SURFACE ACCURAC NND LUBRICATION
Page 26
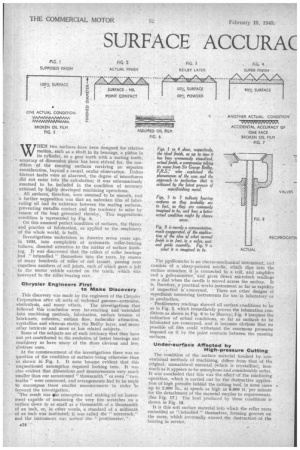
Page 27
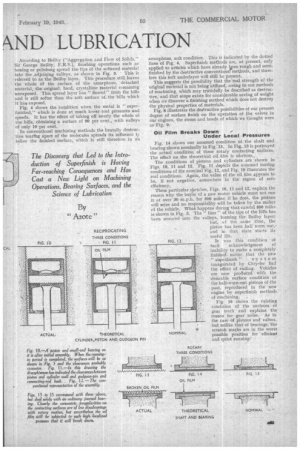
Page 28
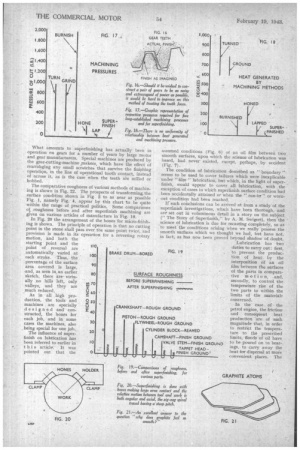
Page 29
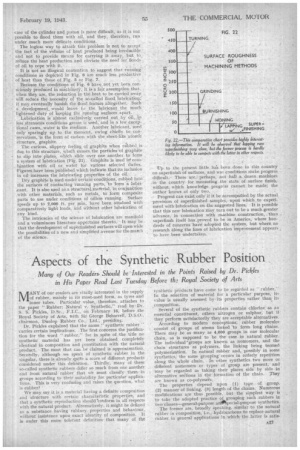
If you've noticed an error in this article please click here to report it so we can fix it.
WHEN two surfaces have been designed for relative motion, such as a shaft in its bearings, a piston in its cylinder, or a gear tooth with a mating tooth, accuracy of dimension alone has been strived for, the condition of the running surfaces receiving no separate consideration, beyond a casnal, ocular observation. Unless . blatant faults were so observed, . the degree of Smoothness did not enter into the calculation; it was subconsciously assumed to be included in the condition of accuracy attained by highly developed machining operations.
All surfaces, therefore, were assumed" to be smooth, and a further supposition was that ao unbroken film of lubricating' oil had its-existence between the mating surfaces, preventing metallic contact and the tendency to seize by reason of the heat generated thereby.. This suppositious 'condition is represented by Fig. 6.
. On this assumed perfect condition of surfaces, the theory and practice of lubrication, as applied to the machinery • of the whole world, is built.
Investigations undertaken in America seven years ago, in 1935. , into complaints of systematic roller-bearing failures, directed attention .to the matter of surface finishing. It was discovered that the rollers of roller bearings had " brinnelled " themselves into the races, by reason
• of many hundreds of miles of rail transit, passing over countless numbers of rail joints, each Of which gave a jolt to the motor vehicle .carried on the. truck, which lcis
. conveyed to the roller-bearing race.
Chrysler Engineers First _ to Make Discovery This discovery was made by the engineers of the Chrysler Corporation after all sorts of technical guesses—corrosion, electrolysis, and many others. The investigations that
• followed this conclusion were far-reaching and 'extended into machining methods, lubrication, surface tension of lubricants, cohesion, surface flow, molecurat attraction. crystalline and vitreous states,' the Beilby layer, and many other intricate and more or less related subjects. Some of the subjects are of such intricacy that they have not yet contributed to the evolution cf better bearings and machjnery as have many of the More obviouS and less: abstruse ones.
At the commencement of the investigations there was no
• question of the condition of surfaces being otherwise than as shown in Fig. 1. It soon became evident that this tinquestioned assumption required looking into. It was also evident that dimensions and measurements very much smaller than our accustomed "thousandth" or even " twotenths " were concerned, and arrangements had to be made to encompass these smaller measurements in order to forward the investigation.
