Cleaning up our act
Page 36
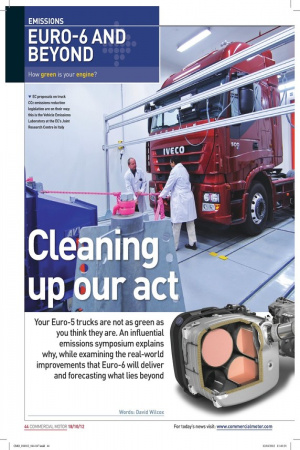
Page 37
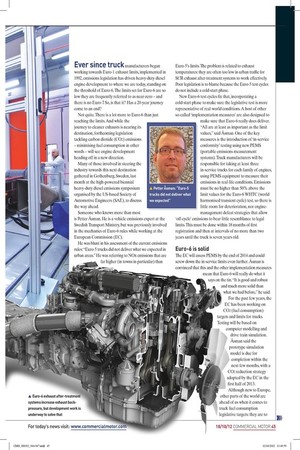
Page 38
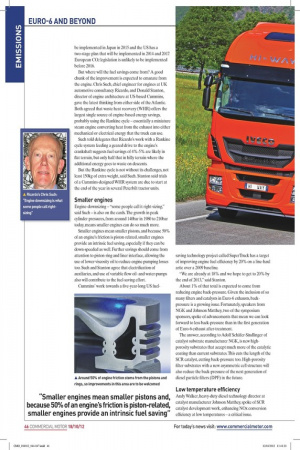
Page 39
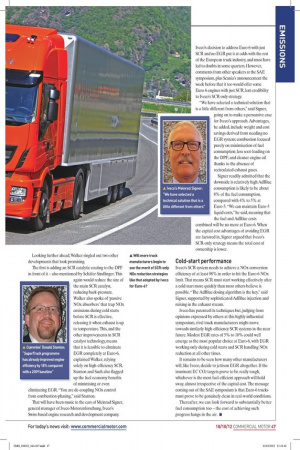
If you've noticed an error in this article please click here to report it so we can fix it.
Your Euro-5 trucks are not as green as you think they are. An influential emissions symposium explains why, while examining the real-world improvements that Euro-6 will deliver and forecasting what lies beyond
Ever since truck manufacturers began working towards Euro-1 exhaust limits, implemented in 1992, emissions legislation has driven heavy-duty diesel engine development to where we are today, standing on the threshold of Euro-6. The limits set for Euro-6 are so low they are frequently referred to as near-zero – and there is no Euro-7. So, is that it? Has a 20-year journey come to an end?
Not quite. There is a lot more to Euro-6 than just reaching the limits. And while the journey to cleaner exhausts is nearing its destination, forthcoming legislation tackling carbon dioxide (CO2) emissions – minimising fuel consumption in other words – will see engine development heading off in a new direction.
Many of those involved in steering the industry towards this next destination gathered in Gothenburg, Sweden, last month at the high-powered biennial heavy-duty diesel emissions symposium organised by the US-based Society of Automotive Engineers (SAE), to discuss the way ahead.
Someone who knows more than most is Petter Åsman. He is a vehicle emissions expert at the Swedish Transport Ministry, but was previously involved in the mechanics of Euro-6 rules while working at the European Commission (EC).
He was blunt in his assessment of the current emissions rules: “Euro-5 trucks did not deliver what we expected in urban areas.” He was referring to NOx emissions that are far higher (in towns in particular) than Euro-5’s limits. The problem is related to exhaust temperatures: they are often too low in urban traffic for SCR exhaust after-treatment systems to work effectively. Poor legislation is to blame because the Euro-5 test cycles do not include a cold-start phase.
New Euro-6 test cycles fix that, incorporating a cold-start phase to make sure the legislative test is more representative of real-world conditions. A host of other so-called ‘implementation measures’ are also designed to make sure that Euro-6 really does deliver. “All are at least as important as the limit values,” said Åsman. One of the key measures is the introduction of ‘in-service conformity’ testing using new PEMS (portable emissions measurement systems). Truck manufacturers will be responsible for taking at least three in-service trucks for each family of engines, using PEMS equipment to measure their emissions in real-life conditions. Emissions must be no higher than 50% above the limit values for the Euro-6 WHTC (world harmonised transient cycle) test, so there is little room for deterioration, nor enginemanagement defeat strategies that allow ‘off-cycle’ emissions to bear little resemblance to legal limits. This must be done within 18 months of first registration and then at intervals of no more than two years until the truck is seven years old.
Euro-6 is solid
The EC will assess PEMS by the end of 2014 and could screw down the in-service limits even further. Åsman is convinced that this and the other implementation measures mean that Euro-6 will really do what it says on the tin. “It is good and robust and much more solid than what we had before,” he said. For the past few years, the EC has been working on CO2 (fuel consumption) targets and limits for trucks. Testing will be based on computer modelling and drive train simulation. Åsman said the prototype simulation model is due for completion within the next few months, with a CO2 reduction strategy adopted by the EC in the first half of 2013.
Although new to Europe, other parts of the world are ahead of us when it comes to truck fuel consumption legislative targets: they are to be implemented in Japan in 2015 and the US has a two-stage plan that will be implemented in 2014 and 2017. European CO2 legislation is unlikely to be implemented before 2016.
But where will the fuel savings come from? A good chunk of the improvement is expected to emanate from the engine. Chris Such, chief engineer for engines at UK automotive consultancy Ricardo, and Donald Stanton, director of engine architecture at US-based Cummins, gave the latest thinking from either side of the Atlantic. Both agreed that waste heat recovery (WHR) offers the largest single source of engine-based energy savings, probably using the Rankine cycle – essentially a miniature steam engine converting heat from the exhaust into either mechanical or electrical energy that the truck can use.
