THE WEAK LINK
Page 47
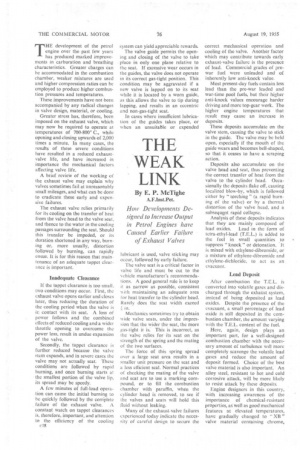
Page 48
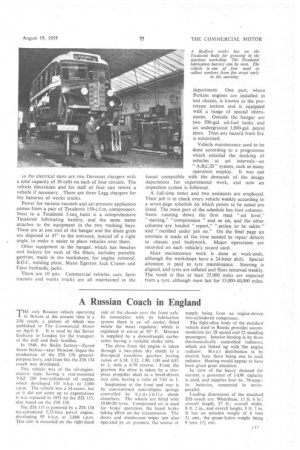
If you've noticed an error in this article please click here to report it so we can fix it.
By E. P. McTighe A.F.Inst.Pet.
How Developments Designed to Increase Output in Petrol Engines have Caused Earlier Failure of Exhaust Valves
THE development of the petrol engine over the .past few years has produced marked improvements in carburation and breathing characteristics. Greater charges can he accommodated in the combustion chamber, weaker mixtures are used and higher compression ratios can be employed to produce higher combustion pressures and temperatures.
These improvements have not been accompanied by any radical changes in valve design, material, or cooling.
Greater stress has, therefore, been imposed on the exhaust valve, which may now be required to .operate at temperatures of 700-800° C., while opening and closing upwards of 2,000 times a minute. In many cases, the results of these severe conditions have resulted in a reduced exhaustvalve life, and have increased in importance the mechanical factors affecting valve life.
A brief review of the working of the exhaust valve may explain why valves sometimes fail at unreasonably small mileages, and what can be done to eradicate these early and expensive failures.
The exhaust valve relies primarily for its cooling on the transfer of heat from the valve head to the valve seat, and thence to the water in the cooling passages surrounding the seat. Should this transfer be impeded, or its duration shortened in any way, burning or, more usually, distortion followed by burning, can rapidly ensue. It is for this reason that maintenance of an adequate tappet clearance is important.
Inadequate Clearance
If the tappet clearance is too small, Iwo conditions may occur. First, the exhaust valve opens earlier and closes later, thus reducing the duration of the cooling period when the valve is in contact with its seat. A loss of power follows and the combined effects of reduced cooling and a wider throttle opening to overcome the power loss, result in undue expansion of the valve.
Secondly, the tappet clearance is further reduced because the valve stem expands, and in severe cases the valve may not actually seat, These conditions are followed by rapid burning, and once burning starts at the smallest portion of the valve lip, its spread may be speedy.
A few minutes of full-load opera • lion can cause the initial burning to be quickly followed by the complete failure of the . exhaust valve. A constant watch on tappet clearances is, therefore, important, and attention to the efficiency of the cooling c18 system can yield appreciable rewards.
The valve guide permits the opening and closing of the valve to take place in only one plane relative to the seat. If excessive wear occurs in the guides, the valve does not operate in its correct gas-tight position. This condition may be aggravated if a new valve is lapped on to its seat while it is located by a worn guide, as this allows the valve to tip during lapping, and results in an eccentric and non-gas-tight seat.
In cases where insufficient lubrication of the guides takes place, or when an unsuitable or expended lubricant is used, valve sticking may occur, followed by early failure.
The valve seat is a critical factor in valve life and must be cut to the vehicle manufacturer's recommendations. A good general rule is to keep it as narrow as possible, consistent with maintaining an adequate area for heat transfer to the cylinder head. Rarely does the seat width exceed in.
Mechanics sometimes try to obtain wide valve seats, under the impression that the wider the seat, the more gas-tight it is: This is incorrect, as the valve relies for its seat on the strength of the spring and the mating of the two surfaces.
The force of this spring spread over a large seat area results in a smaller unit pressure on the seat and a less efficient seal. Normal practices of checking the mating of the valve and seat are to use a marking compound, or to fill the combustion chamber with paraffin, when the cylinder head is removed, to see if the valves and seats will hold this fluid without leaking.