"the result was .ho conception and making-of an instrument capable of measuring the very fine scratches on a 'surface down to as' small as a thousandth of a thousandth of an inch, or, in other words, a standard of a millionth :of an inch was instituted; it was called the " microinch," and the instrument was named the -" profilorheter." . The p{ofilometer is an electro-mechanical instrument, and consists of a -sharp-pointed needle, which dips into the surface scratches; it is connected to a coil, and amplifier and a galvanometer, 'and gives direct' microinch readings on a dial when the needle is moved across the surface. It is, therefore, a practical works instrument so far as rapidity of inspection is' concerned, There are other designs of superfinish measuring instruments for use in laboratory or in productions • Profilometer readings showed all surface-conditions to be as in Fig. 2, which immediately proves the lubrication con• ditions as shown in Fig. 6-to beillusory;.Fig. 5 becomes theindication of actual conditions, so far as surfaces to be lubricated are concerned, and it becomes obvious that no possible oil, film could withstand the enormous pressures imposed on it by the point contacts between the running surfaces,
Under-surface Affected by High-pressure Cutting
The condition of the surface material finished by conventional methods of machining, differs from that of the original, unmachined material (which is crystalline), inasmuch as it appears tcebe amorphous and considerably softer. It was concluded that this was the effeet 'of the machining operation, which is carried out by the destructive application of high presstfre behind the cutting tool, in some cases • up to 2,000 lb., at speeds as high aS 8,000 ft. per minute for the detachment of the material surplus to requirements. (See Fig. 17.) The heat produced by these conditions is shown in Fig. 18. • It is this soft surface material into which the roller races embedded or "Asrinelled " themselves; forming grooves on the races, which eventually caused, the destruction of the bearing in service. .
According to Beilby ("Aggregation and Flow of Solids," Sir George Beilby; F.R.S.), finishing operations such as honing or polishing spread the-tips of the softened material into the adjoining valleys, as shown in Fig. 3. • This is referred to as the Beilby layer. This procedure still leaves the whole of the surface of the amorphous, detached material, the original, hard, crystalline material remaining unexposed. This spread layer has " flowed" from the hills and is still softer than the soft surface of. the hills which it has. exposed.
Fig. 4 shows the Condition when the metal is ." superfinished," Which is done at much loWer tool pressures and speeds. It has the effect of taking off nearly the whole of the hills, obtaining a surface of 90 per cent„ with valleys of only 10 per cent.
In conventional machining methods the brutally destructive tearitig apart of the molecules spreads its influence tc below the finished surface, which is still therefore in an
amorphous, soft condition. This is indicated by the dotted lines of Fig. 4. Superfinish methods are, at present, only applied to articles which have already lien rough and semifinished by the destructive conventionarrnethods, and therefore this soft underlayer will Still be present.
This suggests the possibility that the'real strength of the original material is not being utilized, owing to our methods of machining, which may truthfully be described as destructive, and that scope exists for considerable saving of weight when we discover a finishing method which does not destroy the physical properties of. materials. Fig. 8 illustrates the destructive possibilities of our present degree of surface finish on the operation of the valves in our engines, the stems and heads of which we thought were as Fig. 9;
Oil Film Breaks Down Under Local Pressures
Fig. 14 shows our assumed condition of the shaft and bearing shown nominally in Fig: 15. In Fig. 13 is portrayed the actual' condition of these rotary contacting surfaces. The effect on the theoretical oil film is obvious.
The conditions of pistons and cylinders are shown in Figs. 10, 11 and 12. Fig. 11 depicts the assumed mating conditions of the nominal Fig. 12, and Fig. 10 illustrates the real conditions. Again, the value of the oil film appears to be, if not negative, somewhere in the region of zero efficiency. These particular *etches, Figs. 10, 11 and 12, explain the reason why the bufer of a new motor vehicle must not run it at over 30 m.p.h. for 500 miles; if he does, the pistons. \rill seize and no responsibility will be taken by the maker of the vehicle.What happens during that careful 500 miles is shown in Fig. 3. The " fuzz of the tips of the hills has been smeared into the valleys, forming the Beilby layer:
but, E.t the same time, the piston has been hall worn out, anti in that state starts its
FIG. 12 useful life. ,
It was this condition of tacit acknowledgment of inability to make a completely finished, motor that the new " saperfinish " s-y a t e rn inaugurated by Chrysler had the effect of ending. Vehicles are now produced with the desirable surface condition of the half-worn-out pistons of the past, reproduced in the new engine by superfinish methods of machining.
Fig. 16 shows the existing condition of the surfaces of gear teeth and explains the' reason for gear noise. As in the case of pistons and valves, but unlike that of bearings, the scratch marks are in the worst possible position for efficient and quiet running:
What amounts to superfinishing has actually been in operation on gears for a number of years by large motor and gear manufacturers. Special machines are produced by the gear-cutting-machine „makers, which have the effect of reamtiging any small scratches that survive the finishing operation, in the line of operational tooth contact, instead of across it, as is the case when the teeth ale milled or hobbed.
