Better than new claim for retreading tyres
Page 18
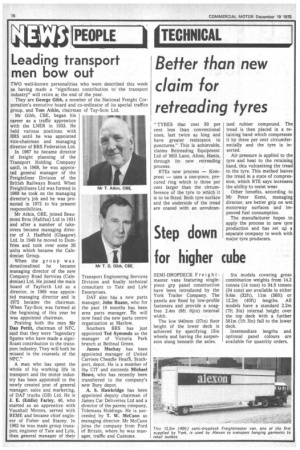
If you've noticed an error in this article please click here to report it so we can fix it.
"TYRES that cost 50 per cent less than conventional ones, last twice as long and have greater resistance to punctures." This is achievable, claims Retreading Equipment Ltd of Mill Lane, Alton, Hants, through its new retreading process.
RTEs new process — Kemprest — uses a one-piece, precured ring which is three per cent larger than the circumference of the tyre to which it is to be fitted. Both tyre surface and the underside of the tread are coated with an unvalcan ised rubber compound. The tread is then placed in a retaining band which compresses it by three per cent circumferentially and the tyre is inserted.
Air pressure is applied to the tyre and heat to the retaining band, this vulcanising the tread to the tyre. This method leaves the tread in a state of compression, which RTE says increases the ability to resist wear.
Other benefits, according to Mr Peter Kemt, managing director, are better grip on wet motorway surfaces and improved fuel consumption.
The manufacturer hopes to apply the process to new tyre production •and has set up a separate company to work with major tyre producers.