bar is turned down to the diameter of the first part, the end being screwed 12 threads per inch.
A sliding cone of the same angle and dimensions is then made, which must be a perfect fit on the shaft. A tightening nut is made for the end of the shaft, and the whole can be assembled, the narrow ends of the cones facing each other. The ends of the shaft are bored out to take the lathe centres. It can be seen that when such a part as a floating bush is slipped over the shaft, the sliding cone is moved up into position and locked by means of the nut. The mandrel and work are then mounted in the lathe and can be turned as desired.
Ii the case of parts of small length the sliding cone will have to be closed up almost on to the fixed one and a distance piece will be necessary between the cone and nut. A group of washers is an alternative.
IT is sometimes useful to have a chuck with soft jaws for handling work of a delicate nature, but it is not desirable
to have the whole jaw soft. Thersfore " WELK," of London, Ni, advocates the use of mild-steel strips soldered to the three jaws of the selfcentring chuck.
The size of these strips naturally -varies with the proportions of the chuck, but, for example, a 7-in, diameter chuck requires pieces approxi
mately in. square and 111 ins, in length.
To solder these strips to the jaws it is necessary to remove the latter from the chuck, clean the surfaces thoroughly and hold the two together in a vice in the actnal position which they will occupy when in use. Cardboard should be used between the vice and the work to prevent loss of heat. The steel strips bed on the actual jaws, not on layers of solder.
Next replace the jaws in the chuck and tighten them down so as to grip a suitable bar of steel, not between the mild-steel strips, but on the actual original gripping parts of the jaws. In this way the false jaws are held open and an ordinary boring tool can be used to true them up. The boring-out process can be repeated whenever necessary and slots can be cut in the jaws to grip bevel gears and so forth.
WHEN a washer has te he held on a
mandrel for turning up the faces and external diameter, difficulty is experienced in keeping it square, owing to the very short bore of the hole in the washer. To get over this difficulty a small stump mandrel is used, which is a force fit in the washer. The assembly is then gripped in the chuck and the mandrel tapped gently so that the washer squares itself up by contact with the ends of the jaws. The reversal of the mandrel will enable the other face of the washer to be skimmed up.
This idea is put forward by " of Bath, as is a further one dealing with the use of " bitstock " drills in a three-jaw chuck.
These drills have square shanks which cannot be gripped properly in three-jaw chuck, 'therefore an adapter is necessary. This consists of a piece of bar metal, bored, tapered and squared internally to fit on the square drill shank. Externally it is circular and is sawn through longitudinally, thus splitting the adapter and giving it a degree of spring which enables it to grip the drill tightly when used in a lathe chuck.
ACCURACY is absolutely essential if good work is to be performed on a lathe, and backlash in the various screwed parts is bound to result in
inferior work. " of Trowbridge, describes the method he adopts to obtain proper working. Say, for example, that the screw of the compound slide rest is badly worn.
First of all, the nut is drilled so as to remove all the old thread, and several holes are made in the nut to act as pouring holes and air shafts when remetalling the nut. Next, the screw is thoroughly blackleaded and inserted into the nut. Great care is necessary so to mount the screw in relation to the nut that they are truly concentric. A shallow box full of foundry sand is a convenient piece of apparatus for holding the parts.
White metal is then poured through the boles previously mentioned and allowed to cool. After a little careful working and " running-in " the two Parts will become bedded together and the shaft and nut are ready for service, being endowed with a new lease of life. The process can be repeated as required.