Such told delegates that Ricardo’s work with a Rankine cycle system feeding a geared drive to the engine’s crankshaft suggests fuel savings of 4%-5% are likely in flat terrain, but only half that in hilly terrain where the additional energy goes to waste on descents.
But the Rankine cycle is not without its challenges, not least 150kg of extra weight, said Such. Stanton said trials of a Cummins-designed WHR system are due to start at the end of the year in several Peterbilt tractor units.
Smaller engines
Engine-downsizing – “some people call it right-sizing,” said Such – is also on the cards. The growth in peak cylinder pressures, from around 140bar in 1980 to 210bar today, means smaller engines can do so much more.
Smaller engines mean smaller pistons, and because 50% of an engine’s friction is piston-related, smaller engines provide an intrinsic fuel saving, especially if they can be down-speeded as well. Further savings should come from attention to piston-ring and liner interface, allowing the use of lower-viscosity oil to reduce engine pumping losses too. Such and Stanton agree that electrification of auxiliaries, and use of variable flow oiland water-pumps also will contribute to the fuel-saving effort.
Cummins’ work towards a five-year-long US fuel saving technology project called SuperTruck has a target of improving engine fuel efficiency by 20% on a line-haul artic over a 2009 baseline.
“We are already at 18% and we hope to get to 20% by the end of 2013,” said Stanton.
About 1% of that total is expected to come from reducing engine back-pressure. Given the inclusion of so many filters and catalysts in Euro-6 exhausts, backpressure is a growing issue. Fortunately, speakers from NGK and Johnson Matthey, two of the symposium sponsors, spoke of advancements that mean we can look forward to less back-pressure than in the first generation of Euro-6 exhaust after-treatment.
The answer, according to Adolf Schäfer-Sindlinger of catalyst substrate manufacturer NGK, is new highporosity substrates that accept much more of the catalytic coating than current substrates. This cuts the length of the SCR catalyst, cutting back-pressure too. High-porosity filter substrates with a new asymmetric cell structure will also reduce the back-pressure of the next generation of diesel particle filters (DPF) in the future.
Low temperature efficiency
Andy Walker, heavy-duty diesel technology director at catalyst manufacturer Johnson Matthey, spoke of SCR catalyst development work, enhancing NOx conversion efficiency at low temperatures – a critical issue. Looking further ahead, Walker singled out two other developments that look promising.
The first is adding an SCR catalytic coating to the DPF in front of it – also mentioned by Schäfer-Sindlinger. This again would reduce the size of the main SCR catalyst, reducing back-pressure. Walker also spoke of ‘passive NOx absorbers’ that trap NOx emissions during cold starts before SCR is effective, releasing it when exhaust is up to temperature. This, and the other improvements in SCR catalyst technology, means that it is feasible to eliminate EGR completely at Euro-6, explained Walker, relying solely on high-efficiency SCR. Stanton and Such also flagged up the fuel economy benefits of minimising or even eliminating EGR. “You are de-coupling NOx control from combustion-phasing,” said Stanton.
That will have been music to the ears of Meinrad Signer, general manager of Iveco Motorenforschung, Iveco’s Swiss-based engine research and development company.
▲ Cummins’ Donald Stanton:
“SuperTruck programme has already improved engine efficiency by 18% compared with a 2009 baseline”
Iveco’s decision to address Euro-6 with just SCR and no EGR put it at odds with the rest of the European truck industry, and must have led to doubts in some quarters. However, comments from other speakers at the SAE symposium, plus Scania’s announcement the week before that it too would offer some Euro-6 engines with just SCR, lent credibility to Iveco’s SCR-only strategy.
“We have selected a technical solution that is a little different from others,” said Signer, going on to make a persuasive case for Iveco’s approach. Advantages, he added, include weight and cost savings derived from needing no EGR system; combustion focused purely on minimisation of fuel consumption; less soot-loading on the DPF; and cleaner engine oil thanks to the absence of recirculated exhaust gases.
Signer readily admitted that the downside is relatively high AdBlue consumption is likely to be about 8% of the fuel consumption, compared with 4% to 5% at Euro-5. “We can maintain Euro-5 liquid costs,” he said, meaning that the fuel and AdBlue costs combined will be no more at Euro-6. When the capital cost advantages of avoiding EGR are factored in, Signer argued that Iveco’s SCR-only strategy means the total cost of ownership is lower.
Cold-start performance
Iveco’s SCR system needs to achieve a NOx conversion efficiency of at least 98% in order to hit the Euro-6 NOx limit. That means SCR must start working effectively after a cold start more quickly than most others believe is possible. “The AdBlue dosing algorithm is the key,” said Signer, supported by sophisticated AdBlue injection and mixing in the exhaust stream.
Iveco has patented its techniques but, judging from opinions expressed by others at this highly influential symposium, rival truck manufacturers might move towards similarly high-efficiency SCR systems in the near future. Modest EGR rates of 5% to 10% could well emerge as the most popular choice at Euro-6, with EGR working only during cold starts and SCR handling NOx reduction at all other times.
It remains to be seen how many other manufacturers will, like Iveco, decide to jettison EGR altogether. If the imminent EC CO2 targets prove to be really tough, whichever is the most fuel-efficient approach will hold sway, almost irrespective of the capital cost. The message coming out of the SAE symposium is that Euro-6 trucks must prove to be genuinely clean in real-world conditions.
Thereafter, we can look forward to substantially better fuel consumption too – the cost of achieving such progress hangs in the air. n