Many of the exhaust-valve failures experienced today indicate the necessity of careful design to secure the correct mechanical operation and cooling of the valve. Another factor which may contribute towards early exhaust-valve failure is the presence of lead. Commercial grades of prewar fuel were unleaded and of inherently low anti-knock value.
Most present-day fuels contain less lead than the pre-war leaded and war-time pool fuels, but their higher anti-knock values encourage harder driving and more top-gear work. The higher engine temperatures that result may cause an increase in deposits.
These deposits accumulate on the valve stem, causing the valve to stick in the guide. The valve may be held open, especially if the mouth of the guide wears and becomes bell-shaped, so that it ceases to have a scraping action.
Deposits also accumulate on the valve head and seat, thus preventing the correct transfer of heat from the valve to the cylinder head. Occasionally the deposits flake off, causing localized blow-by, which is followed either by " torching " (a rapid burning of the valve) or by a thermal distortion of the valve head, and a subsequept rapid collapse.
Analysis of these deposits indicates that they are mainly composed of lead oxides. Lead in the form of tetra-ethyl-lead (T.E.L.) is added to the fuel in small quantities to suppress " knock " or detonation. It is mixed with ethylene-dibromide, or a mixture of ethylene-dibromide and ethylene-dichloride, to act as an evac uan t.
Lead Deposit
After combustion the T.E.L. is converted into volatile gases and discharged through the exhatist system, instead of being deposited as lead oxides. Despite the presence of the evacuant, a small percentage of lead oxide is still deposited in the combustion chamber, the amount varying with the TEL. content of the fuel.
Here, again, design plays an important part, for a well-designed combustion chamber with the necessary amount of turbulence will more completely scavenge the volatile lead gases and reduce the amount of deposit formed. Choice of the best valve material is also important. An alloy steel, resistant to hot and cold corrosive attack, will be more likely to resist attack by these deposits.
Engine designers in this country, with increasing awareness of the importance of chemical-resistant properties, as wellas good mechanical features at elevated temperatures, have gradually changed to "XE" valve material containing chrome, in the electrical store are two Davenset chargers with a total capacity of 30 cells on each of four circuits. The vehicle electrician and his staff of four can rewire a vehicle if necessary. There are three Legg chargers for the batteries of works trucks.
Power for various vacuum and air-pressure appliances comes from a pair of Tecalemit 150-c.f.m. compressors. Next to a Tee-alma 5-ton. hoist is a comprehensive Tecalemit lubricating battery, and the same name attaches to the equipment in the two washing bays. These are at one end of the hangar and the drain grids are disposed at 45° to the entrance, instead of a right angle, to make it easier to place vehicles over them.
Other equipment in the hangar, which has benches and lockers for each of the fitters, includes portable gantries, made in the workshops, for engine removal, B.O.C. welding plant, Mann Egerton Jack Cranes and Epeo hydraulic jacks.
There are 10 pits_ Commercial vehicles, cars, farm tractors and works trucks are all maintained in the department. One part, where Perkins engines are installed in test chassis, is known as the prototype section and is equipped with a range of special instruments. Outside the hangar are two 500-gal. oil-fuel tanks and an underground 1,000-gal. petrol store. Thus any hazard from fire is minimized.
Vehicle maintenance used to be done according to a programme which entailed the docking of vehicles at set intervals—an " A,B,C,D " system, such as many operators employ. It was not found compatible with the demands of the design department for experimental work, and now an inspection system is followed.
A full-time tester and two assistants are employed. Their job is to check every vehicle weekly according to a seven-page schedule on which points to be noted are listed. The main part of the schedule has four columns. Items running down the first read "oil level," "starting," "compression and so on, and the other columns are headed "report," "action to be taken_ " and "rectified under job no." On the final page an estimate is made of the time needed to repair defects to chassis and bodywork. Major operations are recorded on each vehicle's record card.
Most maintenance work is done at week-ends, although the workshops have a 24-hour. shift.' Special attention is paid to tyre maintenance. Steering is aligned, and tyres are inflated and flints removed weekly. The result is that at least 25,000 miles are expected from a tyre, although most last for 35,000-40,000 miles.