Vehicle maintenance (3)
Page 50
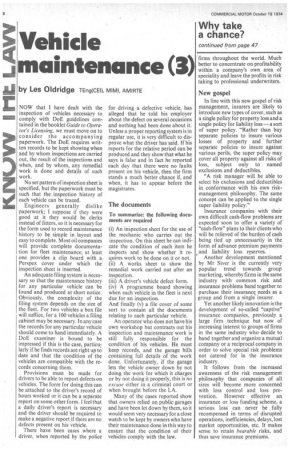
If you've noticed an error in this article please click here to report it so we can fix it.
by Les Oldridge TEng(CE1), MIMI, AMIRTE NOW that I have dealt with the inspection of vehicles necessary to comply with DoE guidelines con tained in the booklet Guide to Operator's Licensing, we must move on to consider the accompanying paperwork. The DoE requires written records to be kept showing when and by whom inspections are carried out, the result of the inspections and when, and by whom, any remedial work is done and details of such work.
No set pattern of inspection sheet is specified, but the paperwork must be such that the inspection history of each vehicle can be traced.
Engineers generally dislike paperwork; I suppose if they were good at it they would be clerks instead of fitters, so it is necessary for the form used to record maintenance history to be simple in layout and easy to complete. Most oil companies will provide complete documenta tion for fleet maintenance; at least one provides a clip board with a; Perspex cover under which the inspection sheet is inserted.
An adequate filing system is necessary so that the maintenance history for any particular vehicle can be found and produced at short notice. Obviously, the complexity of the filing system depends on the size of the fleet. For two vehicles a box file will suffice, for a 100 vehicles a filing cabinet may be necessary. In any case the records for any particular vehicle should come to hand immediately. A DoE examiner is bound to be impressed if this is the case, particularly if he finds records are right up to date and that the condition of the vehicles are compatible with the records concerning them.
Provisions must be made for drivers to be able to report defects on vehicles. The form for doing this can be attached to the driver's record of hours worked or it can be a separate report on some other form. I feel that a daily driver's report is necessary and the driver should be required to make a negative report if there are no defects present on his vehicle.
There have been cases where a driver, when reported by the police for driving a defective vehicle, has alleged that he told his employer about the defect on several occasions and nothing had been done about it. Unless a proper reporting system is in regular use, it is very difficult to disprove what the driver has said. If his reports for the relative period can be produced and they show that what he says is false and in fact he reported each day that there were no faults present on his vehicle, then the firm stands a much better chance if, and when, it has to appear before the magistrates.
The documents
To summarize: the following documents are required (i) An inspection sheet for the use of the mechanic who carries out the inspection. On this sheet he canindicate the condition of each item he inspects and show whether it requires work to be done on it or not.
(ii) A works sheet to show the remedial work carried out after an inspection.
(iii) A driver's vehicle defect form.
(iv) A programme board showing when each vehicle in the fleet is next due for an inspection.
And finally (v) a file cover of some sort to contain all the documents relating to each particular vehicle.
An operator who does not have his own workshop but contracts out his inspection and maintenance work is still fully responsible for the condition of his vehicles. He must keep records, and the garage hills containing full details of the work done. Unfortunately, if the garage lets the vehicle owner down by not doing the work for which it charges or by not doing it properly, this is no excuse either in a criminal court or when brought before the LA.
Many of the cases reported show that owners relied on public garages and have been let down by them, so it would seem very necessary for a close watch to be kept by owners who have their maintenance done in this way to ensure that the condition of their vehicles comply with the law.