road and workshop
Page 133
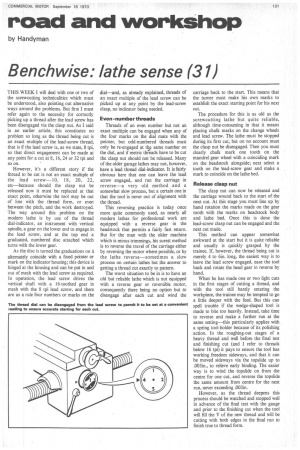
If you've noticed an error in this article please click here to report it so we can fix it.
by Handyman
Benchwise: lathe sense (31)
THIS WEEK I will deal with one or two of the screwcutting technicalities which must be understood, also pointing out alternative ways around the problems. But first I must refer again to the necessity for correctly picking up a thread after the lead screw has been disengaged via the clasp nut. As I said in an earlier article, this constitutes no problem so long as the thread being cut is an exact multiple of the lead-screw thread, that is if the lead screw is, as we state, 8 tpi, so that direct engagement can be made at any point for a cut at 8, 16, 24 or 32 tpi and so on.
However, it's a different story if the thread to be cut is not an exact multiple of the lead screw-10, 18, 20, 22, etc—because should the clasp nut be released now it must be replaced at that exact point, otherwise the tool may be out of line with the thread form, or even between the pitch, and the work destroyed. The way around this problem on the modern lathe is by use of the thread dial-indicator, an instrument with vertical spindle, a gear on the lower end to engage in the lead screw, and at the top end a graduated, numbered disc attached which turns with the lower gear_ As the disc is turned the graduations on it alternately coincide with a fixed pointer or mark on the indicator housing; this device is hinged at the housing and can be put in and out of mesh with the lead screw as required. In operation, the lead screw drives the vertical shaft with a 16-toothed gear in mesh with the 8 tpi lead screw, and there are as a rule four numbers or marks on the dial—and, as already explained, threads of an exact multiple of the lead screw can be picked up at any point by the lead-screw clasp, no indicator being needed.
Even-number threads Threads of an even number but not an exact multiple can be engaged when any of the four marks on the dial mate with the pointer, but odd-numbered threads must only be re-engaged at flip same number on the dial, and if metric threads have to be cut the clasp nut should not be released. Many of the older garage lathes may not, however, have a lead thread dial-indicator. It is fairly obvious here that one can leave the lead screw engaged, and run the carriage in reverse—a very old method and a somewhat slow process, but a certain one in that the tool is never out of alignment with the thread.
This reversing practice is today once more quite commonly used, as nearly all modern lathes for professional work are equipped with a reverse gear in the headstock that permits a fairly fast return. But for the man with the older machine which is minus trimmings, his surest method is to reverse the travel of the carriage either by reversing the motor where possible, or by the lathe reverse—sometimes a slow process on certain lathes but the answer to getting a thread cut exactly to pattern.
The worst situation to be in is to have an old but reliable lathe which is not equipped with a reverse gear or reversible motor, consequently there being no option but to disengage after each cut and wind the carriage back to the start_ This means that the turner must make his own marks to establish the exact starting point for his next Cut.
The procedure for this is -as old as the screwcutting lathe but quite reliable, although time-consuming in that it means placing chalk marks on the change wheels and lead screw. The lathe must be stopped during its first cut, but on no account must the clasp nut be disengaged_ Then you must clearly chalk mark one tooth on the mandrel gear wheel with a coinciding malt on the headstock alongside; next select a tooth on the lead-screw gear and make a mark to coincide on the lathe bed.
Release clasp nut The clasp nut can now be released and the carriage wound back to the start of the next cut. At this stage you must line up by hand rotation the marks made on the gear tooth with the marks on headstock body and lathe bed_ Once this is done the lead-screw clasp nut can be engaged and the next cut made.
This method can appear somewhat awkward at the start but it is quite reliable and usually is quickly grasped by the trainee. If, however, the thread being cut is merely 4 to 6in. long, the easiest way is to leave the lead screw engaged, ease the tool back and rotate the head gear in reverse by hand.
When he has made one or two light cuts in the first stages of cutting a thread, and with the tool still barely entering the workpiece, the trainee may be tempted to go a little deeper with the feed. But this can spell trouble if the wedge-shaped tool is made to bite too heavily. Instead, take time to reverse and make a further run at the same setting—this particularly applies with a spring tool-holder because of its polishing action. In the roughing-out stages of a heavy thread and well before the final test and finishing cut (and I refer to threads below 16 tpi) it pays to ensure the tool has working freedom sideways, and that it can be moved sideways via the topslide up to .003in., to relieve early binding. The easier way is to wind the topslide on from the centre for one cut, and reverse the topslide the same amount from centre for the next ran, never exceeding .003in.
However, as the thread deepens this process should be watched and stopped well in advance of the final test with the gauge and prior to the finishing cut when the tool will fill the V of the new thread and will be cutting with both edges in the final run to finish true to thread form.