Reefers in big
Page 44
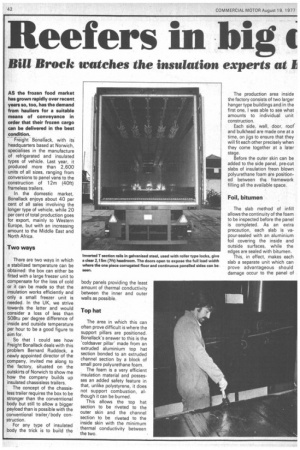
Page 45
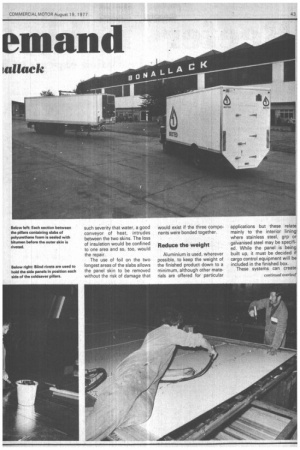
Page 46
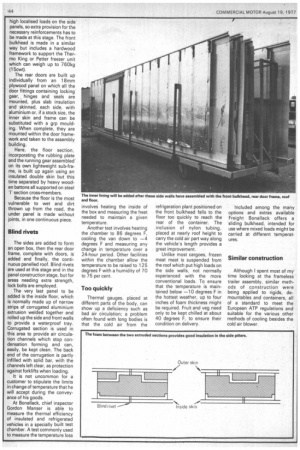
If you've noticed an error in this article please click here to report it so we can fix it.
Bill Brock watches the insulation experts at
AS the frozen food market has grown rapidly over recent years so, too, has the demand from hauliers for a suitable means of conveyance in order that their frozen cargo can be delivered in the best condition.
Freight Banallack, with its headquarters based at Norwich, specialises in the manufacture of refrigerated and insulated types of vehicle. Last year, it produced more than 2,600 units of all sizes, ranging from conversions to panel vans to the construction of 12m (40ft) frameless trailers.
In the domestic market, Bonallack enjoys about 40 per cent of all sales involving the longer type of vehicle, while 20 per cent of total production goes for export, mainly to Western Europe, but with an increasing amount to the Middle East and North Africa.
Two ways
There are two ways in which a stabilized temperature can be obtained: the box can either be fitted with a large freezer unit to compensate for the loss of cold or it can be made so that the insulation works efficiently and only a small freezer unit is needed. In the UK, we strive towards the latter and would consider a loss of less than 50Btu per degree difference of inside and outside temperature per hour to be a good figure to aim for.
So that I could see how Freight BonaIlack deals with this problem Bernard Ruddock, a newly appointed director of the company, invited me along to the factory, situated on the outskirts of Norwich to show me how the company builds up insulated chassisless trailers.
The concept of the chassisless trailer requires the box to be stronger than the conventional body but still to allow a bigger payload than is possible with the conventional trailer! body construction.
For any type of insulated body the trick is to build the body panels providing the least amount of thermal conductivity between the inner and outer walls as possible.
Top hat
The area in which this can often prove difficult is where the support pillars are positioned. Bonallack's answer to this is the 'coldsaver pillar' made from an extruded aluminium top hat section bonded to an extruded channel section by a block of small pore polyurethane foam.
The foam is a very efficient insulation material and possesses an added safety feature in that, unlike polystyrene, it does not support combustion, although it can be burned.
This allows the top hat section to be riveted to the outer skin and the channel section to be riveted to the inside skin with the minimum thermal conductivity between the two. The production area inside the factory consists of two larger hanger type buildings and in the first one, I was able to see what amounts to individual unit construction.
Each side, wall, door, roof and bulkhead are made one at a time, on jigs to ensure that they will fit each other precisely when they come together at a later stage.
Before the outer skin can be added to the side panel, pre-cut slabs of insulation freon blown polyurethane foam are positioned between the framework filling all the available space.