The comparative roughness of variou§ methods of machining is shown in Fig. 22. The prospects of transforming, the surface condition shown in Fig 2 to as near as possible Fig. 1, namely Fig. 4, appear by this chart to be quite within the range of practical politics. Some comparisons of roughness before and after superfinish machining are given on various articles of manufacture in Fig. 19.
As in all high production, the tools and machines are specially designed and constructed, the hones for each job, and in some cases the machines, also _being special for one job.
The influence of superfinish on lubrication has been referred to earlier in t his article. It was pointed out that the
assumed conditions. (Pig. 6) of an oil film between two smooth surfaces, upon which the science of lubrication was based, had never existed, except, perhaps, by accident (Fig. 7).
The condition of lubrication described as " boundary " seems to be used to cover failures which were inexplicable under "film " lubrication, but which, in the light of super_ finish, would appear to cover all lubrication; with the exception of cases in which superfinish surface condition had been accidentally attained or when the ".run-hr " or worn out condition had been reached, • If such conclusions can be arrived at from a study of the superfinish investigations, which have been thorough, and are set out in voluminous detail in a story on the subject (" The Story of Superfinish," by A. M. Swigert), then the science of lubrication is due for recasting completely, so as to meet the conditions arising when we really possess the smooth surfaces which we thought we had, but have not, in fact, as has now been proved beyond shadow of doubt. Lubrication has two duties to carry out: first,
FIG. 19 to prevent the production of heat by the interposition of an oil film between the surfaces of the parts in comparative motion, and, secondly, to control the temperature rise of the two parts to within the limits of the materials concerned. BEFORE 5UPERFIN1SHING AFTER SuPERFINISHING yonmeme. In the case of the petrol engine, the friction and consequent heat production are of such magnitude that, in order to restrict the temperature to the prescribed limits, floods of oil have to be poured on to bearings, to carry away the heat for dispersal at more
■ •()ovenient places. The
case of the cylinder and piston is more difficult, as it is not possible to flood them with oil, and they, therefore; run under much more delicate conditions.
The logical Way to attack this problem is not to accept the fact of the volume of heat produced being irreducible and not to provide means for carrying it away, but to reduce the heat production and obviate the need for floods of oil to cope with it.. . It is not an illogical contention to suggest that -running conditions as depicted in Fig. 6 are much less.productive of heat than those of Fig. 5 or Fig. 7. .
Because the conditions of Fig. 6 have. not yet 1.?teu con
sciously . seiously produeed in niachinerY; it is a fair assumption that, when they are, the reduction in the heat to be carried away will reduce the necessity orthe SO-called flood _lubrication; it may eventually banish the flood feature altogether. Such a development_ would leave h) the lubricant_ the much lightened-duty of 'keeping the renniog surfaces apart.
Lubrication is almost exclusively carried out by cill, ih less strenuous conditions grease is used; and in a few exceptional cases, water is the medium. Another lubricant, used only sparingly up to the moment, owing Chiefly to conservatism, -is the form of carbon with the sheet-like atomic
structure, graphite. . The curious, slippery feeling of graphite when LAW is due to this structure, which causes, the particles 'of graphite to slip into plates, which slide (wer one another to form a system of lubrication (Fig. 21) 'Graphite is used jet combination with oil or water for various selected duties. Figures have been published which indicate that its inclusion in oil increases the lubricating properties of the oil. . Dry graphite is used under certain conditions, rubbhcl into the surfaces of contacting running parts, 'to form a luhri.cant. It is also used as.a structural material, in conjunCtion with other materials, such as metals, to form composite parts to use under conditions of oilless running. Surface speeds up to 2,00) ft. per min. have been attained with comparatively light loads, and without other lubrication of any kind.
The intricacies of the science of lubrication are manifold and a voluminous literature appertains thereto. It may be that the development of superfinished surfaces will open wide the possibilities of a new and simplified avenue for the march of the science.
Up to the present little ha's been done in this country on superfinish -of surfaces, and was conditions snake progress difficult.There are, perhaps, not halt a dozen. machines . in • the country for measuring the state of surface finish, -without. which knowledge progri.ss cannot be made; the author knows of only two.
Progres§ can exist only if it be accompanied by the actual provision of superfinished samples, upon which to experh. merit with lubrication on the suggested lines. It is possible that this new lubrication may turn out to be a much.greater advance, in connection with machine construction, ;than superfiiash itself has,proved to be in America, where hundreds of concerns have adopted the system, bat where no research along the lines of lubrication improvement appears, to have been undertaken: