Safe way to pick-up tips on lorry loaders
Page 36
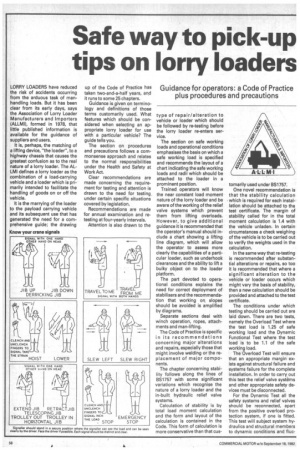
Page 37
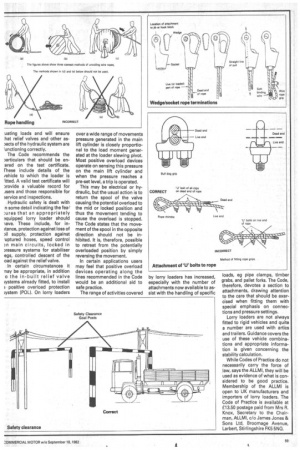
If you've noticed an error in this article please click here to report it so we can fix it.
LORRY LOADERS have reduced the risk of accidents occurring from the arduous task of manhandling loads. But it has been clear from its early days, says the Association of Lorry Loader Manufacturers and Importers (ALLMI), formed in 1978, that little published information is available for the guidance of suppliers and users, It is, perhaps, the matching of a lifting device, "the loader", to a highway chassis that causes the greatest confusion as to the real nature of a lorry loader. The ALLMI defines a lorry loader as the combination of a load-carrying vehicle and a loader which is primarily intended to facilitate the handling of goods on or off the vehicle.
It is the marrying of the loader to the payload carrying vehicle and its subsequent use that has generated the need for a cornprehensive guide; the drawing up of the Code of Practice has taken two-and-a-half years, and it runs to some 25 chapters.
Guidance is given on terminology and definitions of those terms customarily used. What features which should be considered when selecting an appropriate lorry loader for use with a particular vehicle? The guide tells you.
The section on procedures and precautions follows a cornmonsense approach and relates to the normal responsibilities under the Health and Safety at Work Act.
Clear recommendations are made concerning the requirement for testing and attention is drawn to the need for testing under certain specific situations covered by legislation.
Recommendations are made for annual examination and retesting at four-yearly intervals.
Attention is also drawn to the type of repair/alteration to vehicle or loader which should be followed by re-testing before the lorry loader re-enters service.
The section on safe working loads and operational conditions emphasises the basis on which a safe working load is specified and recommends the layout of a chart indicating the safe working loads and radii which should be attached to the loader in a prominent position.
Trained operators will know the near constant load moment nature of the lorry loader and be aware of the working of the relief valve systems which prevent them from lifting overloads. However, to give additional guidance it is recommended that the operator's manual should include a chart showing a lifting line diagram, which will allow the operator to assess more clearly the capabilities of a particular loader, such as underhook clearances and the ability to lift a bulky object on to the loader platform.
The part devoted to operational conditions explains the need for correct deployment of stabilisers and the recommendation that working on, slopes should be avoided is amplified by diagrams.
Separate sections deal with winch operation, ropes, attachments and man-lifting.
The Code of Practice is specific in its recommendations concerning major alterations and repairs, especially those that might involve welding or the replacement of major components.
The chapter concerning stability follows along the lines of BS1757 with some significant variations which recognise the nature of a lorry loader and the in-built hydraulic relief valve systems.
Calculation of stability is by total load moment calculation and the form and layout of the calculation is contained in the Code. This form of calculation is more conservative than that cus tomarily used under BS1757.
One novel recommendation is that the stability calculation which is required for each installation should be attached to the test certificate. The margin of stability called for in the total moment calculation is 1,4 with the vehicle unladen. In certain circumstances a check weighing of the vehicle is to be carried out to verify the weights used in the calculation.
In the same way that re-testing is recommended after substantial alterations or repairs, so too it is recommended that where a significant alteration to the vehicle or loader occurs which might vary the basis of stability, then a new calculation should be provided and attached to the test certificate.
The conditions under which testing should be carried out are laid down. There are two tests, namely the Overload Test where the test load is 1.25 of safe working load and the Dynamic Functional Test where the test load is to be 1.1 of the safe working load.
The Overload Test will ensure that an appropriate margin exists against structural failure and systems failure for the complete installation. In order to carry out this test the relief valve systems and other appropriate safety devices must be disconnected.
For the Dynamic Test all the safety systems and relief valves should be reconnected, apart from the positive overload protection system, if one is fitted. This test will subject system hydraulics and structural members to dynamic conditions and fluc uating loads and will ensure hat relief valves and other asacts of of the hydraulic system are 'unctioning correctly.
The Code recommends the mrticulars that should be enered on the test certificate. rhese include details of the rehicle to which the loader is 'Med. A valid test certificate will 3rovide a valuable record for ism and those responsible for ;ervice and inspections.
Hydraulic safety is dealt with n some detail indicating the tea: :ures that an appropriately aquipped lorry loader should lave. These include, for inrtance, protection against loss of Al supply, protection against uptured hoses, speed control )n main circuits, locked in nessure systems for stabiliser egs, controlled descent of the oad against the relief valve.
In certain circumstances it nay be appropriate, in addition o the in-built relief valve wstems already fitted, to install positive overload protection ;ystem (POO. On lorry loaders over a wide range of movements pressure generated in the main lift cylinder is closely proportional to the load moment generated at the loader slowing pivot. Most positive overload devices operate on sensing this pressure on the main lift cylinder and when the pressure reaches a pre-set level, a trip is operated.
This may be electrical or hydraulic, but the usual action is to return the spool of the valve causing the potential overload to the mid or locked position and thus the movement tending to cause the overload is stopped. The Code states that the movement of the spool in the opposite direction should not be inhibited. It is, therefore, possible to retreat from the potentially overloaded position by simply reversing the movement.
In certain applications users may feel that positive overload devices operating along the lines recommended in the Code would be an additional aid to safe practice.
The range of activities covered by lorry loaders has increased, especially with the number of attachments now available to assist with the handling of specific loads, eg pipe clamps, timber grabs, and pallet forks. The Code, therefore, devotes a section to attachments, drawing attention to the care that should be exercised when fitting them with special emphasis on connections and pressure settings.
Lorry loaders are not always fitted to rigid vehicles and quite a number are used with artics and trailers. Guidance covers the use of these vehicle combinations and appropriate information is given concerning the stability calculation.
While Codes of Practice do not necessarily carry the force of law, says the ALLMI, they will be used as evidence of what is considered to be good practice. Membership of the ALLMI is open to UK manufacturers and importers of lorry loaders. The Code of Practice is available at £13.50 postage paid from Mrs R. Knox, Secretary to the Chairman, ALLMI, c/o James Jones & Sons Ltd, Broomage Avenue, Larbert, Stirlingshire FK5 5N0.