Foil, bitumen
The slab method of infill allows the continuity of the foam to be inspected before the panel is completed. As an extra precaution, each slab is vapour-sealed with an aluminium foil covering the inside and outside surfaces, while the edges are sealed with bitumen.
This, in effect, makes each slab a separate unit which can prove advantageous should damage occur to the panel of such severity that water, a good conveyor of heat, intrudes between the two skins. The loss of insulation would be confined to one area and so, too, would the repair.
The use of foil on the two longest areas of the slabs allows the panel skin to be removed without the risk of damage that would exist if the three components were bonded together.
Reduce the weight
Aluminium is used, wherever possible, to keep the weight of the finished product down to a minimum, although other materials are offered for particular applications but these relate mainly to the interior lining. where stainless steel, grp or galvanised steel may be specified. While the panel is being built up, it must be decided if cargo control equipment will be included in the finished box.
These systems can create high localised loads on the side panels, so extra provision for the necessary reinforcements has to be made at this stage. The front bulkhead is made in a similar way but includes a hardwood framework to support the Thermo King or Petter freezer unit which can weigh up to 760kg (15cwt).
The rear doors are built up individually from an 18mm plywood panel on which all the door fittings containing locking. gear, hinges and seals are mounted, plus slab insulation and skinned, each side, with aluminium or, if a stock size, the inner skin and frame can be substituted with a grp moulding. When complete, they are mounted within the door framework and taken to the assembly building.
Here, the floor section, incorporating the rubbing plate and the running gear assembled' on its own lightweight sub-frame, is built up again using an insulated double skin but this time separated by heavy wooden battons all supported on steel 'I' section cross-members, Because the floor is the most vulnerable to wet and dirt thrown up from the road, the under panel is made without joints, in one continuous piece.
Blind rivets
The sides are added to form an open box, then the rear door frame, complete with doors, is added and finally, the continuous panelled roof. Blind rivets are used at this stage and in the panel construction stage, but for areas needing extra strength, lock bolts are employed.
The very last panel to be added is the inside floor, which is normally made up of narrow strips of corrugated aluminium extrusion welded together and rolled up the side and front walls to provide a waterproof tray. Corrugated section is used in this area to provide air circulation channels which stop condensation forming and can, easily, be kept clean. The back end of the corrugation is partly infilled with solid bar, with the channels left clear, as protection against forklifts when loading.
It is not uncommon for a customer to stipulate the limits in change of temperature that he will accept during the conveyance of his goods.
At Bonallack, chief inspector Gordon Manser is able to measure the thermal efficiency of insulated and refrigerated vehicles in a specially built test chamber. A test commonly used to measure the temperature loss involves heating the inside of the box and measuring the heat needed to maintain a given temperature.
Another test involves heating the chamber to 86 degrees F, cooling the van down to —4 degrees F and measuring any change in temperature over a 24-hour period. Other facilities within the chamber allow the temperature to be raised to 125 degrees F with a humidity of 70 to 75 per cent.
Too quickly
Thermal gauges, placed at different parts of the body, can show up a deficiency such as bad air circulation; a problem often found with long bodies is that the cold air from the refrigeration plant positioned on the front bulkhead falls to the floor too quickly to reach the rear of the container. The inclusion of nylon tubing, placed at nearly roof height to carry the cold air part way along the vehicle's length provides a great improvement.
Unlike most cargoes, frozen meat meat is suspended from the roof which put high loads on the side walls, not normally experienced with the more conventional loads. To ensure that the temperature is maintained below —10 degrees F in the hottest weather, up to four inches of foam thickness might be required. Fruit and veg need only to be kept chilled at about 40 degrees F, to ensure their condition on delivery. Included among the many options and extras available Freight Bonallack offers a sliding bulkhead, intended for use where mixed loads might be carried at different temperatures.
Similar construction
Although I spent most of my time looking at the frameless trailer assembly, similar methods of construction were being applied to rigids, demountables and containers, all of a standard to meet the European ATP regulations and suitable for the various other methods of cooling besides the cold air blower.